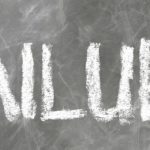
7 Tips for Avoiding CMMS/EAM Failure
Many maintenance organizations invest in a CMMS/EAM in hopes that it will solve their maintenance management problems, only to discover that the software fails to deliver the desired results. Faulty software might be to blame for some CMMS implementation failures, but more often than not, the problems begin well before the software is even implemented. Here are 7 tips for avoiding CMMS failure:
1. Carefully select CMMS maintenance software
There are hundreds of CMMS/EAM software vendors competing for your business, so it can be time-consuming to narrow down your list of potential vendors. One step that can make the process of shopping around for maintenance software easier is creating a reference document that outlines your organization’s requirements. Evaluate and select CMMS software by matching a system’s capabilities with your organization’s specific needs rather than basing your decision on generic demos that aren’t relevant to your organization’s practices and procedures. Additionally, take any software you’re considering for a test drive to ensure that it offers the desired functionality.
2. Plan for your future needs
Your organization’s requirements will undoubtedly change over time. Carefully consider your future needs and whether a CMMS system and vendor will be capable of meeting them. Maintenance software is a significant investment, so it’s crucial to choose a system that provides you with a worthwhile ROI in the long run.
3. Obtain support from management
Convince management of the benefits of using maintenance software and translate those benefits into bottom-line savings. Senior management must be 100% committed to the success of CMMS implementation because they will play a key role in monitoring the project as well as ensuring that the required funding and internal resources are in place.
4. Properly plan your CMMS/EAM implementation project
Many companies can put their best foot forward in avoiding CMMS failure by properly planning. Determine the “what”, “why”, “who”, and “how” of your maintenance software implementation early in the process and set implementation goals and key milestones. Develop a plan for gathering all of the data employees will need to enter into the CMMS and assemble an internal implementation team that consists not only of IT personnel, but also of end users.
5. Hire experienced consultants to handle implementation
Although relying solely on internal resources during the implementation process can bring costs down in the beginning, it could cost you dearly in the long run. Software vendors/consultants are generally far better equipped than in-house personnel to manage the implementation process because they have been there, done that and are capable of completing implementation tasks on time and on budget. The ideal consultant is one who is well versed in CMMS/EAM implementation, maintenance best practices, and your industry.
6. Conduct comprehensive user training
Many implementation methodologies focus on going live with the system in the shortest amount of time possible, but if a system is implemented with minimal training, maintenance technicians may not feel comfortable and confident using it. It’s ideal to invest in your software vendor’s training services to lower the learning curve and provide each user with role-based training that helps them do their jobs more efficiently.
7. Continuously evaluate the system after implementation
Conduct system evaluation on a regular basis after implementation to evaluate the effectiveness of your CMMS and get maximum value from your investment. You could use a bench marking tool to determine how well your CMMS is supporting your maintenance process and identify ways to enhance your current use of the system.
Make sure you’re avoiding CMMS failure by partnering with the right software vendor. DPSI’s Professional Services Team supports your maintenance department through all phases of the CMMS/EAM implementation process to ensure that you’re able to make the most of our software. Contact us today to learn more about avoiding CMMS failure, or for more information about our products and services.
Leave a Reply