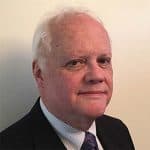
Introduction
Automotive Electronic parts are qualified before usage in serial production. When product quality and reliability are poor, then assembly problems, high warranty costs, poor service, and recalls occur. The OEM’s and suppliers followed different qualification plans. Ford, GM, and Chrysler and large parts suppliers started the Automotive Electronics Council (AEC) in the 1990’s, with the mission of defining a suite of common qualification tests.
The first qualification standard was Q100, which defined stress tests for electronic components containing integrated circuits. These components are in every electronic control module, some sensors, entertainment systems, safety systems, and, in the future, autonomous driving systems.
Failure is defined as a device not meeting individual device specifications. Failure modes could be device that is inoperative; displays intermittent, unexpected, or erratic behavior; or has degrade variables that violate a specification.
One of my concerns is the large sample sizes specified for environmental and life stress tests.
Test Sample Sizes
The environmental and life stress tests specify sample sizes of 45, 231, and 2400. These sample sizes are totally compatible with R95/C90, R99/C90, and R99.9/C90 verification targets. The sample sizes may be calculated using the success – run equation is:
Rn=(1−C)
(1)
In equation (1), equation is modified to calculate the test sample size for any desired reliability and confidence level:
n=ln(1−C)/ln(R)
(2)
While mathematically correct, the tests sample sizes are excessive. For example, the Early Life Failure Rate (ELFR) test specifies 800 samples/lot from 3 lots, or 2400 parts. This is consistent with a R99.9/C90 target. Other tests, require 77 samples/lot from 3 lots, or a total of 231 samples. This is consistent with R99/C90. Other tests require 45 parts from a single lot to support R95/C90.
Test-to-Bogy (TTB)
AEC Q100 follows the TTB without failures test strategy for environmental and lift tests common in the 1990’s. The device is checked for conformance to specified operation and multiple parameters are monitored to verify the device conforms to specification limits. At a minimum this occurs at the beginning of the test, assuring only conforming parts were being tested, and end of the test to determine in the parts were still conforming.Parameters are monitored continuously or at intervals during a test to assure the values remain within specification. Figure 1 shows a group of parts that started with similar values, but ended within different groups.

While TTB was mandated at the supplier level, at the OEM level (Ford, Chrysler, GM…), the TTB tests were replaced with more efficient methods. Some alternative verification approaches are discussed here.
Test-to-failure (TTF)
Using TTF, parts are stressed until they fail. If failures occur, then the failure times are known. When a failure occurs before the test life bogy, then the qualification test is failed. When parts fail after the life test bogy, the failures can be analyzed to determine the Rxx/C90 level at one life bogy. If different failure modes occur, then they are analyzed separately to assure conformance.
A detailed analysis of failed parts may reveal part design or manufacturing weaknesses. This is an opportunity for engineers to correct design flaws and improve the manufacturing process. TTF is better than TTB because the supplier learns how to avoid failure.
In the Temperature Cycle (TC), Q100 required 231 parts for TTB. How many failures are required for a TTF? The answer depends on the R/C verification target; the analytic method (generally Weibull); and corporate policy. For example, using a Weibull probability plot, a failure fit line can be calculated with 3 failures. With 3 data points, the characteristic life θ, slope β, and an estimate of variation σ can be determined. However, because the sample size is small, the confidence limits would be large. To reduce test variation, a larger test sample size is required. Some OEMs require 6 failures, which implies 6 or more samples tested.
Test-to-Extended-Bogy (TTEB)
A concern with TTF is that the testing time can’t be calculated. Testing is complete when the desired number of failures occur, but a very reliable part may never fail. To limit test time, TTEB is used. Given the original test duration and sample size and assuming a Weibull slope β, an equivalent extended test time and sample size may be calculated. This is accomplished by combining a Weibull model with the success – run equation to yield:
nn0=(t0t)β
(3)
The β could be determined from other experimental data for the failure mode, estimates derived from technical publications, or possibly using a corporate standard value. Using β, the original bogy t0, the original test sample size n0, and the extended test time t, then n is calculated.
For example, the high temperature operating life (HTOL) specifies 231 samples (from 3 batches) tested for 1,000 hours at Tmax. If β=2 and the test is run for 2,000 hours, then 58 samples is sufficient to support R95/C90 at 1,000 hours. This is a 75% reduction is test samples, fixtures, and equipment. The primary compromise is longer test duration.
Degradation Analysis (DA)
In DA, the parametric data collected is used to detect degradation patterns, estimate the effect of factors of variation, and estimate the residual variation. Time series plots of a parameter displays the degradation pattern. Some common patters are:
Linear: | y=a⋅x+b |
Exponential: | y=b⋅ea⋅x |
Power: | y=b⋅xa |
Logarithmic: | y=a⋅ln(x)+b |
The parametric data would be plotted to determine the best degradation model. In other situations, the data may need to be analyzed to determine the model with the highest goodness of fit. Once the model is selected, analysis provides information on parameter variation over the test duration. Design of Experiments, regression, and covariance analysis would be used.
Data group factors should be considered. For example, a Temperature Cycling (TC) test specifies using 3 part lots cycled between operating temperatures of $–55^oC and Tmax. Each lot become a grouping factor. The statistical significance of the lot variation needs to be determined. The analysis provides a common degradation equation or a unique degradation for each group.
Distribution intervals characterizing P-percentile population limits need to be determined. These intervals become population bounds about the best fit lines and/or batch means during the test. For a lot, the acceptance region is calculated using the mean at each measurement time and the sigma value based on the residual variation. For the normal distribution, an acceptance interval would span (μ−k⋅σ,μ+k⋅σ) where μ is a group mean at time t and k is based on the probability (reliability) desired, table 1:
Probability | K |
0.90 | 1.645 |
0.95 | 1.960 |
0.99 | 2.576 |
0.999 | 3.291 |
When all of these intervals are contained within the parameter specifications, then the test is passed. Figure 2 shows the results where the lots were not significant, but temperatures were an important factor.

Figure 2 model fits can be projected forward to obtain failure distributions for each temperature. Again, failure is when a parameter fails to conform to specification limits.
Conclusions:
Considerable cost reductions and test efficiencies can be achieved by moving from TTB without failures to Parametric Degradation tests. These alternate test plans meet the qualification intent of Q100 with smaller sample sizes.
Parametric degradation allows one to project the data to predict product life. This is not possible with TTB.
Some qualification should consider upstream actions such as process controls and process capability as evidence of process stability. If the upstream processes are not stable and out of statistical control, the quality of future product is not assured. Reliability tests should not be substituted for other validated statistical methods.
Dennis Craggs, Consultant
Quality, Reliability and Analytics Services
(810)964-1529
I am glad to finally see where 231 and 2300 come from!
I was curious of the date of your blog. My industry made the change in terminology from “IM” to “ELF” fairly recently and I am wondering if other more mechanical industries switched sooner.
Hi Michael, Dennis posted the article on May 1st, 2022, and I’ll let Dennis address the change in terminology bit. cheers, Fred