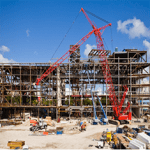
Welcome to part five of my 10-part series of blogs called “Uptime Insights”, where we explore a journey of excellence in maintenance. To stay on top, managers must implement strategies that keep operations performing at high levels. In these articles I will show you how to achieve excellence in maintenance – a critical business process in any capital intensive industry.
Uptime Insights Part Five:
Without parts many jobs can’t be done. There’s no point planning and scheduling work if you can’t rely on materials management to provide the parts when you need them. If you want excellence in maintenance you need excellence in materials management.
Top performers don’t delay or halt work because of a lack of parts. When it happens it’s largely a failure of the planning and work management processes but it can also reflect on materials management. Maintenance, repair and overhaul (MRO) materials usually make up a small portion of most companies’ material inventories but the bulk of the inventory transactions. These parts and materials usually represent a small portion of your inventory investment but they can be critical to whether or not you are able to run your plant. Individual parts can be of any value, they are purchased and used in small quantities, they are often slow moving but hard to source, they are essential to getting planned work done as planned and on schedule, and there are a lot of them. Managing MRO materials is a big and very important job. If it is done poorly, the value of improving maintenance performance will be seriously limited.
Integrating materials management processes such as stores issues and returns, receiving notifications and purchasing with the maintenance planning and scheduling parts of the work management process is critical to success. There’s no point ordering materials for a rush job if the parts arrive only to sit on a shelf because maintenance doesn’t know they are there. Worse still, if the job is urgent and maintenance works outside the normal procurement processes and double-orders to meet production demands.
Information sharing and data management is important to having the right numbers of the right parts on hand, to ordering in economic quantities and to providing a high level of service to meet demand for needed maintenance parts. The internet has become a valuable tool in enabling e-business transactions that speed information flow and purchasing transactions minimizing the wait for some parts.
Of course, the maintenance parts store room is the focal point for your maintainers. There’s much that can be done to make it efficient and cost effective. The key to success here is to have maintenance, inventory and supply chain management working together.
In our next blog we’ll explore part six of our 10 part series “Uptime Insights: Achieving Cost Effectiveness with Performance Management”
To learn more visit Conscious Asset where you will find training, workshops, books, and resources.
Related
Uptime: Strategies for Excellence in Maintenance Management (book)
Leave a Reply