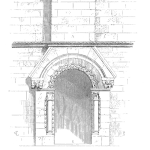
Uncertainty is another word for risk. Reliability uncertainty or risk is neither good nor bad, it just a bit unknown. Until we know the outcome, the eventual reliability performance, we will not know the impact.
So, how do we deal with reliability uncertainty? Will our product or system work as expected over time, or will it fail? Let’s examine a few of the common approaches in use and when and why the approach is effective.
Understand the risks
As with any engineering challenge, we first need to recognize the problem is a challenge. We need to be aware of what we know and what we do not know. What aspects of our chosen material, fastener, component, etc. are going to behave in unexpected ways for our particular design and set of loads?
For example, we may have a new resistor component. It has a novel material not commonly used as the active element of a resistor. It is inexpensive, small, and has very little variability from one resistor to another when manufactured. What else should we know about this new component?
A quick brainstorm may reveal a set of questions worth exploring before adopting the new component. How will the device respond to the range of currents, voltages, etc within the circuit? How will it respond to voltage spikes, EMI, or other power line disturbances? How will the resistance and other important characteristics change over time due to heat, oxygen, ozone, dust, vibration, etc? With a little effort, you may quickly expand such a list. This is the list of uncertainties.
Now, the organization that developed the new resistor may have already addressed many if not all of these questions. Yet, did they do to a degree that encompasses your particular application?
The other aspect to explore is the impact or consequence of not fully understanding the reliability performance of the new component technology. What is this new resistor that continues to perform as if new? That is probably a very good result. What is the resistor changes its resistance value by an order of magnitude? Becomes open or short? What if… fill in the blank.
The paths to the most severe consequences then prioritize those uncertainty to explore and understand.
Increase the margins
In some cases, we do not have time to fully understand all the risks. Yet, we do have enough information to know a possible solution.
For example, if creating a mechanical support for a shelf, we may not fully understand the range of loads, vibrations, or shocks the shelf may impart on the support structure. Yet, we have a rough estimate. So, double the estimated load and design a support system to accommodate twice the load that is expected.
By increasing the margin, the difference between expected strength and stress, we account for our uncertainty concerning the actual range and type of loads, plus any uncertainty concerning the variability of strength of the manufactured support structure.
More uncertainty, within reason, then use more margin. High adverse consequence if a failure occurs, again use more margin.
Use known materials and vendors
A common method to avoid uncertainty is to only design and build with well-understood materials and components. Use only materials and processes from trusted sources. Use only well-characterized and proven design and manufacturing methods.
Avoid anything that deviates from what has a proven track record.
Your organization may use this approach via an approved supplier list, or a preferred component listing. It may be encouraged via internal design guidelines and challenges to any use of something new or novel.
This approach may work to minimize the risks involved with something new, yet it also limits what is possible to create that solves new problems.
One benefit of such a system is to limit the elements that then require further characterization and understanding before adopting.
Take the time to characterize
An uncommon approach, unfortunately – speaking as someone that is curious how something works and fails over time – is to invest in a thorough investigation to fully understand how a material, component, design, or process will perform overtime under a wide range of applied stresses.
I once worked in an organization that had a group of engineers and scientists that did the characterization work to both identify potential risks and to conduct experiments to minimize uncertainties concerning performance over time.
The team would work with product development teams to identify the future needs for material or component improvements or changes. To identify the new and unknown elements that needed better characterization to reduce the uncertainty concerning its use.
As you can imagine this was expensive, time-consuming, oh, and rather fun and actually did avoid some major field failures.
Which Approach to Take
A mistake to avoid is the simple assumption that this new widget is going to work just fine in our application. While we would like the new widget to perform well, as we optimistically look forward to solving our customers’ problems. The critical view, of what do we know and don’t know about the future performance is worth considering?
In order to make rational decisions, we need to understand the risks. Reliability uncertainty is often complex, yet the consequences can be serious. Sorting out those risks and taking steps to reduce the uncertainty using one or more of the above approaches is a prudent approach.
Leave a Reply