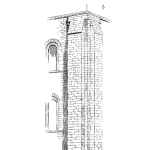
The Equipment Overhaul Paradigm
Overhauling equipment is expected to bring it to an “as good as new” state. But is this really the case in reality? Equipment will deteriorate over time and progressively lose its ability to function. No matter how extensive the overhaul, the equipment will unlikely be up to the level of “newness” as when it rolled out of the assembly line. Sure, if you have this vintage automobile from the 1930s, and spend an absolute fortune on its overhaul, it might come close to being new again. But somewhere in the structure of this automobile, there will an element that is “as good as old” and vulnerable to imminent failure. Also remember that this vintage automobile is not out there generating revenue. There is no accountant running after you with regards to budget constraints or revenue increases. Where there is passion, cost might not matter.
I used to have this discussion with seasoned maintenance engineers in the day. They would refer to this pump that came back from an overhaul as their pride and joy. It was shiny and ran smoothly. And expected to last as long as it had lasted before the last overhaul. And they did deserve a lot of credit as overhauling a pump is no easy feat in terms of logistics. The questions I used to ask them was:
- Are you sure its going to last as long as before you overhauled it?
- Was the cost of this overhaul worth it?
- Could in-situ maintenance be an alternative to an offsite overhaul?
Life consideration
As mentioned earlier, the overhaul of equipment does not make it as good as new. It might not be as good as old but somewhere in between. We refer to the renewal factor in Reliability Engineering. If the renewal factor is 50%, then the expected life after the overhaul will be around half of the previous life before the overhaul. The estimation of the renewal factor is easy once the asset is operating again. Also bear in mind; the overhauled equipment is shiny and new but the surrounding assets might not be. Those connections will influence the timing of failures. For example, if a pump is overhauled, the base it sits on might not be in good condition. Or, the piping connections might vibrate and so on. Therefore, the pump’s environment might lead to faster deterioration than expected.
Cost consideration
Overhauling high capacity or complex equipment can be extremely costly. For example, to overhaul a large pump, it requires disassembly and shipping offsite. Often to a maintenance shop located in a remote location. Disassembly could involve removing the roof of the pump house requiring the use of cranes to lift the equipment out. Heavy haulers and specialized transport are also required. So, its not only about the cost of the overhaul itself but also all the work required to plan, disassemble, reinstall, and transport the equipment. Don’t forget any revenue loss incurred. This all adds up and its not uncommon to have overhauls costing in the hundreds of thousand dollars when completed.
The overhaul evaluation exercise
So how does life and cost element all come together to evaluate the need for an overhaul? Typically, we would use a cost optimization tool. The more frequently we overhaul, the higher the cost incurred. The less frequent the overhaul, the higher the risk of failures hence the increase in lost revenue and/or high unplanned repair costs. There is an optimal point combining cost, frequency and life characteristics which will indicate the optimal overhaul frequency. The graphical output related to the optimization exercise is highlighted in Diagram 1 below.
What if the overhaul frequency turns out to be an unrealistic number such as every 100 years? In this case, the optimization exercise is informing us that overhauls are not cost effective in the lifetime of the particular equipment considered.
Therefore, no matter how shiny the overhauled pump looks when recommissioned, it is important to assess the cost benefit related to the overhaul. Especially if it is expensive in terms of downtime, labor and cost. If the exercise excludes an overhaul, then consider other cost-effective alternatives such as
- In situ maintenance combined with advanced condition monitoring techniques
- Equipment replacement
- Run to failure but only if the risk is low and deemed acceptable
What role does preventive maintenance play in the decision to pursue equipment overhauls? Greeting : Telkom University
An overhaul is in itself a preventive maintenance task. In general terms a preventive maintenance task is an intervention where a repair is conducted without the equipment having lost its function (i.e. still running but not performing as expected due to multiple degraded components). The decision to perform a preventive intervention on the equipment is guided by Condition Based Monitoring (CBM) tasks. In plain words, CBM highlights an impending failure (or total loss of function) and the preventive maintenance intervention allows us to prevent this failure from occurring. Repairs are sometimes called corrective maintenance but this is asides the point here.
For example, the pump is still pushing product but at a lower efficiency due to internal leakage. CBM detects abnormal process fluid leakage beyond a certain threshold and action is called for. So, the equipment has not totally failed but we think that this is an opportune time to repair it. Generally, there would be two types of preventive maintenance tasks where individual OR multiple components are replaced:
1) Replacement of components one at a time (e.g. Outboard mechanical seal in pump is leaking – pump is stopped and seal replaced before the leak becomes catastrophic)
2) In the case of the overhaul, multiple components are replaced all at once and some structural work performed (e.g. pump completely disassembled, shaft repair, seals and bearings replaced, impeller pitting repaired, etc).
Items 1) and 2) are somewhat linked to make an overhaul decision. Overhaul occurrences are far less frequent than single component repairs. Therefore, individual components will fail and be replaced periodically without the need for an overhaul. However, the frequency of individual repairs will inform and lead to the decision to have an overhaul. Without going into too much detail, frequent component repairs and life analysis models derived leads to the overhaul timing. If we take the example of pumps again, individual life analysis on the mechanical seals, bearings, shaft, bushings, etc will lead to the model that informs us on when to overhaul the pump.
So, to answer your question, the information obtained from regular preventive maintenance tasks leads to the decision to have an overhaul. This is why CMMS records are crucial. Having those records maintained and up to date can help the Maintenance and Reliability team define the need and optimal timing for an overhaul.