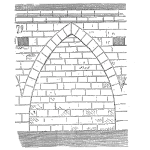
Coatings provide industry with low-cost solutions to difficult chemical corrosion problems.
This article covers the use of rubber, fiberglass, and epoxy linings.
Keywords: rubber lining, resin, composite glass fibers, overlap joints, adhesive, primer, corrosion barrier, repair.
To select an appropriate lining material the supplier must be told:
- the chemical(s) in contact with the lining
- the range of concentrations
- the process temperature range
- the pressure conditions
- whether the item to be lined is old or new
- whether there is agitation present
- the size and shape of the item
- whether the lining is to be done on-site or at their workshop
Rubber lining
Hydrochloric acid will corrode a 6 mm thick steel tank in a matter of hours, yet when the tank is lined with rubber, hydrochloric acid can be stored safely in it.
Rubber is available in a variety of types each with its own chemical resistant properties.
Successful rubber lining depends on the quality of the surface preparation, the adhesive used and the applicator’s skills.
The surface must be clean, smooth and solid. At least a class 2.5 surface finish as noted in Australian Standard 1627 part 4 is required for metal. A class 2.5 blast exposes the metal surface and removes all loose surface rust and dirt.
A class 3 blast is back to a completely bare metal surface. The adhesive must match the chemical resistance and temperature properties of the rubber.
The applicator must be experienced with the type of rubber used.
After the surface is cleaned a primer is applied.
Adhesive is put on the surface and the back of the sheet. The sheet is then laid and worked so all voids are removed.
The edges are beveled back sharply to make a wide incline. The adjoining sheet edge is beveled to the opposite angle. The second sheet is prepared in the same way and pushed against the first sheet so the beveled edges overlap.
The quality of the jointing is critical, as any future leaks must first make their way through a joint. For added protection, a sealing strip can be stuck over the joint.
Getting the proper radius of bends and corners is critical. Rubber cannot be bent to a sharp crease.
The minimum bend radius is twice the thickness of the rubber. Fabricated items must be built to this requirement.
Once the rubber has been placed it is necessary to use heat to vulcanize it. Vulcanization is the process that chemically creates the long chain molecules that give rubber its properties.
Some rubbers can become vulcanized by themselves at room temperature.
Spark testing for pinholes or thinning is required to prove the lining’s integrity.
Fiberglass
Fiberglass is a composite material consisting of fibers of glass held together with resin.
The fiberglass can be long, continuous rovings, chopped strands or woven mat.
Fabrication can be by winding around a mould or by placing sheets of strand or mat over a mould. The resin is impregnated into the glass fibers as they are laid.
The fibers carry the forces and applied loads and hold the structure together. The resin bonds the glass fibers together and fills the cavities between the fibers.
A fiberglass wall is constructed in layers of glass fiber and resin.
To increase the strength of the wall the fibers in alternate layers are offset to each other. If woven or chopped strand glass sheets are used an overlap of 50 mm between sheets is required for strong connections.
When nozzles are installed additional reinforcing is required around the penetration.
Usually, the wall consists of three different layers – a corrosion barrier of suitable resin about 0.5 mm thick, a backing layer about 2.5 mm thick and a structural layer of suitable thickness to take the working loads.
The corrosion barrier and backing layer can be both on the inside and outside of the structure in corrosive environments.
The resin used in the corrosion barrier is expensive.
To minimize costs a cheaper resin is used in the structural layer. Chemical protection is provided entirely by the outside corrosion barrier.
If the corrosion barrier is breached the resin in the structural layer will fail quickly.
Epoxy linings
Epoxies are resistant to a large range of chemicals including acids and caustics.
They are a two-part coating system consisting of a base and a hardener. Once the components are mixed there is a short period of time to apply the coating before it sets.
Proper surface preparation is critical for successful application of epoxies.
A minimum class 2.5 blast is necessary on metal surfaces and all dirt, greases, oils, fuels and impregnated contaminants must be removed.
Often a high-pressure hot detergent wash is used to first clean the surface followed by garnet blasting to prepare a key for the epoxy. All sharp edges and sharp peaks need to be rounded else the paint ‘runs away’ from the edge or tip and does not cover it to the required depth.
The quality and experience of the applicator is an important requirement when applying an epoxy coating.
It is the applicator who has the responsibility of preparing the surface, applying the primer and placing the epoxy. If the individual steps are not done well the coating system will fail. Surface temperatures and relative humidity affect paint application.
If surface rust reappears on a previously blasted surface it must again be blasted.
To prevent this situation the primer should be applied straight after blasting or within four hours at the latest.
Usually, an epoxy system has a 50 to 75-micron primer and a 100 to 150-micron epoxy coating. If the item is exposed to the sun or weather a third sealing topcoat of 50 to 75 micron is applied to prevent chalking.
Spark testing or a dry film thickness test can be used check the paint thickness.
Rubber lining repairs
A repair to rubber lining involves cutting out the section of rubber containing the hole.
An additional 300 mm of rubber is removed beyond the contaminated area to ensure the edges are sealed to a reliable surface.
Where the corroded surface is damaged it must be repaired. In the case of a steel tank, the area is replaced with a new section of wall and the welds ground flat.
If wall replacement is not viable it can be repaired with appropriate fillers and contoured to suit.
All old adhesives must be removed and the surfaces cleaned and edges of rubber prepared as if new work was being performed.
Fiberglass repairs
Successful fiberglass repair requires the use of resins compatible with the chemical being contained.
If the repair comes in contact with the process it is necessary to apply a corrosion barrier, a backing layer, and a structural layer as if it were a new fabrication. The extra fiberglass layers give structural integrity to the repair that a corrosive barrier applied over the crack alone cannot provide.
It is critical to get a key into the old fiberglass.
This is done using an abrasive disk on a hand drill worked over and around the crack to a distance of 100 – 150 mm either side of the crack. The crack is ground out and the ends rounded.
All evidence of the sheen from the previous surface must be removed prior to applying the new fiberglass.
Prime the surface with the resin and apply the fiberglass matting, overlapping 50- 75 mm either side of the crack.
Wet the matting thoroughly with resin and apply the second layer of glass. Continue in this way till the repair is as thick as the crack was deep. Finally, apply the corrosion barrier over the repair and onto the remaining keyed surface.
Where a fiberglass vessel stores dangerous goods it is advisable to get a qualified fiberglass repairer to do the repair job.
Epoxy paint repairs
Where painted coatings are to be repaired or touched-up the surface must be roughened to make a key for the new paint.
Depending on the extent and severity of the repair it may be necessary to blast the area back to metal. At the very least, all dirt, oil, loose material, and any other contamination must be removed, and the surface wire must be brushed or sandpapered.
The repaint requires applying a primer, an intermediate coat, and a topcoat as per the original specification.
Mike Sondalini – Maintenance Engineer
If you found this interesting, you may like the ebook Bulk Materials Handling Introduction.
Leave a Reply