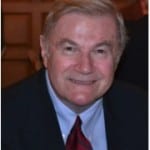
Guest Post by John Ayers (first posted on CERM ® RISK INSIGHTS – reposted here with permission)
There are many design rules of thumb I have heard over the years. For example: KISS (keep it simple stupid); make it idiot proof; be realistic with tolerances; do not make assumptions that are not realizable (zero gap for instance); and many more. The most important rule of thumb I have experienced is “common sense”. To illustrate my point, I have a few examples that are below.
Example 1-The Eyeball
I was working on a program for large phased array radar. A major component of the radar was the support structure that a very large, spherical geometry (approximately 100 feet in diameter). For radar, the stiffness of the structure drives the design to meet the RF beam pointing accuracy requirements. The lead engineer for the support structure (and his team) developed a very stiff, unistructure (dubbed the “eyeball”). It was a specification compliant design that successfully completed a preliminary and final design review. The structure documentation package along with and RFP (request for quote) was sent to 5 different well known and qualified bidders. Only one bidder provided a proposal which included the development of a new multi-million dollar tool to machine the “eyeball” to drawing requirements. Aside from the very expensive tool, the structure could only be shipped by barge which was very expensive and required a shipyard to build it because of the need for access to the waterway. Panic set in once it became obvious the design was too expensive to build. This revelation resulted in a significant schedule delay while the structure was re-designed into a knock-down design that could be fabricated and shipped using standard existing tools and equipment. The surprising thing to me was how the design got through the design reviews without picking up this major problem. I believe part of the reason was the lead engineer (aka the “wizard” as he was known) was so well respected and trusted that very little or no oversight was given to the design. In hindsight, it may have been a wonderful technical design but no one used any common sense in the design development and reviews resulting in substantial schedule and cost growth to the program.
Example 2-The Low Cost Antenna
I was involved in an IRAD (Independent Research and Development) project for a new, portable, low cost antenna in preparation for a pending government RFP for this product development. The best design engineer in my department was assigned to the project as the mechanical lead. The antenna design went well including design reviews. The project met cost and schedule goals. It was considered a success. The surprising thing to me was the antenna structure material was specified as spent plutonium, a very unusual, expensive and hard to get material. The lead engineer disclosed that he selected that material because the density was the best one to use for dynamic balance since the antenna rotated at high speeds. A great theoretical technical approach but no “common sense” for a low cost antenna. A redesign would be necessary once the RFP came out to submit a completive low cost antenna development proposal.
Example 3-Rapid Deployable Portable Satellite Communications Antenna
The government came out with an RFP for a rapid deployable satellite communications antenna for soldiers in the field to use under combat situations to communicate with elements of their unit and other units. It was a potentially lucrative program with a development phase and options for large quantities of production units. The RFP included the prototype design developed by one of the national laboratories. This was a standard practice by the government whereby they funded one of the national laboratories to design and build a prototype and then subcontract it to industry for the detail design, fabrication, tests, documentation package and transition to production. Historically, the laboratory design worked technically but required significant effort to develop the design to be producible, reliable and cost effective. As a result, the final product designed by industry was usually much different that that done by the laboratory.
The proposal manager had the responsibility to select the winning design concept and proposal approach. He decided that the winning strategy was to maintain the laboratory design concept (with a few tweaks) which comprised about 20 lose parts making it extremely impractical to assemble the antenna quickly in the field especially at night. In spite of efforts by the proposal team to change his mind this approach was submitted in the proposal to the government. Evidently, management was sold on the idea the laboratory had significant input into the selecting the winning proposal and by using their design would provide us with an advantage. We lost the competition to another company that proposed a design with no loose parts and a simple method to deploy the antenna with one easy stroke. Our design was judged to be the worst because it was not practical. Common sense did not prevail and we lost badly.
SUMMARY
Engineering has been called a science and an art. I think it is both. Requirements, policy and standards, rules of thumb and guide lines are vital to developing good designs that are producible and cost effective. But in my view at some point early on the the design cycle, a sanctity check called “common sense” needs to be applied to ensure success.
Bio:
John earned a BS in Mechanical Engineering and MS in Engineering Management from Northeastern University. He has a total of 44 years’ experience, 30 years with DOD Companies. He is a member of PMI (project Management Institute). John has managed numerous firm fixed price and cost plus large high technical development programs worth in excessive of $100M. He has extensive subcontract management experience domestically and foreign. John has held a number of positions over his career including: Director of Programs; Director of Operations; Program Manager; Project Engineer; Engineering Manager; and Design Engineer.His technical design areas of experience include: radar; mobile tactical communication systems; cryogenics; electronic packaging; material handling; antennas; x-ray technology; underwater vehicles; welding; structural analysis; and thermal analysis. He has experience in the following areas: design; manufacturing; test; integration; selloff; subcontract management; contracts; risk and opportunity management; and quality control. John is a certified six sigma specialist, certified level 2 EVM (earned value management) specialist; certified CAM (cost control manager).
Leave a Reply