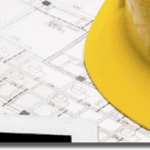
Welcome to part three of my 10-part series of blogs called “Uptime Insights”, where we explore a journey of excellence in maintenance. To stay on top, managers must implement strategies that keep operations performing at high levels. In these articles I will show you how to achieve excellence in maintenance – a critical business process in any capital intensive industry.
Uptime Insights Part Three:
Building an Effective Work Management System
At the core of the maintenance function is work management – a six step process for getting maintenance work done. Without it workforce deployment becomes reactive to emergencies and maintenance costs are high. Work done in those reactive situations is anywhere from 1.5 to 3 times as expensive as work that is fully planned and executed on schedule. In some industries the cost of emergency work is even higher. If you choose excellence, then master the work management process.
The simple cycle of identifying what work must be done, how to do it and what resources are required, when to do it, who to do it, then doing the work and then learning from the experience is what good maintenance departments do. Getting this basic process right drives improved efficiency and opens the door to enhanced effectiveness through a variety of reliability improvement initiatives.
There are planning and budgeting cycles to consider. They range from detailed job plans, through project, shutdown and annual cycles to strategic multi-year and asset life-cycle focus. The basics of planning and scheduling apply to all work. Individual jobs, projects and shutdowns are all managed the same way, the only difference being scale and scope of work. Shutdowns in particular are high cost, intensive activities that occur when revenue generation through production is zero. It’s important to get it right and avoid the temptations to do too much unplanned or poorly planned work in the available time windows. There is a variety of tools and standards to assist the planner so that he can deliver high workforce productivity consistently and keep your costs down.
Mobile workforce management differs from fixed plant. Communications are more challenging and have led to the development of a variety of technologies. Scheduling plays a big role in efficiency due to the need for travel from job to job. Technologies like Global Positioning Systems coupled with Geographic Information Systems help keep mobile workforces productive while meeting the demands of far flung customers. Mobile work crews are autonomous by their nature and carry much of their own support parts and materials with them, but those must be replenished regularly or excessive travel time will result. Planning and scheduling, this time with geographic consideration, is a key to success in managing a mobile workforce.
Work management is the single most important maintenance process. Attention to it provides substantial benefits and leverages your busy workforce.
In our next blog we’ll explore part four of our 10 part series “Uptime Insights: Basic Care Leads to Reliability.”
To learn more visit Conscious Asset where you will find training, workshops, books, and resources.
Related
Uptime: Strategies for Excellence in Maintenance Management (book)
Leave a Reply