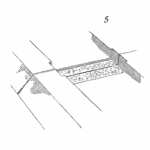
Critical is defined as “a situation or problem having the potential to become disastrous”. A system of physical well barriers is used in offshore wells to mitigate against a disastrous event. The United States Bureau of Safety and Environmental Enforcement (BSEE) refers to Category 1 and 2 well barriers. A failure of a barrier can lead to a blowout or fluids spill into the ocean, either of which is high severity. Thus, it is customary in the upstream energy industry to refer to well barriers as “critical equipment”.
TRUTH: Well barriers protect against disastrous events.
Should non-barrier equipment may be considered critical? For example, is it critical that intelligent completion systems operate with precision over a long service life? Is the severity of failure high if a remote-controlled downhole valve cannot shut-off water inflow? Is the severity of failure high when a chemical injection valve fails three years into well life? Reliable water shut-off and corrosion inhibition may vastly improve project economics. Is it business-critical that this equipment perform reliably?
TRUTH: Non-barrier products may be critical for project success.
As was stated in Quality and Reliability in Oilfield Equipment, completion equipment is highly customized and has a long expected service life. Long-term reliability in offshore applications is required for favorable project economics, to avoid high intervention costs, and because equipment failure can result in an HSE incident. As a result, offshore completion equipment must be developed using thorough due diligence and best practices. This includes industry product and materials standards, extensive simulation and modeling, robust laboratory testing programs, a DfR program, risk discovery (FMEA), systematic failure analysis (RCFA), thorough design policies, and manufacturing to the highest quality levels.
The articles in the Critical Equipment series cover the design of critical equipment for offshore completions. They will also challenge some legacy equipment development practices, reliability assumptions, operator practices, and identify areas for improvement.
This is the 1st in a series of 10 articles on critical equipment design for offshore completions.
- Critical Equipment Fundamentals
- Technology Readiness Level (TRL)
- Materials and Design Risk
- Temperature Deration
- Design for Reliability (DfR)
- Factors of Safety and Load Factors
- Using Industry Standards in Design
- Modelling and Simulation
- FMEA Improves the Bottom Line
- Lab Testing Programs
Leave a Reply