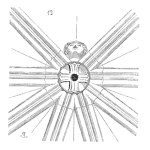
A better approach using RAM models
Traditional spare parts or inventory calculation methods involving Min-Max levels lack rigor, especially for critical equipment. Reliability, Availability and Maintainability (RAM) models provide a better approach to this calculation.
The importance of spares inventory management
“Don’t get caught with your pumps down”!
Having the correct number of spare parts in inventory is key to addressing recurring equipment failures. Organizations don’t want to have failures only to find out that they have no spares parts in stock. Downtime incurred waiting for spares causes revenue loss. Additionally, “rushing” in emergency spares is expensive mainly due to transportation costs. On the flip side, having unused spares in inventory is also undesirable. Most spares are consumable goods and have a specific shelf life. They deteriorate over time and are discarded if past their best buy date. Large amounts of spares discarded over time can add up to a significant financial loss. In addition, keeping spares in stock comes at a cost. Also known as “holding” costs involving insurance and storage expenses. It might not be intuitive but inventory is expensive to maintain.
The concept of Mix-Max levels
Inventory Min-Max levels, also known as Min-Max ordering policy, is a common inventory management strategy. It defines the minimum and maximum quantities of a product that a business should keep in stock. Formulas below are used for this purpose.
- Minimum Stock Quantity (Min) = (usage per year / 365) x lead time.
- Maximum Stock Quantity (Max) = Minimum quantity + Economic Order Quantity (EOQ).
- Economic Order Quantity = √(2DS/H).
With:
- D = Usage per year.
- S = Ordering cost per order.
- H = Inventory carrying cost.
This method can apply to non-critical spares. Thus, avoiding complex calculations or software programming. However, when it comes to critical equipment, the method is somewhat deficient and could lead to the wrong decision regarding inventory.
The RAM model approach
Spare parts consumption is directly related to equipment failures. And those failures are governed by life statistics. The equations above are linear and do not include the concept of randomness which is a characteristic of equipment failures.
Therefore, if we are looking at stocking critical spares for equipment, we first need to define the life characteristic of the equipment. This is based on its failure records. Equipment come in multiple units, in different types, fail in different “modes” and have different spare parts. This leads to very complex systems hence why a RAM model is a tool of choice to quantify the sparing requirements.
However, a RAM model moves us away from the term “Min-Max” and instead calculates the most economical number of spares to maintain in stores. This involves minimizing financial risk over time.
Calculation inputs and outputs
The main inputs to the calculation are as follows:
- Life distribution for the component being stocked.
- Financial impact of an unplanned component failure.
- Cost of a planned component replacement.
- Number of equipment this component is assigned to. The component ends up in a “pool” of spares. For example, a specify bearing type assigned to 10 identical pumps.
- Regular purchase cost of the component.
- Time the component takes to get from the supplier to storage.
- Purchase cost if you run out (emergency spare cost) and the time it takes to be “rushed in”.
- Time the component takes to get from storage to the field when a repair is required.
- Inventory or holding costs related to storage and insurance.
The main outputs to the calculation are as follows:
- Stock quantity – quantity we should keep in inventory.
- Re-order trigger quantity – when we use spares, by how much do we deplete the stock in order to trigger a re-order?
- Re-order quantity – how many do we order in to re-stock.
Example using above outputs: our sparing program requires Quantity 1 in stock. When stock level falls to Quantity 2, we reorder Quantity 3.
The diagram below shows the input table for some of the above-mentioned variables.
In addition, as the RAM model can deal with a wide variety of equipment, it allows us to define and manage pools of spares. A spares pool is crucial when multiple equipment are sharing the same type of spares.
In summary, the RAM model turns out to be a method of choice for defining economical inventories. This is mainly due to the fact that the model accounts for a large number of equipment but also because it takes into account the life characteristics of each individual equipment.
Leave a Reply