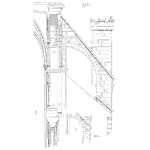
Bridging is the name given to the self- created arch that develops just above the outlet of a bulk material silo or hopper as it empties.
A bridge forms when wall friction holds up the ends of the arch.
To overcome bridging the wall friction must be reduced or prevented from occurring.
Keywords: live bottom, cohesive, powder, hopper design, angle of repose.
There are two types of arch. One is mechanically formed by relatively large particles (above 3 mm) interlocking, while the second is formed when powders bind together under compression (cohesive arch).
The resulting arch can support the weight of the material above it and prevent flow. Figure No. 1 shows the two types of arch.
Figure No. 1 Mechanical arch and cohesive arch
It is easy to tell if a silo has a material flow problem by looking for ‘hammer rash’ on the wall.
If the product is not moving freely through the silo and outlet the operator will strike the side walls to rattle the material free.
What causes bridging?
Bridging starts when friction stops the product at the wall and a neighboring particle wedges in behind or sticks to it.
The product binds to itself until an arch is formed.
Product from above compacts it into place and makes the arch so strong that it supports the overburden.
Sketch No. 2 shows a simplified view of the arch building process.
Whether bridging occurs depends on a number of factors.
a) The angle of the discharge section wall.
b) The material of which the silo or hopper walls are made.
c) The stickiness (cohesiveness) of the bulk material.
d) The amount of attraction between the particles of the bulk material.
e) The extent of settling (consolidation) within the bulk material.
f) The natural strength of the material forming the arch.
g) The amount of moisture in the bulk material.
h) The ease with which the bulk material slides over itself.
This list can be divided into two categories – effects that depend on the bulk material properties and effects that depend on the silo and hopper design.
Figure No. 2 The arch building process
Overcoming bridging in hoppers
Solutions to stop hopper bridging focus on reducing the stresses created in the bulk material at the bottom of the hopper.
If wall friction can be reduced or removed then the arch cannot get a foothold against the wall.
If the cohesiveness if the bulk material can be reduced then the arch cannot span the gap before it collapses under the weight of the overburden.
If the weight from the overburden can be directed away from the arch it will prevent compaction.
Design to the product
The best approach to prevent bridging is to correctly design the hopper and silo for the product being handled.
Standard tests can be done on samples of the bulk material to determine the necessary hopper angle and opening size for the product or range of products put through the silo.
The Centre for Bulk Solids and Particulate Technologies at the University of Newcastle, NSW do bulk materials testing.
These tests cost AUD$3,000 per product but they pay for themselves with a proper silo design producing free flowing product.
Discharge hole
One method to prevent an arch developing is to make the discharge hole from the hopper so large that the arch will collapse into the opening because the side wall is not present to provide support.
In existing silos, the size of this hole can be determined by viewing the position on the hopper wall at which the arch is supported and adding an additional 20% to the measurement.
A ‘live bottom’ would also be required to feed the material out of the discharge opening.
Rectangular opening
Another method is to convert the hopper into one with a long rectangular opening of length equal to the width of the silo.
This removes the wall on one side of the hopper and allows the material to collapse into the long discharge slot.
The width of the slot need only be half the size of the equivalent round opening to discharge the hopper.
A feeder the full length of the slot would be required to remove the product.
Steeper hopper angle
Improvements to the flow can also be gained by having a steeper hopper angle combined with resizing the outlet.
The steeper walls reduce the friction and the outlet is again sized larger than the point at which an arch forms.
Go mechanical!
Mechanical methods are also available to overcome bridging.
Stirrers, internal screw feeders, flexing air pads mounted inside the hopper and air- blasting devices can be used. These operate by fluidizing (aerating) the bulk material and reducing the cohesive forces in the product.
Vibrating shakers mounted to the wall of the cone only help compact the contents.
Live bottom bin activator
A recent invention is the live bottom bin activator for cone shaped hoppers.
It promotes flow by installing a steep upward pointing funnel cone inside the hopper portion of the silo where the arch would form in order to prevent compressive stresses developing throughout the product.
The material is feed between the gap separating the skirt of the internal cone and the wall of the hopper by vibrating the separately suspended bottom cone.
This design overcomes the effects of both the wall and the internal bulk material stresses.
Mike Sondalini – Maintenance Engineer
If you found this interesting, you may like the ebook Bulk Materials Handling Introduction.
I definitely think that it is best to design a hopper is such a way to reduce bridging. However, if you already have a hopper it is probably not the most cost effective method. In this case, I think that flow aids, like flexing air pads, are the best option.
Hi there, I have been having problems with silo bridging for the last 6 years at our mill. I have soya hi pro stored in 3 square concrete silos and 1 metal silo. Keeping track of stock and conducting stock take is a nightmare because I cannot seem to get the correct dips due to the bridging. Any suggestions is most welcome. Thanks Dasen Antony
Hi Dasen, thanks for the comment and solution request. Let’s see if any readers have a suggestion for you. Another place you may post the question is in the Linkedin group Reliability Success (plenty of plant based folks there) cheers, Fred
Hi Dasen, a college of mine has just brought this thread to my attention and I was wondering if you are still looking for assistance with your bridging problem? I work for a company called Primasonics International Ltd who specialise in the design and manufacturing of Acoustic Cleaners, for use in the dry bulk material storage and transportation industries, and I believe we could certainly help with your bridging issue. Our cleaners use standard plant compressed air to create rapid pressure fluctuations that would be transmitted into the bonded dry material inside your silo, causing the solid particles to resonate and dislodge from any surface they are deposited on or bonded to, without causing any damage to the silo itself. If this sounds like something you might be interested in and would like more information, please do feel free to drop me an email back or visit our website. The following link has a useful demonstration video and a few relevant case studies, along with a downloadable questionnaire you can complete and return to us if you would like our engineers to offer their recommendations and a no-obligation quote for a suitable solution – http://www.primasonics.com/silos-hoppers. Best regards, Dan.
I think it is useful that you mentioned how the buildup of material can effect bridging. This is when having something to clean it out can be useful. An air cannon might be a great option to look into if you are experiencing issues.
We are a cement factory. In our raw meal mill, we have some blockage of material from hopper and we need solutions for this.
I work at a refinery plant and am having problems of coal bridging at the smelting plant, the coal hopper bridging is too much we have employed the mechanical methods of air etc. Our fuel coal injection system is facing flow interruptions please help.
Hi there,
We have 2 x 40Tons capacity Silos in our factory for our food manufacturing process. One of the Silo has Ultra white flour and the other Protein Enrich Flour. The silos are square in shape similar to some bulk bag and of a woven material, the bottom of the silo is funnel shaped and in stainless steel with a round discharge of 200mm diameter, it is attached to a 300mm square flange where the rotary valve is fitted, there was no provision made to fit a sliding gate valve between rotary valve and the 200mm diameter discharge of the silo for maintenance or breakdown should the rotary valve needs pulling out for dismantling. Maintenance was lucky that when they decided to remove the rotary valve, the bottom of the silo was bridging, at the time there was 26 Tons of flour in the Silo. Our issue is, that every time we have an annual cleaning of the silo for fumigation, we always have a bridging issue on the silo, is it because of the chemical residual after the fumigation, couple with bad design on the discharge. The bottom stainless steel hopper has a series of air fluidisers fitted onto it that activates on cycle during transfer. Can someone help recommend to overcome the issues we are having.
Kind regards,
Charlie Putong