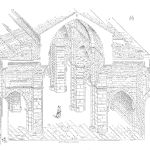
One of the considerations when planning maintenance is the timing of the replacement of parts of the system. In some cases it makes sense to wait for the item to fail, sometimes, it makes sense to place it on an interval or set an amount of operating time, and yet in others, we can measure indicators that a replacement is necessary.
In order to make these decisions, we need data.
According to O’Connor and Kleyner (Practical Reliability Engineering, 5th Ed.), we need specific information for each part. The following list outlines the recommended information.
1. The time-to-failure distribution parameters for the main failure modes.
This involves keeping track of when an item is placed into service when it fails, and the nature of the failure. Additionally if possible track down and record the root cause of the failure. A focus on failure mechanisms also is useful as the item failing may not be the only place to implement an improvement or repair. The failed item may be the hero that received the damage when some other element’s failure (misbehavior) instigated the fault.
This information provides you the ability to schedule, if it makes sense, part replacement before failure occurs.
2. The effects of all failure modes.
Not all failures are the same. Some cause serious safety risks, some are barely noticeable or easily ignored. This information provides a means to prioritize inspections or replacements.
The information allows us to focus on minimizing the serious effects of failure.
3. The cost of failure.
Like effects, not all failures incur the same costs. You can use this information to prioritize replacement strategies to minimize both the cost of the parts & maintenance activity and the cost of the resulting failures.
4. The cost of scheduled replacement.
The costs include labor, parts, and associated element so doing the replacement, it also includes the cost of downtime – did you really need to shut down the line for the repair based on the schedule. It had better be worth it to avoid more costly downtime later due to failure.
5. The likely effect of maintenance on reliability.
Some maintenance restores the equipment to like-new conditions, some just keep the equipment running. Track the impact of maintenance on the subsequent failure rates to determine what is useful or not so useful
If we are able to measure indicators or an element of a replaceable item (vehicle tire tread depth, for example) we can anticipate failures shortly before they occur.
To do so, we need two more bits of information.
6. The rate at which defects propagate to cause failure.
Do we have time before the unit is likely to fail or require replacement? Can we get more value out of the existing equipment before doing repairs? We can answer these questions is tracking the rate of degradation.
7. The cost of inspection or test.
Even just looking costs money. It takes time. Sometimes the inspection is very expensive and should be considered when balancing the benefit of the measure with the ability to avoid even more costly failures.
The information provides a means to make decisions to optimize your preventative reliability program.
Related:
Field Industry and Public Failure Data (article)
Program Elements Part 1 (article)
8 Factors of Design for Maintainability (article)
Leave a Reply