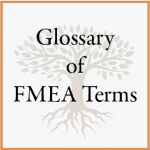
FMEA
Failure Mode and Effects Analysis (FMEA) is a method designed to:• Identify and fully understand potential failure modes and their causes, and the effects of failure on the system or end users, for a given product or process.
- Identify and fully understand potential failure modes and their causes, and the effects of failure on the system or end users, for a given product or process.• Assess the risk associated with the identified failure modes,
- Assess the risk associated with the identified failure modes, effects and causes, and prioritize issues for corrective action.
- Identify and carry out corrective actions to address the most serious concerns.
By definition, FMEA is an engineering analysis done by a cross-functional team of subject matter experts that thoroughly analyzes product designs or manufacturing processes, early in the product development process. Its purpose is to find and correct weaknesses before the product gets into the hands of the customer. The primary objective of an FMEA is to improve the design of the product or process being analyzed.
FMECA
Failure Mode Effects and Criticality Analysis (FMECA) is similar to FMEA, with the added step of a more formal Criticality Analysis (CA). There are two types of CA. The first is Qualitative CA, which uses predefined rating scales for assessing Severity (S) and Occurrence (O) risk, and analyzes the resultant S and O values. The second is Quantitative CA, which requires objective data to support a criticality calculation, involving the expected failures for each item, the mode ratio of unreliability for each potential failure mode, and the probability that a failure of the item under consideration will cause a system failure.
Types of FMEAs
System FMEA is the highest-level analysis of an entire system, made up of various subsystems. The focus is on system-related deficiencies, including system safety, system integration, interfaces or interactions between subsystems or with other systems, interactions with the surrounding environment, human interaction, service, and other issues that could cause the overall system not to work as intended. In System FMEA, the focus is on functions and relationships that are unique to the system as a whole (i.e., do not exist at lower levels). The System level FMEA includes failure modes associated with interfaces and interactions in addition to considering single point failures. Some practitioners separate out human interaction and service into their own respective FMEAs.
Design FMEA focuses on product design, typically at the subsystem or component level. The focus is on design-related deficiencies, with emphasis on improving the design and ensuring product operation is safe and reliable during the useful life of the equipment. The scope of the Design FMEA includes the subsystem or component itself, as well as the interfaces between adjacent components. Design FMEA usually assumes the product will be manufactured according to specifications.
Process FMEA focuses on the manufacturing or assembly process, emphasizing how the manufacturing process can be improved to ensure that a product is built to design requirements in a safe manner, with minimal downtime, scrap and rework. The scope of a Process FMEA can include manufacturing and assembly operations, shipping, incoming parts, transporting of materials, storage, conveyors, tool
maintenance, and labeling. Process FMEAs most often assume the design is sound.
Concept FMEA is a short version of FMEA to aid in selecting optimum concept alternatives or to determine changes to system design specifications. All potential failure modes and effects of each proposed concept are considered before proceeding with actual design.
Reliability-Centered Maintenance (RCM) is an analytical process used to determine preventive maintenance (PM) requirements and identify the need to take other actions that are warranted to ensure safe and cost-effective operations of a system. The core of an RCM project is an FMEA on selected manufacturing or operational equipment, with additional unique actions that ensure the equipment is safe and reliable in service.
Software FMEA applies to software systems in which software controls the hardware. In Software FMEA, the focus is on identifying system weaknesses through software flow charts so that software specifications can be made comprehensive and unambiguous. The goals are to 1) determine whether the software is fault tolerant with respect to hardware failures and 2) identify missing requirements in the system specification.Hazard Analysis is the process of examining a system throughout its life cycle to identify inherent
Hazard Analysis is the process of examining a system throughout its life cycle to identify inherent safety-related risks. The System Hazard Analysis focuses on identifying potential hazards associated with the use of a product, estimating and evaluating the risks, controlling the risks, and monitoring the effectiveness of the controls.
Human Factors FMEA is a type of system FMEA where the focus is on the interaction between users (humans) and equipment. Sometimes this type of FMEA is integrated with the System FMEA in which the scope of the System FMEA includes human interaction.
Service FMEA is a type of system FMEA where the focus is on the installation or service of equipment during operation. Sometimes this type of FMEA is integrated with the System FMEA in which the scope of the System FMEA includes equipment installation and service.
Business Process FMEA focuses on the steps of a business process, and on how to minimize inefficiencies by improving workflow, organizational management, and decision-making. It follows a similar format to a Process FMEA, with the exception that the steps of the business process replace the operations of the manufacturing or assembly process.Failure Modes, Mechanisms and Effects Analysis (FMMEA)
Failure Modes, Mechanisms and Effects Analysis (FMMEA)
FMMEA is a systematic methodology to identify potential failure mechanisms and models for all potential failures modes, and to prioritize failure mechanisms. FMMEA enhances the value of the FMEA and FMECA methods by identifying high-priority failure mechanisms in order to create an action plan to mitigate their effects.
FMEA worksheet definitions
(in sequence of their position in FMEA worksheets)
Item is the focus of the FMEA project. For a System FMEA this is the system itself. For a Design FMEA, this is the subsystem or component under analysis. For a Process FMEA, this is usually one of the specific steps of the manufacturing or assembly process under analysis, as represented by an Operation Description.
