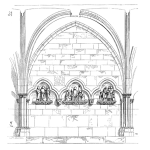
Example ACE 3T (Target-Tolerance-Test) Procedure with Reliability Standards: Machine performance is totally dependent on human beings. To address the problem of human error causing equipment failure, an Accuracy Controlled Enterprise sets best practice quality standards and uses 3T Target-Tolerance-Test work task quality control that assures high quality workmanship for high reliability results. Their work procedures are standardised so everyone follows the same methods to produce the same results, their training teaches people how to do craftsmanship work that creates outstandingly reliable plant and machinery. They create the reliability they want and as a result achieve operational excellence.
Keywords: precision job procedures, maintenance work quality assurance,
High equipment reliability requires parts made to precise sizes and assembled to precision standards. Our machines and equipment are dumb, lifeless objects that cannot tell they are suffering and in trouble. They cannot adjust their behaviour when stress and strain gets too much. They just brake and die. It is up to us to make machines work properly by ensuring they are made well and kept healthy. If we want high equipment reliability we need to use the skills, methods and processes that produce high equipment reliability.
Maintenance work processes that deliver better than 3-sigma quality accuracy (7 errors per hundred opportunities for error) are uncommon in industry. Most maintenance and repair work processes range from 2-sigma to 2-1/2-sigma, or 30 to 10 errors respectively per 100 opportunities1. You can truly say that due to human error maintenance destroys the equipment that it is meant to maintain reliably. To address that problem an Accuracy Controlled Enterprise creates high quality work procedures full of double-checks and measurable task quality standards that must be met. An example ACE 3T Procedure with work reliability quality standards for mounting spherical roller bearings on shaft adaptor sleeves in Plummer blocks follows.
With an ACE 3T procedure high maintenance work quality is assured. It also brings many other wonderful benefits to organisations that chose to become great at operational excellence. It sets standards that everyone must adhere to, from equipment vendor to subcontractor to employee to professional engineer. It allows workmanship skills to be trained for targeted reliability outcomes. It drives continuous reliability improvement as people reach higher and higher workmanship quality standards and become an Accuracy Controlled Expert. ACE 3T procedures are written at three levels of work quality performance. The lowest work quality level is the best of current site practices; it is ’bronze medal’ level performance. The third level is set at world class reliability standards and tells everyone where they need to be if they want to deliver ‘gold medal’ results reliability (To be that good takes training in precision maintenance skills, use of quality control proof-tests and a mindset that values high quality workmanship.). In-between is the intermediate level, which is a hard stretch target above the best existing level of work quality; it is ‘silver medal’ standard.
Writing an ACE 3T maintenance procedure takes a lot of research into the fine technical details of what delivers ultra-high reliability, you need to appreciate and understand exacting engineering standards and be able to decide which apply in a situation, it needs a good grasp of the reliability of a design and of materials of construction issues. It is the work of technically competent and engineering knowledgeable persons working together with trade savvy people to create a document that helps technicians to do expert, masterly work first-time, every-time.
Best regards, Mike Sondalini
1 Smith, Dr, David J., Reliability, Maintainability and Risk, Seventh Edition, Appendix 6, Elsevier, 2005
ACE3TProcedurePlummerBlockExample
Leave a Reply