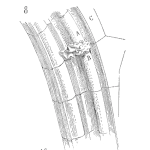
You are an engineering manager overseeing product development. For the new offshore product developed by your team, you want to know:
- If the final design margins comply with company standards
- If the thin-wall components are susceptible to Bauschinger Effect
- Which load factors were used for the ASME section 8 analysis.
And there may be other questions, such as:
- Were FMEAs conducted?
- Was a Basis of Design created for the product?
- Who conducted the design risk assessments?

These questions relate to design risk management, and possibly regulatory compliance. With the right program, de-risking activities can be identified, executed, and documented for maximum value during product development. In the best programs, de-risking activities are assessed by a Subject Matter Expert (SME) who is not affiliated with the design team. In Quality and Reliability in Oilfield Equipment, we learned that these are attributes of a competent OEM DfR program. And a DfR program provides value in other ways:
- De-risking activities can be selected based on project TRL; this ensures that the volume of de-risking activities is appropriate for the technology-application combination.
- De-risking activities begin in the conceptual stage, enabling mitigations to be implemented when most cost-effective.
- De-risking activities are conducted throughout the project, which minimizes reliability issues during commercialization.
If the OEM practices Design for Reliability, the manager’s questions can be answered during, rather than after, development. This means fewer surprises at commercialization time.
TRUTH #1: DfR programs enable design de-risking during product development.
TRUTH #2: DfR programs minimize reliability issues during commercialization.
This is the 5th in a series of 10 articles on critical equipment design for offshore completions.
Leave a Reply