Function is what the item or process is intended to do, usually to a given standard of performance or requirement. For Design FMEAs, this is the primary purpose or design intent of the item. For Process FMEAs, this is the primary purpose of the manufacturing or assembly operation; wording should consider “Do this [operation] to this [the part] with this [the tooling]” along with any needed requirement. There may be many functions for each item or operation.
Failure Mode is the manner in which the item or operation fails to meet or deliver the intended function and its requirements. Depending on the definition of failure established by the analysis team, failure modes may include failure to perform a function within defined limits, inadequate or poor performance of the function, intermittent performance of a function, and/or performing an unintended or undesired function. There may be many failure modes for each function.
Effect is the consequence of the failure on the system or end user. For Process FMEAs, the team should consider the effect of the failure at the manufacturing or assembly level, as well as at the system or end user. There can be more than one effect for each failure mode. However, in most applications, the FMEA team will use the most serious of the end effects for the analysis.
Severity is a ranking number associated with the most serious effect for a given failure mode, based on the criteria from a severity scale. It is a relative ranking within the scope of the specific FMEA and is determined without regard to the likelihood of occurrence or detection.
Cause is the specific reason for the failure, preferably found by asking “why” until the root cause is determined. For Design FMEAs, the cause is the design deficiency that results in the failure mode. For Process FMEAs, the cause is the manufacturing or assembly deficiency (or source of variation) that results in the failure mode. In most applications, particularly at the component level, the cause is taken to the level of failure mechanism. By definition, if a cause occurs, the corresponding failure mode occurs. There can be many causes for each failure mode.
Occurrence is a ranking number associated with the likelihood that the failure mode and its associated cause will be present in the item being analyzed. For System and Design FMEAs, the occurrence ranking considers the likelihood of occurrence during the design life of the product. For Process FMEAs the occurrence ranking considers the likelihood of occurrence during production. It is based on the criteria from the corresponding occurrence scale. The occurrence ranking has a relative meaning rather than an absolute value and is determined without regard to the severity or likelihood of detection.
Controls are the methods or actions currently planned, or that are already in place, to reduce or eliminate the risk associated with each potential cause. Controls can be the methods to prevent or detect the cause during product development or actions to detect a problem during service before it becomes catastrophic. There can be many controls for each cause.Prevention-type design controls describe how a cause, failure mode, or effect in the product design is prevented based on current or planned actions; they are intended to reduce the likelihood that the problem will occur, and are used as input to the occurrence ranking.
Prevention-type design controls describe how a cause, failure mode, or effect in the product design is prevented based on current or planned actions; they are intended to reduce the likelihood that the problem will occur, and are used as input to the occurrence ranking.Detection-type design controls describe how a failure mode or cause in the product design is detected, based on current or planned actions, before the product design is released to production, and are used
Detection-type design controls describe how a failure mode or cause in the product design is detected, based on current or planned actions, before the product design is released to production, and are used
as input to the detection ranking. Detection controls are intended to increase the likelihood that the problem will be detected before it reaches the end user.Prevention-type Process Controls describe how a cause, failure mode or effect in the manufacturing or assembly process is prevented, based on current or planned actions. They are intended to reduce the likelihood that the problem will occur, and are used as input to the occurrence ranking.
Prevention-type Process Controls describe how a cause, failure mode or effect in the manufacturing or assembly process is prevented, based on current or planned actions. They are intended to reduce the likelihood that the problem will occur, and are used as input to the occurrence ranking.Detection-type Process Controls describe how a failure mode or cause in the manufacturing or assembly process is detected, based on current or planned action, before the item is shipped from the manufacturing or assembly plant, and are used as an input to the detection ranking.
Detection-type Process Controls describe how a failure mode or cause in the manufacturing or assembly process is detected, based on current or planned action, before the item is shipped from the manufacturing or assembly plant, and are used as an input to the detection ranking.
Detection is a ranking number associated with the best control from the list of detection-type controls, based on the criteria from the detection scale. The detection ranking considers the likelihood of detection of the failure mode/cause, according to defined criteria. Detection is a relative ranking within the scope of the specific FMEA and is determined without regard to the severity or likelihood of occurrence.RPN is a numerical ranking of the risk of each potential failure mode/cause, made up of the arithmetic product of the three elements: severity of the effect,
RPN is a numerical ranking of the risk of each potential failure mode/cause, made up of the arithmetic product of the three elements: severity of the effect, likelihood of occurrence of the cause, and likelihood of detection of the cause.Recommended Actions are the tasks recommended by the FMEA team that can be performed to reduce or eliminate the risk associated with
Recommended Actions are the tasks recommended by the FMEA team that can be performed to reduce or eliminate the risk associated with a potential cause of failure. Recommended Actions should consider the existing controls, the relative importance (prioritization) of the issue, and the cost and effectiveness of the corrective action. There can be many recommended actions for each cause.
Action Taken is the specific action that is implemented to reduce risk to an acceptable level. It should correlate to the recommended action and is assessed as to effectiveness by a revised severity, occurrence, detection ranking, and corresponding revised RPN.
Leave a Reply