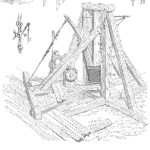
When spares cannot be purchased easily it becomes necessary to manufacture your own.
Local fabricators, foundries and machine shops can often make the item if you provide them with a design and specification.
Keywords: casting, reverse engineering, metallurgy, original equipment manufacturer, second hand.
When you need a spare part for equipment made overseas be prepared to pay up to three times what it is worth.
Wasting that sort of money puts ‘a chill’ up the spine of a maintenance manager. The logical thing is to ask if the part can be made cheaper locally. In a lot of cases, it can be with both a better price and faster delivery.
Reverse engineering, as this process is often called, can offer an opportunity to lower maintenance costs and improve equipment operation.
The cost of spare parts
The cost of a part brought from overseas or interstate will include shipping and freight charges, possibly customs duties and taxes, profits for various middlemen and one-off production costs for the manufacturer if the spare is made from design drawings.
The supplier also knows that you are in no position to bargain. And people being people, he will add on a premium because he knows you have no choice but to pay up.
Fortunately, the high price affords you an opportunity to absorb the development cost of a replacement part within the cost you would have to pay to the original equipment manufacturer (OEM).
Difficulties also arise if the equipment is an old model and it is out of production or if the machine was a one-off special design.
OEMs will not supply spares for their machines indefinitely.
Some manufacturers will have spares available for up to 25 years while others will only carry spares for 10 years.
Obviously, it is in their interest to get you to buy new machines instead of keeping the older models in use.
Replacement decisions
The decision to replace a machine is an investment decision.
You need to determine if the cost of replacement will lower operating costs for a sufficiently long period of time to recoup the money required for maintaining the existing machine over the same period of time.
This explains why machines are kept in service for decades and why there is a second-hand equipment market. It is very difficult to justify replacement purely on maintenance costs.
Once your money is spent on equipment – you’re stuck with it.
The best option, if the machine is a ‘dog’, is to design out the problems yourself.
What parts can be made locally?
The sorts of parts that can be made locally depend on the technical skills available in the local industry.
Are there foundries that can cast various materials?
Are there fabrication shops with the equipment to make the part? Do the machine shops have the machinery of the right size and type?
Will the skills and abilities of the local tradesmen produce quality work?
Do they have systems in place that control the quality of their production?
Shafts are probably the easiest item to get made locally, as a sample is usually easy to provide. If you don’t have copies of the manufacturer’s fabrication drawings the dimensions can be measured from the original.
Tolerances for bearings, seals, sliding surfaces and interference fits must be determined for the fabricator and machine shop.
Small cast parts are also often easy to get locally made.
Examples are pump impellers, mill hammers, liners, open gears, rollers, etc. A sample can be provided to the foundry to determine material composition and method of construction.
What to do to make parts locally
Often the material from which a part is made is unknown.
In such situations, you need to contact a materials specialist to conduct tests on its composition.
For example, a metallurgist can do a spectrograph test on a piece of metal and tell from the percentages of the constituent elements the metal and its grade.
With this information, you can contact the local foundries and fabricators to find out if they are able to supply and work with the material.
Redesign the part if necessary
At other times you may need to redesign the part.
Often a part performs a function that can be satisfied in other ways to the method used by the OEM.
To permit local workshops to use their existing equipment and methods you may need to make a small adjustment to the design. You still end up with the function required but the item can now be made locally.
Can the part be made from alternate materials and by different methods?
Perhaps machined or fabricated instead of cast in one large piece.
Usually, ingenuity and creativity find a way.
Be prepared to work with the local shops to get what you want.
You may need to experiment with designs, methods, and materials. The aim is to get your parts at a better price or delivery than buying them from the OEMs.
Provided it is cost effective, there is value in working through the problems that normally arise in doing something differently.
Can you on-sell your part?
Once you have manufactured the parts and developed the drawings and material specifications you are in the position to become independent of the OEM.
If the OEM no longer carries the parts or is not prepared to make the parts, you may be able to make and sell them to other remaining users of the machine.
Be careful you do not infringe copyright or patents and other similar proprietary ownership issue.
Challenges for designers and purchasers
If you are a designer of machinery or the person responsible for procuring equipment in your company, you are in a unique position to affect the long-term maintenance costs of the equipment users.
Your choices will continue to affect people for possibly the next 30 years and in some cases up to 60 years after you make them.
This means you must endeavor to keep your designs or equipment selections as simple as possible.
Use the most common materials and construction techniques available that will satisfy the duty.
Much equipment is sold second-hand.
Users of older equipment usually have to operate them without support from the OEM.
If you have designed or selected easily maintainable equipment made of commonly available parts and materials then you have made good decisions that will benefit people for decades to come.
Mike Sondalini – Maintenance Engineer.
If you found this interesting, you may like the ebook Bulk Materials Handling Introduction.
Leave a Reply