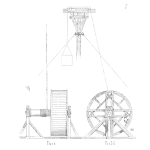
One of the more confusing distinctions for quality professionals, especially those working within one of the quality management standards such as IATF 16949 or ISO 13485, is the difference between a Corrective Action Request (CAR) and a Preventive Action Request (PAR).
On the surface, CAR’s and PAR’s look nearly identical. Both are used to improve a process or design. Both commonly employ the use of an “8D” format where key steps such as the root cause, containment activities and verification are detailed. And both are required by most of the big quality standards. But the key difference between a CAR and a PAR is its origin.
For most organizations, CAR’s get more attention than PAR’s because they originate with some sort of failure like a customer complaint, field recall, audit finding or similar event. In other words, CAR’s are initiated when something bad happened. Since failures like these often get the attention of an organization’s management staff, their resulting correction and documentation get a high level of attention as well.
PAR’s on the other hand don’t originate with a failure. Instead, they originate as an opportunity for improvement discovered through benchmarking, brainstorming, a new technology, or similar trigger. With a PAR, nothing bad happened, but someone is working to lower costs, improve quality, increase throughput, etc.
In either case, the 8D process works well to identify the problem or opportunity, detail the process or design change, and then verify the effectiveness of the improvement.
For a deep dive into root cause analysis, CAR’s, PAR’s, and a range of corrective action strategies, sign up for the online course titled, “Root Cause Analysis and the 8D Corrective Action Process”.
Leave a Reply