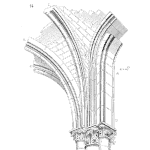
On page 6 of Statistics for Experimenters, Box, and Hunter suggest a scientist could conduct an investigation without statistics.
Whereas, a statistician could not do so without scientific knowledge.
The text’s discussion quickly expands on the benefits to a scientist when they do employ statistical thinking and tools.
Design of Experiments, DOE, is a set of statistical tools that allow an investigator to efficiently examine multiple factors and their associated influence on results.
DOE allows us to be better investigators.
For reliability engineers, DOE is a tool
- to augment design and process development,
- to accelerate failure analysis
- to optimize supplier selection
All to enhance product reliability.
The number of contributing factors
When I was in college, a few of the electrical engineering labs including setting up a circuit, then exploring how the system response changed as I altered a resistor value.
Or, change out a capacitor, or another single element of the circuit. We were learning about basic circuit design and how the components worked to influence the output.
One factor at a time.
Great for learning about resistors, yet not so great about learning about the system.
Granted the circuits we used we very simple and we probably did learn a bit about the system output, yet not when both the resistor and capacitor used their maximum values.
We didn’t explore interactions between the components.
At times it makes sense to hold everything stable and explore just one variable. This doesn’t happen very often outside a classroom.
Sometimes we explore a variable against a standard, or against another option.
For example, comparing two components from different vendors on the design’s performance may require the use of a hypothesis test. Comparing two things benefits with the statistical tool called a hypothesis test.
You may be familiar with this tool.
What happens when you have three vendors, for each of 5 parts? Or, you want to explore the impact of seven different environmental stresses on the aging of your product?
Running one at a time or pair-wise comparisons is not practical and often uninformative.
Instead, use the appropriate design of experiments approach
- to identify the important factors
- to explore factor interactions
- to determine robust solutions
DOE tools allow you to explore multiple and possibly interacting variables in a cost effective and efficient manner.
The noise that variation creates
Noise in experimental data is the result of variation caused by factors we either cannot or chose to not control.
Measurement error in one element of noise. Another is local temperature changes within the sample under test over the span of the experiment.
There are literally hundreds, if not thousands of sources of noise for any measurement.
Statistical tools, such as DOE, are designed to minimize the volume of noise so we can view the factors of interest as they influence the system results.
DOE tools may provide the ability to isolate or block the effects from clouding our understanding of the design parameters in question.
Another view of noise includes our ability to craft a compromise solution that optimizes the result despite the many sources of noise.
Taguchi talks about finding a robust solution. A solution that works well given the broad range and variety of noise it will experience. The system may not be finely tuned for optimal conditions, yet function well across all the sub-optimal situation that will exist.
Noise and the resulting influence on results rarely occurs in isolation or in economically controllable ways.
It is our product’s reality.
Our experimentation should embrace the richness of the variability that is there and DOE helps to manage the noise.
Long life and DOE experimentation
Reliability testing often attempts to cheat time or explore a wide range of end-use conditions.
Reliability testing is brutish, expensive, and time-consuming. As much as I enjoy testing, it is something I have regularly avoided.
When reliability testing or experimentation is necessary to answer questions, it is well worth the extra effort to garner as much meaningful information as possible from the testing. That is where DOE plays an important role.
If I have a fairly well understood failure mechanism, such as solder joint fatigue, using test boards to explore a new solder joint geometry may be all we need for the life testing.
This, of course, assumes the thermal gradients across an active board, the effects of forced air cooling, the addition of even modest fan vibration, not to say anything about the assembly, storage, handling, or installation stresses, this assumes, all have an insignificant effect on the solder joint resulting expected life.
It is rare that a product only experiences relatively high temperatures without being powered on and working, along with relatively high humidity, and vibration, power line fluctuations, varying loads or demands, a bit of dust accumulation, and quite often UV or chemical material degradation.
Our products face a multifaceted sequence of stresses that each and together strive to degrade or destroy our products.
Evaluating high temperature over life for a new IC provides a shrouded view of its potential life.
Use DOE with reliability testing to acknowledge the reality of the noise world our product will experience.
Summary
In short, DOE lets us explore more than two factors at a time.
DOE tools enable screening for important factors, optimization of design for salient factors, and evaluation of robustness in the face of noise from many sources.
A little up front planning for your experiment will help you learn as much as possible from your experimentation work.
Leave a Reply