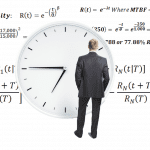
One of the most difficult challenges of incorporating reliability activities with program planning is estimating the time it will take to demonstrate reliability. Demonstrated product reliability is typically measured as a confidence in a product’s capability to achieve a reliability goal. At product release, the business unit may feel comfortable with their target market and warranty goals with a demonstration of a 90% confidence in the products reliability goal of 99.1%.
Achieving a demonstrated 90% confidence in a product is in direct opposition with any “time to market” goal that has been established, no matter what the product or technology is. There are several ways to translate test time to demonstrated confidence. Using one common method this confidence of 90% in a 99.1% reliability would take running 254 production equivalent units to full life, with no issues. So the reliability team is effectively asking the program if they can be the first customer and have enough time and resource to run 254 products to life. I have never in my career seen a request like that granted, or even seriously asked. I think you would mention those figures only to put your actual request in perspective.
The reliability demonstration program will then typically take a two-prong approach. A “Reliability Growth” (RG) program will be launched as soon as the first full system prototype is available. This program will look to systematically measure and improve the reliability by running the system in a manner as close as possible to a customer use case and environment. The RG program will permit for a growing confidence in the reliability goal to be demonstrated. This confidence measurement will assist with program management decisions by producing a quantifiable risk of the product being able to achieve it’s reliability goal. Specific confidence percentages can be associated with program phases.
- At the completion of the “Proto 2” phase, a confidence of 30% will be demonstrated.
- At the first “trial production run” a 60% confidence will be demonstrated.
- At release, a 70% confidence will be demonstrated.
The second prong of the confidence demonstration approach is executed at the sub-assembly level. A reliability allocation model can derive reliability goals for sub-assemblies based on the high-level product goal. This can be advantageous because often sub-assemblies are available for test before the high-level system is ready to be operated. If there are subassemblies that are high-risk they can go through the “test and fix” iterations with a specific goal. This is instead of an open-ended improvement that may be stopped too early or continue unnecessarily.
The key is to synchronize with the program leaders early in the planning process. Expectations for what can be demonstrated at each phase of the program should be set. This goes both ways. The reliability team communicates that it is not possible to demonstrate a 90% confidence in a 99% reliability unless they are willing to postpone release by 10 months from the original product date. The program leaders understand what they will have to provide with regard to test units, resource (fixturing, lab space), and program schedule to achieve the agreed upon program goals.
-Adam
Reliability Demonstration Testing (RDT) is ideally performed when the product development is stable, with all design flaws removed. For most companies RDT is performed at either the Pilot Production phase, or first mass production as a final qualification before initiating full blown production.