
Metal strength and fracture toughness are important mechanical properties for components exposed to fatigue conditions and components with stress concentrations. Optimization of the two properties through alloy selection and component fabrication must be considered when designing components for these situations.
For structural components, strength and fracture toughness are two important mechanical properties. Yield strength is the stress a metal can withstand before deforming. Tensile strength is the maximum stress a metal can support before starting to fracture. Fracture toughness is the energy required to cause a material that contains a crack to fracture.
As a metal’s fracture toughness increases, the energy required to cause a pre-existing crack to instantaneously grow to fracture increases. For a component with a crack of a certain length, as the fracture toughness increases there is an increase in the component’s ability to support the load without fracturing. Said another way, for a certain load, as fracture toughness increases, a component can tolerate a longer crack before fracturing.
Fracture toughness vs. strength
As shown in the figure, fracture toughness decreases as strength increases. Both properties can be modified through alloy composition, mechanical treatment, and thermal treatment. For many alloys, different processes can be used to get different fracture toughness vs. strength curves.
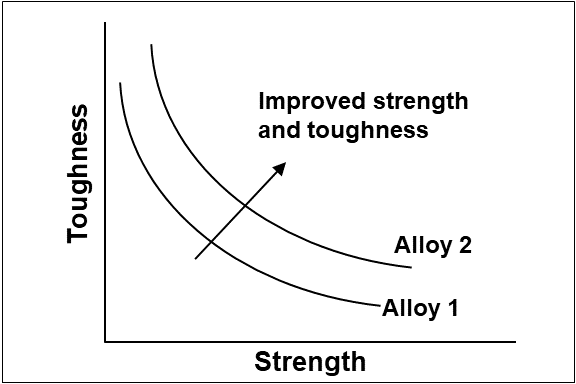
When designing components, engineers are often tempted to use a material that is as strong as possible to enable reduction of component cross-section. This can inadvertently lead to using a material with insufficient fracture toughness to withstand fracturing if a crack forms in the component during manufacturing or use.
Modifying toughness and strength
There are a few options when a component, made of a particular alloy and fabrication process, does not have the fracture toughness and strength needed
- Use a different alloy
- Use different fabrication processes
- Use a different alloy and different fabrication processes
Fabrication processes include the mill or casting processes used to make the metal, subsequent mechanical processing, and heat treating. For example, the toughness vs. strength for a cold-rolled carbon steel alloy is different than for the alloy after a quench and temper heat treatment.
Fatigue and stress concentrations
One common source of cracking during use is exposure to fatigue conditions. When designing components that will be exposed fatigue conditions, fracture toughness data is used to predict how long the component can remain in service before a crack grows beyond a critical length and the component fractures. This applies to aerospace components and pressure vessels such as boilers.
Another situation where fracture toughness is important is when a component has a design feature that is a stress concentration, such as a notch or sharp corner. The stress concentration results in high local stress. If the material’s fracture toughness is too low, the high local stress at the stress concentration will cause the component to crack and fracture.
Optimizing strength and toughness
So, there are situations when designers must be concerned with a metal’s strength and fracture toughness when designing components. The strength must be large enough for a component material to withstand applied loads without deforming. The fracture toughness must be sufficient for a component to withstand the presence of cracks or stress concentrations without fracturing.
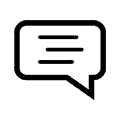
Leave a Reply