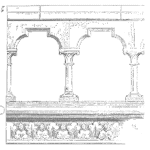
Part 5 of 5
A Question & Answer Period with Fred Schenkelberg on the what can be done to improve the reliability of your operation.
So far in this series, we have had the opportunity to discuss the role of reliability engineering in today’s maintenance environments. In this final post of the series, I (James) had the opportunity to ask Fred Schenkelberg some questions related to this very topic. Fred, with his years of experience, was able to provide some great insights to the role of reliability engineering, and what those in the maintenance department can do to improve reliability.
Even if you don’t have a reliability engineer in your organization, you can implement a few basic reliability engineering techniques to make a sustainable difference in your operation. See the ebook with all five articles in this series below.
Learning from A Reliability Expert
Why is it manufacturers choose to not invest in the design upfront?
Mostly out of ignorance. There are many rationales and competing priorities for any product or piece of equipment under development. It’s when the value of reliability performance to the customer and to the designing organization is clear will the team design for reliability properly.
Another reason I’ve heard, is the design team does not know enough about the customer, their priorities, the cost of failure, and operating conditions. Without this essential information it is difficult to estimate reliability performance nor the impact (cost of failure).
If we could only do one thing in the design stage of equipment, what would it be?
Ask the questions, often, is it good enough? (reliability speaking of course)
Reliability is often considered difficult to measure, thus goals and requirements become of little use as there is little by way of measurement. By asking is the design good enough, you can only answer their question by understanding the reliability risks, the current estimates, and the weaknesses of the design. Then the team can make informed decisions concerning the reliability performance of a system.
What is the one thing that can be done to improve maintainability?
Make the cost of unplanned downtime well known.
This provides a basis to plan for and conduct preventative maintenance, plus to invest in predictive maintenance technologies. If the only approach is fix on failure, the team is missing the chance to reduce overall costs by investing appropriately in preventative and predictive maintenance.
In maintenance, should RCM or FMECA be used?
Yes, always. Reliability Centered Maintenance is set of approaches, yet basically focuses on preventing the consequences of failures whenever possible. Always a good move.
FMECA is a risk prioritization tool. It helps the maintenance team a couple of ways. First by providing the team insight on what could go wrong and which areas of the equipment provide the highest risk (not just frequency). Second by helping the team identify means to minimize or mitigate failures and thus downtime.
Should someone in Maintenance look to certification as a reliability engineer?
A little knowledge is a good thing for the maintenance team members. A certification provides a structure and check on a body of knowledge. It often broadens the knowledge of anyone pursuing the certificate.
Plus, even if one doesn’t sit for the exam, the exercise and practice of the various concepts and tools associated with a certification will help the person be efficient and effective at work. Mastering the knowledge associated with maintenance engineering is good for the person and program.
Why is plotting your data important?
We all have too much data from our equipment or products concerning reliability. Averages and summaries play a role in understanding the data, yet often conceal the essential information you need to interpret your data correctly.
Plot the data. For repairable systems use a mean cumulative function plot, or with non-repairable elements of your system use a Weibull plot to get started. Time to failure information is rarely constant. The failure rate will vary with time. Identifying increasing or decreasing failure rate trends is essential to properly care of your equipment and improve your program.
How should your set reliability requirements for your purchased equipment?
Hopefully not with a single number. Reliability has four essential elements that incorporate a complete reliability requirement.
Include the function(s), environment (weather and use conditions), duration and probability of successful operation. Even better is to include multiple durations or periods of time. For example, set a probability and duration couplet for the first month of use, the first year, and then 10 years.
Being complete and clear with the specifications enhances the chance you will receive equipment that meets your needs.
When your equipment fails, what should you avoid doing?
Blaming someone. By know this should be common knowledge, yet it all too common. When the equipment fails, it is not the operator or technician’s fault. It’s the design, the maintenance process, the priorities to run at all costs, etc. It’s really a management role to set the tone of the organization to focus on learning from each failure and working to improve the system and processes to avoid failures in the future.
When your equipment fails, what should you do?
Pull out your crime scene investigator tool kit and learn as much as you can. Rather than rush to patch or replace equipment to quickly get the line up and running. Take a few minutes to learn what caused the failure. The failed item may be a victim of another element of the system malfunctioning. The failed item may be the hero, averting a larger failure within the system that a simple patch will permit to occur. The failed item may well be the causes, well, why?
Sure there is a balance with getting the system running again, yet if you do not learn what to actually improve within the system you’ll be back doing the same repair again and again. Even taking 5 minutes to gather data and make observations will serve the team to analyze what happened. It is often critical information needed to implement significant improvements.
Do your equipment operators and maintenance personal need to feel ownership for the equipment they operator or maintain?
Yes. And some will despite what management does. Some will take personal pride in operating and maintaining their equipment to the best of their ability.
Others will not. They will avoid reporting issues, they will miss signs of impending failure, they will defer repairs to the next shift. After all, they have production to get out.
Creating a culture of ownership will encourage more ownership behavior. Not everyone will participate, yet the policies and practices within your organization can help most take ownership of their equipment. The benefits include smoother running equipment, less downtime, and higher employee morale.
The Next Steps
What is the one thing you took away from the not only this post, but the series? What is the one thing you are going to do differently to improve the reliability in your organization?
I want to thank Fred, for sharing his wisdom and experience. If you have any questions of your own, please email questions@HPReliability.com and we will do our best to answer them.
Fred Schenkelberg
Part 5 of 5 in the Maintenance & Reliability Series
Fred Schenkelberg is an experienced reliability engineering and management consultant with his firm FMS Reliability. His passion is working with teams to create cost-effective reliability programs that solve problems, create durable and reliable products, increase customer satisfaction, and reduce warranty costs. If you enjoyed this article, consider subscribing to the ongoing series at Accendo Reliability.
All five articles in this series in one short ebook, interested?
Please login with your site registration to download this ebook which includes all five articles in this series.
Login
If you haven’t registered, it’s free and takes only a moment.
—
The other articles in the series include:
Post 1 – Incorporating Reliability into Your Future
Post 2 – Using a Design FMEA
Post 3 – Where Does Maintenance Fit Into Reliability?
Post 4 – Life Cycle Costs
Post 5 – What Can You Do To Improve Reliability? A Q&A with Fred
Great series Fred. I really enjoy your articles .
Thanks Jon, certainly do appreciate the support and kind words. cheers, Fred