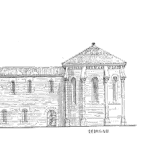
The first time I changed the oil filter of my car (first car in high school) I smashed my knuckles against a grimy block of metal. More than once. It may have been my lack of experience or improper tools. Or, it may have been a rather poor design.
Watching the Indy 500, especially the pit stops, I quickly realized there has to be something different about those cars that lets them change tires, add oil & fuel, and clean the windshield in less time than it took me to get under the hood and find the oil filter. The cars were designed differently and that is what permitted the difference in service time.
In order to increase availability and minimize the cost of maintenance, we have to deliberately design the system to accommodate the needs of maintenance.
Here are 8 factors to consider when designing a system that will require maintenance.
1. Standardization
Select from the smallest set of parts (one screw instead of 10 different types of screws) with as much compatibility as possible. Minimize spare parts inventory is just one benefit.
Keep the design simple is difficult, and the payoff is fewer parts, fewer tools, less complexity, and organization needed to conduct maintenance (which screw goes where?).
2. Modularization
Create a set of standard sizes, shapes, modular units. Lego bricks come to mind.
If we expect to different models with different features, using a standard structure allows the interchange of compatible parts to alter functionally without changing the majority of the product. A good example is light bulbs. You can select the functional bulbs (brightness, intensity, color, etc.) and they will fit in the same socket.
3. Functional packaging
Gather all the required elements to complete a maintenance task in one kit. If I need washers, o-rings, and pumper’s grease to complete a faucet repair, having all the items in one package helps me complete the task quickly (without the need to run to the store to pick up the forgotten item.)
4. Interchangeability
If you have to create a custom fit for a part, consider the ramifications. Single source, lack of compatibility with other similar functioning parts, another spare part in inventory, and limitations on future design changes if you want to stay in that custom form factor.
Select parts that are useful for a range of products or applications. Manage and control the dimensional and functional design tolerances.
5. Accessibility
Bruised knuckles are one risk of getting this wrong.
If an item requires replacement or adjustment as part of the expected maintenance, then it should permit access. Consider tools, lighting, environment, and experience of a maintenance crew. Providing access panels is one factor, safety another.
6. Malfunction annunciation
A key step in performing maintenance is to know what caused the problem or which parts are damaged and require replacement.
A bicycle flat tire is obvious to visual inspection or you may notice a change in the sound and feel of the ride. On complex systems which circuit board requires replacement may not be obvious. Minimizing the need for inspection tools and diagnostic tasks minimizes the time/cost of the corrective maintenance tasks. Let the system inform the technician what requires attention.
7. Fault isolation
There are two parts to this factor. One, make the system as informative as possible such that it not only signals a failure mode, it also narrows down the possible failure mechanisms. Replacing a blown fuse doesn’t fix the problem and just finding the problem may take significant time.
Second, a failure in one part of a system can cause failure of other elements in the system.
When possible, contain the damage to minimize the amount of damage caused by a failure of one item.
8. Identification
Name the parts with unique identifiers. This streamlines documentation, procedures, and maintenance tasks.
Be consistent and provide meaningful or memorable naming conventions to avoid confusion.
Summary
There are always the considerations of time, complexity, cost and functionality, in a design. Considering these factors during the design process provides a meaningful basis to balance the needs of maintenance as we attempt to restore a system to service.
The cost of ownership is a function of main tenability and during the design process, you have the ability to minimize the number of bruised knuckles that occur.
Related:
Preventive Maintenance or PM Goals and Activities (article)
CRE Primer Error (article)
Reliability Centered Maintenance (article)
I’m curious, is there a semantic web application or software system to take all this glorious information and represent it in an ontology applicable to the domain of design, such that you get a Clippy virtual assistant or code linter bugging you about these during your design process?
?: Looks like you’re designing a physical item with [3] different screw types. Try to use less!
Why? Because it aligns with design brief directives:
A) As much compatibility as possible please! [@Pennypacker says on 27.09.2016]
and the following directives (inherited from General Industrial Design Directives):
1) Cost savings: You minimize the spare parts inventory
2) Fewer parts
3) Fewer tools
4) Less complexity
Thanks for the comment and kind words. None that I know about. I’m sure the DFM work found in the Boothroyd Dewhurst approach has applications out there. I would suspect there are a few design review assessment tools out there too.
Cheers,
Fred
Thanks for the directions!
Which of the following maintainability attributes is most preferred in aircraft maintenance : Accessibility ,Diagnosibility and Fault Tolerance?
If compared in pairs, i.e. between Accessibility & Diagnosibility, Accesibility & Fault Tolerance etc
Hi Abhishek,
Interesting question and one that does not have a simple answer. Each organization either designing or maintaining equipment will have different objectives, goals, and constraints that will shift which attributes to prefer. The trouble is, that same organization may find as conditions change the preferred attributes change as well.
A general answer is to find a balance of these attributes along with cost that is resilient in a wide range of constraints and conditions.
Cheers,
Fred