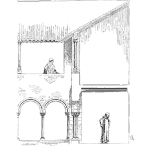
What readers will learn in this article.
- How pneumatic actuators work.
- Air pressure requirements for proper operation.
- Air supply piping installation requirements.
- Air quality requirements for long life operation.
Pneumatic (air operated) actuators are the preferred device used to automatically open and close quarter-turn valves. A quarter-turn valve goes from fully open to fully close in 90o of rotation. Examples are butterfly, plug or ball valves. Figure 1 shows an actuated butterfly valve in a pipeline operated by a solenoid valve.
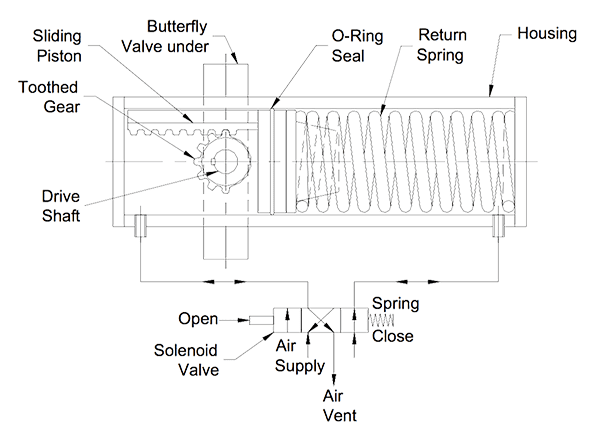
To open the valve automatically from a remote signal a mechanically operated actuator is mounted on top of the valve. The pneumatic actuator connects the valve stem to a piston inside the actuator. A solenoid valve directs air to one side of the piston or the other and the stem rotates.
The solenoid valve contains an electric coil, a shuttle plunger and a spring. The plunger covers openings within the solenoid body. When power is applied to the coil it becomes magnetised and pulls the shuttle into place. When the power is turned off the spring pushes the shuttle back. The electric power is turned on and off by a signal from the process computer. When the solenoid operates, compressed air flows through the open ports and onto one side of the actuator. The piston moves and the valve stem rotates.
The actuator can contain a spring that pushes the piston back into place on release of the air pressure. Actuators that are closed by a spring are called fail-close actuators. If air pressure is lost the valve will be closed by the spring and stop the process flow through the pipe. There are fail-open actuators where a spring keeps the valve open and air closes the valve. Double acting actuators need air to both open and close the valve.
When selecting pneumatic actuators make sure the actuator can produce a greater torque than that needed by the valve. Butterfly valves used as outlet valves on silos of powdered product can bind when the product causes the torque between the disk and seat to increase above the capacity of the actuator. Air lines to the solenoid and the actuator should be the same diameter, and even one diameter larger, than the port connection. This permits the air to quickly flow to the piston chamber for rapid response. It also gives the piston a sudden surge to help break any seating torque.
Instrument quality air is best for long-lived reliable operation of air operated actuators. In particular moisture must be removed so it does not condense in solenoids and actuators. Trapped moisture causes corrosion inside the actuator and solenoid bodies and can hydraulically lock the piston at part-stroke and stop the valve from turning.
Insure the pressure dew point of the compressed air is well below the coldest distribution system temperature.
Mike Sondalini – Maintenance Engineer
If you found this interesting, you may like the ebook Bulk Materials Handling Introduction.
Thank you for all the information about pneumatic actuators. I know my husband has been working with them lately, and I wanted to learn more. That is really cool that they are devices that are used to automatically open and close quarter-turn valves.