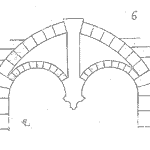
The only true way to prevent asset failure is to prevent the causes of microstructure failure from occurring.
Machines fail when their component’s microstructure is degraded or deformed to a point where it can no longer bear the load. If you prevent degradation and deformation from occurring a machine and its components will provide an exceptional lifetime. However, you must do this at every phase of the asset’s life cycle to get world class reliability.
The table below lists just some of the hundreds of ways that a component’s microstructure can be destroyed. These events can occur at one or more phases in the lifecycle of a component. As such, it is important that quality controls are used, and quality assurance provided to prevent these events from occurring throughout an asset’s and its parts’ lifecycles.
Most operators will only have control over these events occurring during installation, operation, and maintenance phases. So, it is important to select and use asset designers, fabricators, and manufactures that consistently produce high-quality products by following robust and reliable processes and procedures. Otherwise, you are placing your operation’s future at unnecessary risk for all its operating lifetime.
Once it is sure that there will be no unexpected microstructure failure you know you have a highly reliable piece of equipment. You can put your faith in it knowing it will run as intended for its whole service life. Once all your operating assets have outstanding reliability then you will have a world class reliable operation, along with all the extra operating profits it will bring you forevermore.
Table 1. How hundreds of potential causes of microstructure failure can occur during an asset’s and its parts’ life cycles
Principle Factor of Solids Microstructure Failure | Component Manufacturing and Rebuild Events | Component Operational Stress Events | Component Degradation Events / Conditions | Electronic / Electrical Degradation Conditions |
Force Overload – compressive, tensile, shear, cyclic, shock | Error during manufacturing (metallurgy, formulation, process conditions, chemical composition) | Pressure | Temperature range (too high or too low) | Electrical discharge / arching |
Change of state (melting) | Fitting (loose or tight) | Vacuum | Erosion | Ionization |
Crack in structure | Incorrect, misaligned or missing parts | Rotational torque load | Corrosion | Power dissipation |
Missing material | Stress or damage due to welding | Shrinkage | Acidic atmosphere | Contact wear |
Ripped material | Scratches, gouges, burrs, etc. | Expansion | Humidity | Short circuit |
Electromagnetic radiation | Vibration | Abrasion | Lubrication degradation | No or inadequate grounding / earthing |
Chemical radiation | Excessive rigidity, or movement | Friction | Chemical attack | |
Electrical discharge | Insufficient rigidity or movement | Buckling | Environmental factors (rain, dust, sand, mist, animal interference etc.) | |
Long-term creep | Incorrect quality or quantity of lubricant | Fracture | ||
Leaks | Solid object impact | |||
Incorrect tool used | Under or overloaded operating conditions |
Ensuring lasting component microstructure reliability is the natural outcome of using Plant Wellness Way EAM. The methodology gets you to consider and prevent the many ways by which your plant and equipment and their parts can fail in their operating environment. Eliminating microstructure failure through use of highly effective business processes and work procedures becomes the normal practice in organizations using PWW EAM.
If having world class operating asset reliability is what you want for your company, please make contact and ask us how to use Plant Wellness Way to create that future.
Leave a Reply