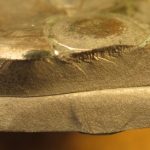
Here’s an example of how a metallurgical failure analysis led to identification of the root cause of a failure, and to identification of the corrective actions needed to prevent the failures from recurring.
Failure analysis
As I discussed in my previous article, metallurgical failure analysis can be used to improve product reliability. The information from failure analysis of a failed component is used to determine the root cause of the failure. Once the root cause is identified, the failure analysis data and findings is used to help identify the corrective measures required to prevent the failure from recurring.
Failure example
Stainless steel paddles used in industrial mixing equipment were fracturing during use. The paddles consisted of a stem (machined bar) welded to a plate. The paddles were attached to a shaft that ran the length of the inside of the equipment by screwing the stem into the shaft. As the shaft rotated the paddles stirred the material being processed.
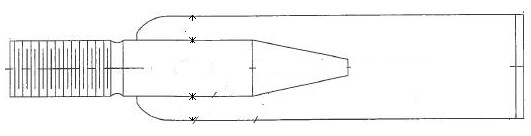
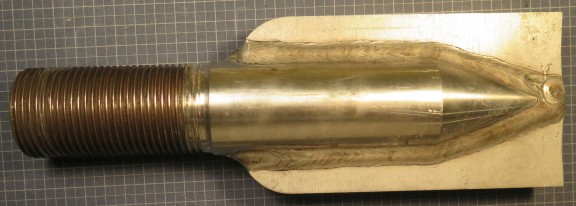
The failure analysis indicated the failure mechanism was reversed bending fatigue – the paddles were exposed to cyclic stresses that caused bending backwards and forwards. Also, the failures occurred at the tip of the weld between the paddle shaft and plate. The weld joint was a stress concentration, resulting in higher stresses at the weld compared to the other parts of the paddle. The composition and microstructure of the paddle materials and weld joint met their specifications.
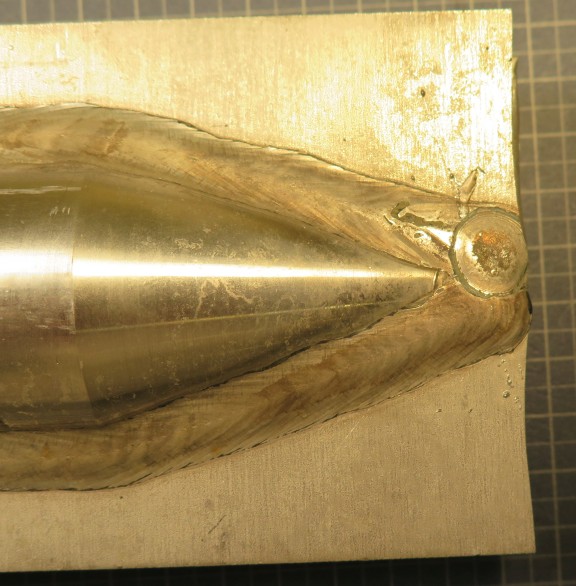
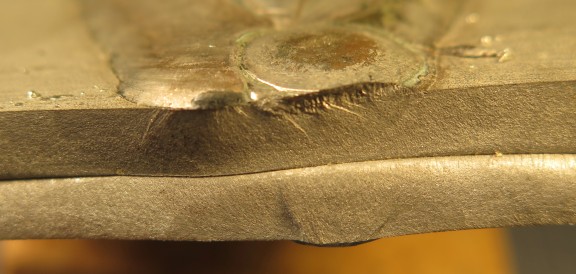
Failure by reversed bending fatigue seemed odd because the equipment shaft spun in only one direction. A little additional research revealed that motors can experience transient acceleration and deceleration due to fluctuations in the power supply. This was investigated and it was determined that there were a few problems with the power supply to the motor that spun the equipment shaft, resulting in large voltage spikes and erratic motor behavior.
Two root causes and fixes
For this failure there were two contributing root causes – a paddle design with a stress concentration and an unstable motor power supply. Changes to the power supply resulted in elimination of the large voltage spikes and improved the motor’s behavior, resulting in less stress on the paddles. That changed resulted in a large reduction in the number of failure and time between failures, but not complete elimination.
The paddle design was also changed to eliminate the stress concentration – the entire paddle was cast as one piece. The change resulted in complete elimination of failures during use.
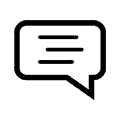
Interesting. Thanks. Given that castings have their own gremlins to manage, I might have also considered moving the start/stop of the welding process away from the ends of the welded joint along with evaluating the transition in section. But there are more ways to skin a cat, and success is in the details.
I agree, there are different options for making improvements. For the situation casting was used because of familiarity with it.