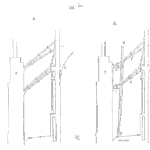
What you will learn from this article.
- Glued plastic pipes must have the joints prepared before gluing.
- Some plastic is joined with glue while others are solvent joined.
- Glued joints do not bond with the plastic but must be ‘hooked’ to it.
- Install thrust brackets if large glued pipes change direction sharply.
Some plastics can be joined with glues or cements. One of the most common of these is PVC. PVC can be either unplasticised (uPVC) or chlorinated (cPVC). Some plastics can be dissolved and chemically bonded together. ABS plastic is such a plastic.
Glued Pipe End Preparation
Glued plastic pipes come as a socket and spigot design. This means that the pipe slips into a recessed fitting. The glue is an adhesive that sits on the plastic surface but does not bond to the plastic. The strength of the joint depends on how much glue sticks to the plastic. The strongest joints are those what have:
- a big surface area of contact between the pipe and the socket
- are mechanically hooked to the plastic
- the glue fully coating both surfaces.
To get excellent glued plastic joints it is necessary to use fine sandpaper to scratch the ends of the pipe and the inside of the socket for a distance equal to the full length of the socket. The fine scratches are made square to the axis around the circumference. When the plastic is sanded the scratches fill up with plastic fines and these must be removed to allow the glue to hook into the scratches. The fines in the scratches are removed with a suitable pre-cleaner available from the glue supplier.
The entire original manufactured surface must be removed by the sanding so that only a rough, matte finish is observable. It is not necessary to make deep scratches into the plastic. In fact if the scratches are too deep they will weaken the pipe by becoming stress raisers that will cause pipe failure. The scratches must be no more than 5% – 10% of the thickness of the pipe wall.
To help the glue coat the surfaces properly, dress the ends of the pipe with a 2 mm (1/16”) long 45o chamfer. This will spread the glue ahead of itself as it moves through the socket and also allow the glue to slide into the fine gap between the pipe and socket wall.
The glue is applied to both the pipe and the socket for a distance equal to the full length of the socket. The pipe end must be cut square to let the pipe slide the furthest distance possible into the socket. While the glue is wet the two parts are pushed home to the end of the socket and held together till the glue sets. Only by getting full surface area contact between socket and pipe can you be sure the joint will hold to its design requirements.
Solvent Joined Piping
ABS plastic joints are cut, roughened and cleaned in the same way as PVC joints. However instead of glue, ABS is joined with a solvent. The solvent dissolves the plastic surfaces in the socket and on the pipe and as it evaporates and dries the plastic molecules intertwine and set together.
The maximum possible contact surface area is necessary and the pipe must be pushed home to the bottom of the socket recess and held in place till the joint sets. Mechanically push the parts together if necessary. Design and built your own clamping devices.
Thrust Supports on Glued Pipes
When large diameter glued plastic pipes are used it is necessary to support the elbows and counter the trust produced by the liquid’s change of direction. When an elbow diverts liquid flow, the change in direction produces a force through the elbow in-line with the flow direction. The elbow will try to move with the liquid. If the force from the liquid is large enough an unsupported pipe joint will fail. Thrust blocks or pipe supports must be installed to absorb the force and hold the pipe in place.
Mike Sondalini – Equipment Longevity Engineer
If you found this interesting, you may like the ebook Process Control Essentials.
Leave a Reply