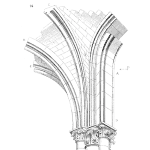
Equipment risk is a reality of every oil or gas well completion, but is this risk the exclusive responsibility of the equipment manufacturer (OEM)? To answer this question, let’s examine the major aspects of equipment risk in more detail. [Read more…]