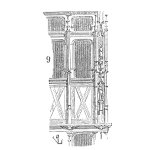
What does asset management have to do with TIME? Everything.
My mentor, John Moubray, taught me that our most valuable resource is TIME. Time is WAY more valuable than money.
How you spend your TIME determines IF and HOW your asset management efforts will pay off. In other words, will your efforts help you achieve the kind of equipment Reliability you’re looking for?
TIME is the great equalizer. Everyone gets 24 hours per day…no matter who you are, where you live, or what circumstances you find yourself in.
Remember…you can always make more money…but you can never make more time.
I remember reading about Dr. Elmer Gates, an American scientist and inventor (1859-1923). He would tell his secretary that he wasn’t to be bothered because he was “sitting for ideas”…and he would do so for two to three hours at a time. The only things on his desk were an open notebook and a pen.
We live in a fast-paced world. There’s information coming at us from just about every direction.
Maybe getting “still” and being quiet so you can “hear” or “feel” ideas and inspirations come through could be the best way to spend some of your time.
Whether or not that is a valuable exercise is up to you. Just remember…time is an “UNrenewable” resource…so be careful how you spend it! ☠️
And here’s the real doozy…how you spend your time is directly proportional to your internal and external circumstances.
Let’s look at this from an Asset Management point of view.
Does your organization suffer from frequent unplanned downtime? How about skyrocketing maintenance costs? What about chronic unreliability? Does your organization live in a “reactive” environment?
Perhaps it’s time to stop and take a look at how your organization is spending its “asset management time” and other valuable resources.
⏱️ Have you taken the TIME to actually define the kind of “Reliability” you want from your equipment?
⌛ Have you taken the TIME to figure out what could (or does) specifically cause failure?
⏰ Have you taken the TIME to figure out if you’re doing the right maintenance at the right time?
⌚ Have you taken the TIME to figure out if any other actions could help (like a new operating procedure)?
Reliability Centered Maintenance (RCM) can help you figure out how you should be spending your TIME…and you DON’T have to apply RCM on every piece of equipment you have…
…you can apply RCM as broadly or as narrowly as necessary…
…apply all 7 steps…
…or just those steps that apply to your situation.
The RCM process is jam-packed with actionable knowledge and it can provide you with necessary skills so YOU can TAKE CONTROL of your equipment.
(Isn’t it time you do maintenance on YOUR terms and NOT on your equipment’s terms?)
Take control of your equipment with these basic Maintenance and Reliability skills.
If you want to change the circumstances about anything, start by taking a look at how you spend your TIME (personally and professionally). It could be a real eye-opener
Leave a Reply