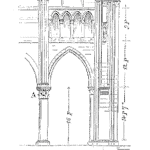
My introduction to reliability engineering was my boss asking me to sort out how long a new product will last in use.
The expectation was it would last for 20 years or more buried in Italian mountain concrete bridges.
My first thought was about living in the Dolomites for 20 years monitoring the performance of the product.
That was quickly dashed as my boss explained he wanted an answer in about 6 months.
Now this was a problem. How do you cheat time to learn about the expected lifetime of a something? Thus started my career in reliability engineering.
Life testing for reliability engineering helps us answer the question how long till failure occurs. Specifically, we find the chance of failure over some duration.
Life testing helps us to know if a printer will operate with low enough failure rate over the warranty period that we will meet our profit targets.
The same testing may help us determine the expected number of units surviving for 5 years, thus continuing the demand for the printer’s ink cartridges.
For the solar power industry, the life testing attempts to prediction failure rates out to 20 to 30 years.
Cochlear implants in children may need to operate 70 or more years. We have business and consumer needs to know the likelihood of an item working as expected over a duration.
Thus we do life testing.
Types of life testing
Life testing takes many forms.
For some systems that may only operate a short time before something fails, simply operating the system under normal conditions allows us to accurately estimate the lifetime.
For other systems, we apply higher than normal stress to accelerate specific a failure mechanism to simulate 20 years of operation.
We make assumptions and use engineering judgment.
We follow previous experimenters insights and models. We attempt to discover the life distribution in an economical and timely manner.
There isn’t one right way to conduct life testing.
Each system and set of materials will respond to the use conditions and stresses in part due to the design, to the assembly, to the installation.
Each system will require a unique approach to estimating the expected life distribution.
Threshold tests
In some cases, we want to know if the system is just good enough.
No big surprises. Or, that the new design is as good as or better than the last design. In these cases, either a binomial-based success test or a comparative test may be appropriate.
Success testing is the operation of a set of samples under a defined set of stresses that may represent a lifetime of use.
For example, a car door may have an expected use over its lifetime of 10,000 open/close cycles.
If we are interested in the wear due the open/close cycles and not concerned about the events that may occur while the door is not opening or closing (assimilation of debris, corrosion, creep, etc.) then a life test may be as simple of cycling a set of doors 10,000 times by eliminating the time the car would otherwise be parked or driving or not having the door opening or closing.
On the other hand, if the door just has to perform better than a previous design and we do not have a specific number of cycles in mind, then cycles the two designs next to each other with the same rates, loads, environments, etc.
As long as the new design lasts longer, however we define failure, then it answers our basic question.
Distribution estimation testing
Another spectrum of testing involves the estimation of the life distribution.
Test enough systems till they fail while tracking the time to failure, allows us to create an estimate of the life distribution.
For complex systems, we may focus on specific failure mechanisms or subsystem and combine the results to create a system life model.
This style of testing is often expensive and time-consuming, yet is the best way to estimate the expected time to failure behavior.
One advantage is the work of previous experimenters for specific failure mechanisms allows us to avoid testing in some cases, or streamline the testing based on existing models.
Assumptions in life testing
The easiest thing to do for life testing is to assume away any and all complexity.
You can quickly create a life estimate, which will not be accurate nor useful.
The best life testing is actually done by the people actually using the system as intended. Unfortunately letting customers test the product may lead to unexpected and unwanted failures.
The idea and value of life testing is to understand the time to failure behavior so we can make necessary improvements before customers discover the life limiting issues.
Fewer assumptions are better and will always become a balance between what is possible within the budget and timeframe allowed and the need to accurately estimate the life distribution.
Be clear about each assumption and the risk involved if that assumption is invalid.
Life testing has risks and as you design or interpret a set of tests, understanding the risks either assumed about the test or designed into the test help use to interpret and use the result well.
While my first project did not result in an extended trip to Italy, it did teach me that there are ways to accelerate, model and estimate the operating life of products.
I’ve learned a lot since that first discussion with the help of many in the reliability field.
Life testing is core to what we do as reliability engineers and a critical task to master.
How are your life tests going? Are you getting the value you expect from them?
Related:
Life Testing Starting Point (article)
Intro to Thermal Cycling Life Testing (article)
Accelerated Life Testing (article)
Leave a Reply