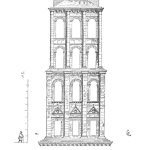
Behavioural Based Safety (BBS) involves peer reviews of fellow workers’ safety practices. You use members of your workforce who take five minutes out of their day to observe a colleague at work and see if they are truly doing safe work practices
Use of a Behaviour Based Safety Program has seen an exponential rise in recent years. A number of eminent psychologists believe deeply in it, and in its ability to gain positive workplace safety results
Workforce behavioural observation, behavioural based safety, and a behaviour based safety program all involve observing people doing their work and seeing the safety behaviours they use. They are a proactive approach for getting workplace safety rather than a reactive approach to force safety improvement. The use of BBS is proactive because it gets shopfloor people working together to identify their hidden workplace hazards. It also gets unique data on your employees’ interaction with the hazards they have around them.
Workplace behavioural psychology is a scientific method to cause workplace safety change because behaviours are observed and measured (points of which make it a science) and specific solutions for risky safety behaviours are put into place and tested to prove the right behaviours are adopted.
What is a Behaviour Based Safety Program?
Behaviour based safety concerns itself with observing members of the workforce. Peers trained in behavioural based safety take five minutes out of their day to observe a colleague at work. The difference between Behavioural Based Safety Observation and a lot of other workplace safety inspections is that in BBS inspections the Observer introduces him or herself to the Observed and explains exactly what they are here to do, what the Observed can expect and what the Observer is trying to achieve.
The Observer looks to see if there are hazards present during a job and check what the Observed does about them. They want to note how does the Observed do the work when there is a hazard visible. Does the employee work around the hazard, or do they take time to remove the hazard?
The idea behind a behaviour based safety program is that many people can get desensitized to hazards in their work area and may not notice the risks they carry. Because dangers may have already been there for a long time those doing the work ‘see straight through them’ and are unaware of the potential harms that exist. The Observer is a ‘set of fresh eyes’ who does not know the job as well as the person being observed and will see risks that the worker will not.
The coping behaviours used by the Observed to deal with each hazard are identified and recorded by the Observer. At the end of the session the Observer feeds back what they saw, and risky practices that need to be replaced with better methods are identified for corrective action.
Conducting Behaviour Based Safety Program Observations
Behavioural safety psychologists have found that it is much better when peer observes peer rather than managers’ observing employees. When management watches employees it may be construed as a punitive process or micro-management, rather than a positive hazard identification and recognition process. Behavioural based safety observation has been found to work very well for the people on the shopfloor.
During observation the Observer follows a specialised format for recording. At the end of the review they discuss all the good things the worker did whilst being observed. Then a well-trained observer will discuss a hazard and why the worker continued to work around it rather than dealing with it. At the end of the feedback session the observer will finalise by ending in a positive note.
The Observer will then calculate the number of safe acts versus the numbers of unsafe acts the worker performed using the following calculation: Number safe acts / Number of safe acts plus number unsafe acts.
This calculation is very basic and enables the safety management to gauge not only the hazards being identified, but how the employee treats the hazard whilst being observed or not. It is a snapshot of what is going on and the number of safe acts versus the number of unsafe acts can be trended.
Chart Your Behaviour Based Safety Program Statistics
Visually present behavioural based safety program results in your workplace in a graphical format using a purpose-built spread sheet. It is also the most useful tool for boardroom reports as well as for senior management to measure what is happening on their shopfloor.
A behaviour based safety program is very good, however it must never be used as a performance appraisal tool or a disciplinary tool. As soon as you use it for disciplinary purposes your behavioural based safety programme will fail.
There is great benefit to you to get accurate, untainted data about your real workplace safety practices. It will influence other occupational safety and health initiatives, such as training, use of Safe Work Procedures, developing Safe Work Method Statements (to name just a few of the options you have to improve your safety practices). BBS program results can be employed to ‘close the gap’ when you find there are unsafe acts being done in your company.
Teach your people to fully understand your behaviour based safety program. Tell them of its benefits and its pitfalls so your BBS program is introduced correctly and works successfully. Collect data for each a month and graph it. Monitor the results and provide feedback. Be sure to properly interpret the BBS results to ensure you’re heading to where your workplace safety results should be. Go get sound and appropriate recommendations that it will benefit you and your work safety improvement initiatives when you are unsure.
Leave a Reply