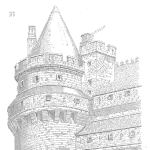
A form of testing that reduces the time till results are known, ALT provides a means to estimate the failure rate over time of a product without resorting to normal use conditions and the associated duration.
For example, solar photovoltaic cells should operate for 25 years without failure. The product development time is less than a year for a new panel and the team wants to estimate the reliability of the cells over the 25-year duration.
Why is it better than other methods?
A simplistic way to determine the reliability is to set up and operate solar systems for 25 years and track the number of failures over time. This isn’t practical or useful.
Another method is to only test units as above for one year then use the available information to make a decision. While product failures may occur (most likely due to manufacturing and installation errors) it will not be useful for delimitation of coatings or sealants, solder joint fatigue, PV cell degradation, and other longer term failure mechanisms. While we could make an estimate, it would not be very accurate beyond the one year of use replicated in the testing.
Two words: Time compression
Accelerated testing uses a variety of methods to compress time. Using the solar cell example, if UV radiation degrades one of the coatings, we can ‘accelerate’ this by exposing the cells and coatings to UV radiation more often per day than in normal use. If in normal use the panel would have 10 hours of direct daylight per 24 hour day, then using UV lamps, we could expose the units 24 hour per day, for a 2.4 x acceleration. Thus instead of 25 years, we would require little more than 10 years for the testing.
Still not good enough.
If we explore the UV damage mechanism, it may be part of a chemical reaction that clouds the coating. This chemical reaction most likely can be accelerated with temperature (Arrhenius rate equation – remember your chemistry). With a little work, we find the expected coating temperature during use is 40°C or less 90 percent of the time. By increasing the temperature (and not melting the coating – watch those phase transitions) we may find another 10x of acceleration. The specifics of the acceleration is related to the activation energy of the specific chemical reaction, the testing temperature, and the use temperature.
Use ALT to its best ability
Therefore, with a little understanding of the use conditions (10 hours of daylight per day) and the specific failure mechanism in question (UV and temperature driven chemical reaction) we can achieve a 24x acceleration factor. This will still take a little more than a year to fully test out to 25 years, yet the team may be able to use the data out to 24 years as a rough estimate and update when the final results become available.
This is just a short example and mainly an example of my approach to accelerated life testing. There is a lot more to ALT design, yet the most important by far is the understanding of the failure mechanism.
Related:
Reading a Datasheet (article)
Sources of Reliability Data (article)
Sample Size – success testing (article)
Regarding accelerated life test plan it will be helpful if you could give your suggestion on below queries
1.How to select the failure distribution before starting accelerated test for new component which does not have a previous history
2.How to have the scale or shape parameter for new component which does not have a previous history
3.These two inputs are required for creating a optimum test plan , kindly give your suggestion
4.Once the test plan is established , what can be the allowable variance or standard error
5.How to adjust the sample size for the confidence interval and failure percentage we need to know
Ravi – there are a couple of really good questions here! But the first thing we need to know is what decision is your ALT informing? Are you choosing between two different materials? Are you trying to assess the reliability of something in ‘normal’ conditions? Are you trying to see if the reliability of something exceeds a requirement in ‘normal’ conditions? There are several other questions that might be answered by ALT … so to answer yours can you give us some further insight?
Hi christopher Jackson I am trying to access the reliability of something in normal use condition.
But to answer a couple of specifics … your ‘scale’ parameter is based on your ‘life model’ which describes how reliability changes when you accelerate testing through (for example) increasing temperature. The ‘failure’ model (which I presume you mean to be the model that describes the random nature of your item failing around the ‘scale’ parameter) is going to be a wear-out probability distribution model. Think normal, lognormal or Weibull with a shape parameter greater than 1.5. And your sample size is all about the decision you are trying to inform. Hope this helps!
Thanks Christopher Jackson that cleared a lot
No worries Ravi … let me know if there is anything else you need to talk about.
ALT from some reliability textbooks say that we need a few (at least two) levels of stress to 1) obtain the parameters of the acceleration life factor and 2) if the life data for each levels of stress will fit to a set of parallel lines.
However, based on my work experience, I have never seen the reliability engineers used different levels of stressor for the ALT.
What’s your recommend best practice?
Hi Lee,
There are many ways to conduct ALT – if you have a good (actually known to be representative of the specific failure mechanisms being accelerated and of interest for the study) then using only one stress level is fine. This places a very large assumption that the model to translate the accelerated results actually are meaningful and accurate – which is way too often not the case in my expereince.
Using only two stress levels assumes you have a linear response between stress level and time to failure – which means not running a third stress level means you cannot check that assumption.
Everything we do in ALT that is different or further away from how customers will use the product creates opportunities for our assumptions to lead us astray. Running multiple stress levels permits us to check more assumptions and confirm our model at high stress is creating meaningful results or not.
I routinely run multiple stress levels and once the results and assumptions and model all check out, then can streamline to one or two stress levels based on that knowledge. Pulling a model from a book or paper and assuming an acceleration factor so one can run a single stress is very nearly always going to end with results that are just plain misleading. And, one then has no concrete way to check.
ALTs are expensive experiments – take the time to do them well in order to create information that is useful and meaningful.
cheers,
Fred
I am so happy to hear your response.
I was questioning the AF (acceleration factor) for some of our one-stressor ALTs, and people just said they assumed it is metal fatigue or plastic degradation …so they just assumed the AF. The worse part was the assumption that the ALT will actually accelerate the particular failure mode.
Here is what I think we should have for the following at least:
1) the life vs stress plot, and
2) the fitting of life data of each stressor with similar parameters (are they parallel on the life data plot)
What do you think?
Hi Lee,
The hard part of just guessing or assuming the acceleration factor and then running just one stress level – it you won’t know of far off the results are until customer use the product at normal stress (second level), which is a very expensive way to check an assumption.
Unless there is very solid evidence to support using an acceleration factor or model (such as what you propose) the results are very likely meaningless and misleading.
cheers,
Fred
Thank you!
One following up question:
In the NPI phase (Proto, EVT…), when is the better time to perform the quantitative accelerated life testing?
Hi Lee, as soon as possible for two reasons – ALT’s (often) take time from start to results. Second, you want the team to have time to deal with the results – good or bad. Ideally, you can characterize a new material or component well before the design starts for a new product, second best is as soon as the new item is being considered and has a question on longevity. cheers, Fred
Fantastic article, Fred! In essence, an accelerated lifetime test (ALT) is a means to speed up time so that we can determine whether a thing can endure that long without having to wait 20-30 years. Such testing is frequently carried out under demanding circumstances, including open circuit voltage (OCV), high current density, high temperature, and similar circumstances.