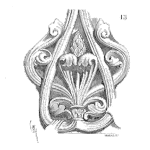
Bag house dust bag selection. The dust bags within a bag house must handle the process conditions they experience. The choice of bag materials is usually based on the cheapest fabric that will handle the conditions for a minimum of 3 to 5 years’ operation. The selection of the bag materials requires a good understanding of the process temperature, moisture content, chemical reactions with the bag fibre, dust loading effects and behaviour of the dust bags in operation.
Keywords: pulse jet dust collector,
Construction of Collector Bags
Dust bags are manufactured in either tubular shape or as an envelope. They consist of a bed of woven or twisted fibrous material with the surface worked (usually with serrated needles) to further intermingle the outer layers of fibre. In the early days of the technology the bags were cotton, hemp, jute, etc but currently the materials are typically plastic.
The bag is made from a cut sheet of fibre folded into the required shape and stitched together. The bag consists of an open top collar that sits in a holder or tube-sheet plate and suspends the rest of the bag while forming a dust tight seal with the carrier. The collar is sewn to the body of the bag and the bag is sewn its full length. On tubular dust bags a round bottom is sewn to the base to complete the bag.
All stitching must at a minimum be double stitched to provide strength and longevity of service.
The bags are prevented from collapsing by a 2 – 4 mm thick, metal wire cage skeleton inside the bag. The metal used for the cage also needs to be selected to suit the process conditions. In damp environments the bag sticks to the cage and it is impossible to remove it without destroying the bag.
The dust bags are made 2 mm larger in size than the cages. This allows them to be slid onto the cage on assembly and for the fabric to be supported during operation. Insure that for tubular bags the bottom is also no more than 2 mm off the bottom of the cage to prevent excessive beating against the cage during air cleaning pulses.
Behaviour of Dust Bags in Service
Dust bags are cleaned either by pulsing air through the center of them or by mechanical shaking. The more severe of the two methods is the air pulse, but it is also the most effective, cheapest and easiest system to maintain.
The process dust is not meant to get through the fibres of the bag. The bags are designed so that the dust builds up as layers on the outside. The built up layers act as the filter medium and the bag is only the supporting structure to carry the dust layer. If the dust does get deep into the fibres the bag is destroyed as a filtering device.
It is critical that the gas velocities across the bags do not force process dust into the fibres. This will cause blinding and the filtration efficiency falls, the back-pressure on the bag rises and the bags are put under more stress and will fail at their weakest location. Blinded bags can be detected when dust clouds are observed discharging from the filtered gas outlet during the cleaning cycle. This means dust has migrated through the bag from the dirty to the clean side.
Pulse jet cleaning is an aggressive process. The sudden blast of air travels down the inside of the bag as a pressure wave flicking the bag off the support cage and the dust cake off the outside of the bag. After the pulse has passed by, the fan sucks the bag back onto the cage and it impacts the cage support wires. As this expansion and contraction process is repeated the fibres of the bag and stitching get beaten and stressed. Eventually the fibers tear apart, or the stitching breaks, and the dust escapes through the bag. Only pulse the bags when the differential pressure across is more than 1.5 kPa (6” of water).
High local velocities past bags due to poor collector design will abrade through the bag fibre. Make sure collector entry baffle plates are in place and the airflow is evenly distributed around all bags equally. Insure that no bags touch each other as movement will wear the fabric at the contact points.
Process Conditions Review
The bag material must be selected to handle the process conditions within the bag house dust collector. Both the maximum and the average temperatures must be measured, including how long the maximum temperature is sustained. As some fibres do not like damp conditions the level of relative humidity within the dust collector must be known. The level and type of acid or alkaline in the process gas needs to be checked. So to the amount of oxygen present in the gas stream, as highly oxidising environments are not liked by some fibers. The process chemicals in the gas stream need to be known to insure all aspects of bag fiber degradation are addressed. Finally the dust size range should be analysed so the correct size of fiber weave, or felt, and the amount of needling can be selected.
Tables No. 1 and 2 provides guidance on some types of filter bag fibers commonly available and their ability to accommodate various process conditions and resistance to chemicals. You will notice that some materials have poor chemical resistance but can handle high temperatures while others have good chemical resistance but low temperature limits. It is important to get the right fiber and stitching material in order to get the maximum cost effective bag life.
Fibre (Trade name) | Acid Resistance | Alkalis Resistance | Solvents | Oxidiser | Hydrolysis | ||
Polyester | 3 | 3 | 1 | 2 | 3 | 4 | 1 |
Polypropylene | 4 | 4 | 4 | 4 | 4 | 3 | 4 |
Polyamide (Nylon) | 1 | 3 | 3 | 3 | 3 | 3 | 2 |
Polyaramid (Nomex) | 2 | 3 | 3 | 3 | 3 | 3 | 2 |
Acrylic – homopolymer | 3 | 3 | 3 | 3 | 3 | 3 | 3 |
Polyphenylene Sulphide (Ryton) | 3 | 3 | 2 | 2 | 3 | 1 | 2 |
PTFE (Teflon) | 4 | 4 | 4 | 4 | 4 | 4 | 4 |
Note: 1 Poor, 2 Fair, 3 Good, 4 Very Good.
Table No. Fibre Resistance to Chemicals
Fibre (Trade name) | Specific Density | Tenacity (Tensile Strength) | Con. Operating Temp °C | Max Short Duration Temp °C | Price Ration |
Polyester | 1.38 | 60 | 150 | 170 | 1 |
Polypropylene | 0.91 | 50 | 90 | 100 | 1.4 |
Polyamide (Nylon) | 1.14 | 60 | 110 | 120 | 1.2 |
Polyaramid (Nomex) | 1.38 | 33 | 220 | 250 | 5 |
Acrylic – homopolymer | 1.15 | 35 | 135 | 150 | 1.5 |
Polyphenylene Sulphide (Ryton) | 1.37 | 35 | 190 | 200 | 5 |
PTFE (Teflon) | 2.3 | 18 | 250 | 260 | 20 |
Table No 2. Fibre General Properties
Mike Sondalini – Maintenance Engineer
If you found this interesting, you may like the ebook Process Control Essentials.
Leave a Reply