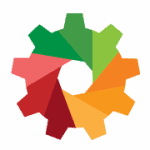
Mature organizations seeking a competitive edge are familiar with the term Reliability Centered Maintenance (RCM). A maintenance philosophy encompassing predictive, preventative, and maintenance, RCM uses defined processes to find latent or hidden failure modes, customizing maintenance processes to maximize system performance. Most understand that the RCM philosophy enhances equipment availability through improved reliability, increasing annual earnings before interest, tax, and amortization (EBITDA). Yet, some businesses fail to understand that equipment availability comprises two crucial inputs, not one. Equipment reliability, yes, but also equipment maintainability.
Combined with availability and reliability, maintainability is the third leg of RCM, less glamorous, often ignored, but without which a company’s RCM investment will fail to deliver optimal results. No matter the efficacy of an asset maintenance program, maintenance downtime is inevitable, and maintainability refers to the speed with which equipment returns to productive service. While often thought the sole preserve of designers, in-service activities provide multiple operational, tactical, and strategic levers to improved equipment availability through enhanced maintainability.
Benefits Of A CMMS
Leveraging a maintenance program to enhance maintainability depends on a reliable, comprehensive, and networked computerized maintenance management system (CMMS). A CMMS collects historical operating and maintenance information while scheduling pre planned maintenance or inspection tasks based on equipment hours, cycles, or calendar time. Yet, it can also be linked to inventory, quality, safety, and engineering systems; and in those linkages lie the true power of improved equipment maintainability.
Correctly utilized, CMMS improves maintainability at three different levels within an organization. Operationally, its focus is on assisting the maintainers to be as safe, efficient, and productive as possible. Tactically, it prepares production, organizational processes, and assets in advance for the pending maintenance downtime. Strategically, it fine-tunes and informs the corporate-level strategy to optimize maintenance strategies; implementing and ensuring minimum safe levels of equipment care through effective governance.
The operational opportunities for improved maintainability focus on enabling the maintenance technician to maintain, not seek, queue, research, or wait. Examples include access to maintenance procedures, repair techniques, illustrated parts catalogs, and wiring schematics. Linked to the CMMS, electronic tablets allow access to safe work practices (SWP), personal protective equipment (PPE) requirements, fault troubleshooting, and repair procedures, assisting technicians to remain at the worksite and improve their productivity. Helpful in reducing the potential for personnel injury and downtime from incidents, scannable QR codes at pinch points can allow rapid access to and reinforce lockout/tag out and safe-work procedures.
Tactical benefits accrue from minimizing maintenance downtime by provisioning all resources necessary for the planned tasks ahead of time. Such provisioning through the CMMS identifies and orders spares, ensures critical tooling serviceability, availability, and calibration, it can schedule technicians by skill and currency, and task stores personnel to prepare and stage all spares, tooling, and consumables necessary to acquit planned tasks.
Such pre-planning minimizes unpleasant surprises on maintenance day, when delays from finding people, tools, or spares decrease maintainability, increase frustration, delay maintenance shutdowns, impact production, and reduce equipment availability. Further tactical gains occur from measuring the operational intensity of production equipment, using algorithms in the CMMS to adjust inventory levels, reschedule repair turn-times and refine restocking triggers to meet desired equipment availability rates.
The strategic maintainability gains from a CMMS lie in the power of data collection and analysis. On-condition and condition-monitored maintenance, defect analysis, and updated mean time between failure (MTBF) rates optimize maintenance programs, calculating appropriate inventory levels and targeting necessary technician interventions. Engineering analysis from linked maintenance data allows ongoing cost-benefit analyses, informing such decisions as to whether modular replacement versus part replacement is the most cost and time-effective repair strategy.
With enhanced governance from analyzing maintenance task times and spares traceability, training needs and purchasing optimizations are better informed, with more focused budget spend decisions.
In Summary
The gains to maintainability from a practical and well-managed CMMS are akin to compound interest in a savings account. Each on its own may be small within the context of single maintenance shuts. Yet, combined and refined, the process becomes iterative, and the gains rapidly accrue. In asset-intensive industries such as the airline industry, it’s not unusual for maintenance costs to comprise 13% of total operating costs (TOC). For businesses seeking a competitive edge, the combined focus on reliability and maintainability via a CMMS may provide the opportunity to pare that figure back by a few points, flowing through to enhanced annual EBITDA results.
Leave a Reply