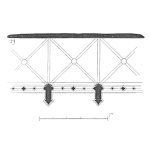
Understanding and Using Human Factors for Human Error Prevention and Mistake Proofing Gets You a Great Safety Advantage
There are many businesses around, even national and international sized companies, who have done an OHS risk assessment for their operations and still have poor workplace safety performance and lousy safety statistics. Clearly they got something seriously wrong when they undertook their operational health and safety (OHS) risk assessment process.
Doing a workplace risk assessment of the operational health and safety risks in your company is a minefield hidden with mistakes and errors that can blow-up in your face! It is vitally important that the people who undertake your workplace safety risk assessment process know how to ensure the OHS risk assessment arrives at correct and cost-effective workplace risk mitigations, especially when they are related to human errors.
Human error is a mistake made by people that results in any unfavourable outcome. It is a normal by-product of workplace activity. The limitations of the human body and human mind, called the human factors, are the foundations of human error. All of us are affected by human factors in diverse ways when doing our jobs and throughout our lives. One could reasonably argue that all failures are the fault of human design because we cannot stop them happening.
For serious reduction in the number of mistakes in your operation you need human factors solutions that prevent the opportunity for your people to make errors.
Human Error Prevention Solutions
The best human error solutions are those designed and built into the way of working. The job design protects against error caused failures. The job design insures that there is only one way to do the task, the right way, and any other way is clearly wrong. Where the same human error in a job happens twice you need to install designed-in error prevention and mistake-proofing solutions.
Human Error Proofing (Poka Yoke)
The goal of mistake-proofing or Poka Yoke is simple: to eliminate mistakes. Originally called ‘fool proofing’” in Japan, and later changed to ‘mistake proofing’ and ‘fail safe-ing’ so employees weren’t offended, poka yoke (pronounced “poh-kah yoh-kay”) translates into English as, to avoid (yokeru) inadvertent errors (poka). The method uses small devices to either detect or prevent work defects occurring.
Existing Methods of Human Error Detection
One branch of human error management strategy detects an error after it is made. The errors are not stopped, but they are detected after they occur. The most common methods to detect existing human error are:
1. Inspect and Check: Test samples against a standard for non-conformance.
2. Work Process Audit: Inspect a work process and get information to better control the process (a feedback loop)
3. Point-of-Origin Inspection: Assess if the input is error-free before using it. Use the Poka Yoke concept of applying low cost devices and visual indicators to spot mistakes as the work progresses.
Existing Methods of Human Error Prevention
The second type of human error management proactively prevents human error. It recognises the effect of human factors and requires designing a system-of-work to remove or reduce the opportunity to make a mistake. Standard Operating Procedures, Fatigue Management, workplace ergonomics and Safety Management are examples of systems and methods to prevent human error.
We have long understood that preventing mistakes is far cheaper than fixing them. The admonishment of ‘An Ounce of Prevention is Worth a Pound of Cure’ is ascribed to Benjamin Franklin (1706-1790). The 1-10-100 Error Cost Rule has long been known in quality management literature. An error corrected during design costs 1 unit, if corrected during construction it is 10 units, and if corrected when the customer has it, the cost is 100 units to fix. The 1-10-100 human error cost rule tells us a human error that progresses through each level costs ten times as much to fix than the prior level.
The 1-10-100 Cost Rule makes it clear that it is best to detect human error early. The misunderstanding people make when they see the 1-10-100 Cost Rule is that a mistake found at data entry is not expensive to fix. They look for errors after an item is in use. They do not count the time and cost that will be lost fixing an error once it is made. They overlook that in an imperfect business system run by humans some errors still get through inspection to cause disaster. They mistakenly believe early error identification is the role of quality management and not their own responsibility. Much better by far is to not make human errors in the first place. Solutions that prevent error bring far greater value and productivity to companies than solutions which identify errors for correction.
LRS Consultants Human Factors Error Prevention Solutions
In order to eliminate mistakes, we need to modify work processes so that it is impossible to make mistakes. With mistake-proofing solutions, many repetitive tasks that depend upon the memory of the worker are built into the work process itself. Mistake-proofing frees the time and minds of the workforce to pursue more creative and value-adding activities. Mistake-proofing also involves a change in the mindset of the organisation. Organisations must establish a mistake-proofing mindset that promotes the belief that it is unacceptable to allow even a small number of product or work defects.
The best part of implementing human error prevention and doing mistake-proofing is that it is never over. Continuous improvement through human factors analysis becomes an essential part in your safety plan to catch new opportunities for error proofing your workplace.
At LRS Consultants we have developed human factors analysis methods that quickly identify the human error risks in your work processes and job tasks. We follow a sound and highly effective job risk assessment methodology for identifying and mitigating workplace errors and mistakes. We develop a focused checklist, as shown in the table below, to spot the potential for misunderstandings, task mistakes and work errors in a job. We then design human factor solutions and Poka Yoke methods that proactively prevent and eliminate the problems in the first place. Solutions are embedded into work activities so people do their work right-first-time.
Our philosophy is that solutions which prevent error bring far greater value and productivity to companies than solutions which identify errors for correction. In our proprietary Plant Wellness Way methodology, work processes are separated into individual tasks. Each task is analysed for its inherent risks, be they safety, mistakes and errors, risk prone behaviours, anthropometric, or potential procedural violations. Once a risk is identified it is addressed with a sound mix of human factor engineering solutions, such as removal of the ‘dirty dozen’ factors that degrade people’s ability to perform effectively and safely, which could lead to errors.
Once human error prevention and mistake-proofing is implemented the learning is not over. Continuous improvement through human factors analysis becomes an essential part in your safety plan to catch new opportunities for error proofing your workplace.
All the best to you,
Mike Sondalini
Lifetime Reliability Solutions HQ
Leave a Reply