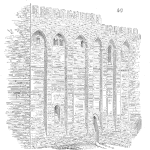
Unless you are working with raw materials directly, you rely on your suppliers to provide reliable parts.
Do you suppliers know your reliability objectives for the parts they supply?
If you didn’t tell them, they probably do not know. If you did tell them, did you make it the reliability specification clear and understandable?
As with any specification, clear communication is essential. Guessing or assuming both parties know and have the same reliability goals is, well, not a good practice. The ability of a supplier to build and deliver the parts that meet all your specification has to include a clear and understandable reliability specification.
There is a range of common reliability specifications in use, some are better than others. Let’s start with a brief review of reliability specification types.
Then briefly outline how you establish the reliability specifications for each supplied component.
Common reliability specifications
Reliability – the probability of successful operation (function) within a stated environment over a stated duration.
MTBF – Mean Time Between Failure: a measure of repairable system reliability, typically expressed in hours or months, equal to the reciprocal of the Hazard Rate when it is constant (when failures are random in time – the exponential distribution).
MTTF – Mean Time To Failure: a measure of a non-repairable component’s reliability, typically expressed in hours or months. The determination that a component is non-repairable is often an economic choice rather than a physical impossibility.
FIT – Failures in Time: The rate of expected failures per unit of time. Commonly used to represent the number of failures expected over one billion (109) device-hours of operation. The relationship of FIT to MTBF may be expressed as: MTBF = 1,000,000,000 x 1/FIT. Some use FIT with one million hours (106) instead.
MTBMA -Mean Time Between Maintenance Actions): A measure of the system reliability parameter related to demand for maintenance manpower: the total number of system life units, divided by the total number of maintenance actions (preventive and corrective) during a stated period of time.
MTBUR – Mean Time Between Unscheduled Removal: A measure of the system reliability parameter related to demand for logistic support: the total number of system life units divided by the total number of unscheduled items removed from that system during a stated period of time.
MTTR – Mean Time To Repair: a measure of repairable system serviceability, typically expressed in minutes or hours. Generally the time from when a problem is discovered until the system is usable, although in some industries this is more narrowly defined.
Availability – Fraction of time that a system is usable. Steady state Availability = MTBF/(MTBF+MTTR). Be sure to specify if the specification is inherent, achieved, or operational availability as each included different contributors of downtime.
There are related requirements or constraints that you may add to a reliability specification. We will save that discussion for another article.
Establishing reliability specifications
You can set whatever reliability goal you would like.
Ideally, we all could specify the supplied part will never fail. This isn’t realistic nor economical to prove, if even possible to prove it would never fail.
We have to set requirements for what we want, balanced with what is possible. If you are familiar with process capability, you know it is a measure of a supplier (a process) to create items that meet specification along with the probability of items falling outside the specifications.
Unlike measuring length or voltage, measuring reliability may be a complex process. Thus making the application of process control and process capability analysis difficult.
Ideally, we set reliability specifications such that each supplier can meet the requirements with some margin. In addition, when all the items meet specifications, and the product is assembled well, the system will meet its system reliability requirements.
In an ideal world, each part will be as reliable as necessary and not more so. Since time to failure variability will occur, we should consider adding a cushion to the reliability specifications to improve the ability of the system to meet its goals.
Modeling and apportionment
Reliability block diagrams (RBD) provide a great way to arrange the elements of a system reliability-wise.
It also provides a framework to apportion the system reliability goals to the elements. For a series reliability set of elements, the reliability of the higher element is the product of the reliability values of the elements.
Using RBD you can model series, parallel, complex, keystone, and k-out-of-n configurations. You are also able to model various forms of redundancy.
There are multiple ways to apportion reliability to subsystems or elements of a system. Even starting with an equal apportionment technique is suitable as it provides a starting point to refine the apportioned values.
The ARINC apportionment technique does make the assumption of constant failure rates, yet also incorporates the current element failure rate information into the apportionment process.
The resulting apportioned reliability values are just a starting point. Decorating the goal for one part to accommodate a supplier’s capability, will require increasing the goal for one or more other parts.
The accumulation of the part goals still has to result in achieving the system reliability goals.
Stated supplier reliability
One way to start the reliability apportionment process to establish reliability specifications is to use the supplier’s reliability performance directly.
If the vendor claims the part will have a 98% reliability over 5 years, use that value. Adjust the value to the time frames desired. Or, use supplier provided life distribution data directly in a modeling tool such as ReliaSoft’s BlockSim.
When possible adjust the supplier’s goal often based on a set of environmental conditions to your products set of conditions.
By setting the reliability specification to the vendor’s claimed reliability performance, we can quickly check if we will still meet the system reliability goal, or not. Also, supplier’s are more likely to meet their listed reliability performance, than meeting a potentially more stringent objective requested.
The values from vendors are just starting points, as in the top-down apportionment processes described above. The intent is to start with the information you have and adjust and refine the reliability specifications as needed.
Field data estimates
If you have been using a particular pump in other products with a similar set of applied stresses, you may find your own field data provides an excellent way to estimate part or subsystem reliability.
This approach has the benefit of being a customer used system without making any assumptions about stress levels or use conditions.
In practice, we use a mix of all these methods to establish reliability specifications for use with suppliers. The more realistic and accurate the data the better the actual results will match the objectives.
The key is to use all available data to define the reliability goals. Equally important is clearly stating the reliability specification to the supplier in such a way that they fully understand the requirement.
Related
Approaches to Assess Customer Reliability Needs (article)
3 Elements of Reliability Goal Setting (article)
RBD and Design Process (article)
Reliability Apportionment (article)
Why Should a Supplier Work Harder For You? (article)
SOR 055 What To Do When Supplier Changes Your Reliability Specification (podcast)
SOR 045 Supplier Not Meeting Your Reliability Requirements (podcast)
Great article Fred. Thank you
Thanks Henry, much appreciated. cheers, Fred