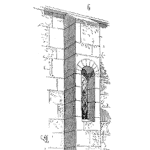
One question that you should consider when planning multiple stress accelerated life test (ALT) is the allocation of test units to the various stresses.
We want to create a model detailing the relationship between stress and time to failure. We also want to project the time to failure estimates to use conditions. Ideally, we test at nominal conditions only and gather time to failure information. We do not have the luxury of time thus explore using ALT.
One method of allocation is to place an equal number of samples with each stress level. Is that the best approach?
General ALT Planning Guidelines
In How to Plan an Accelerated Life Test: Some Practical Guidelines (The ASQC Basic References in Quality Control, Vol. 10) (The Asqc Basic References in Quality Control; V. 10), William Q. Meeker and Gerald J. Hahn outlined a few basic guidelines to consider during ALT planning.
- Restrict the stress range over which the failures that occur across the range, including use conditions are the same. A failure at high stress has the same failure mechanism and essentially the same path to failure. The idea is to avoid phase changes or fundamentally different failure mechanisms. This sets the high stress level.
- For the middle-stress level select a level that is far from the high-stress level (helps to create a better estimate of the relationship slope), yet is sufficiently high to yield about 10% failures within the testing time period.
- The lowest stress level is as close as possible to use stress levels but still expected to generate a few failures during the testing.
For each stress level, we need failures. When you have time, run all units to failure. You can use a ‘guess’ or assumed time to failure model to estimate the number of failures at each stress level for a different number of samples. This is just for planning to aid in selecting appropriate ALT stress levels.
The 4:2:1 Plan for Allocation of Test Units
With three ALT stress levels determined, the question turns to how many samples to allocate to each level. Considering the goal is estimating time to failure distribution at use conditions using a regression model relating time to failure and stress, we improve the accuracy by having a reasonable estimate of the slope of the relationship and by having more information closer to the use conditions.
The distance between stress levels impacts the accuracy of the slope estimate. Using stress levels as far apart as possible improves the statistical regression modeling to estimate the slope.
At each stress, we are attempting to estimate a time to failure distribution. We need failures to do so. The more failures the better. The closer the lowest stress level is to use conditions the less of an extrapolation to use conditions and the lower the probability of failures occurring.
It’s a balancing act or optimization problem with imperfect information.
Meeker and Hahn work out an optimized plan based on just two ALT stress levels. This really only works when you have an accurate estimate of the time to failure distribution and acceleration model. We may not have suitable conditions to ‘optimize’.
Meeker and Hahn then outline an optimum test plan with an equal number of failures per stress level. They recommend using a ratio of 4:2:1 samples for the low: middle:high-stress levels, respectively.
Thus if you have 21 samples available for the ALT place 12 units under the lowest stress condition, 6 in the middle level, and just 3 in the highest level. If the stress levels are selected appropriately you should expect about 3 failure per stress level.
Of course, more samples the better. This will certainly be limited by the number of samples available, cost, testing capability, and measurement facilities.
How do you set up your ALT? Do you use multiple stresses and do you have a favorite algorithm to allocate samples to the various stress level? Share your advice or experience in the comments section below.
References:
William Q. Meeker and Gerald J. Hahn, How to Plan an Accelerated Life Test: Some Practical Guidelines (The ASQC Basic References in Quality Control, Vol. 10) (The ASQC Basic References in Quality Control; V. 10) Milwaukee, WI: ASQC Quality Press.
Fred, for a minute I thought the title of the article might have related to the number you request from management for how many units you need. I have heard from reliability engineers that management will give them one unit for HALT or ALT. the 4:2:1 sample allocations come from this discussion.
RE to management: ” I need four units to perform a good HALT or ALT”
Management: “We do not have the budget for you to potentially damage or destroy 4 units”
RE to management: “Ok, how about two units?”
Management: “We only have the budget for one sample to pass the HALT or ALT testing”
RE to management: “Ok, one sample it is”