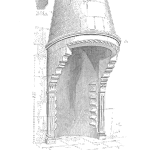
Materials expand or contract with temperature change. Water expands as it freezes, whereas steel contracts as it cools.
This motion can limit the life of your system.
Materials and mechanical engineers include the expected motion into their designs, well the better engineers do.
Even centuries ago, craftsmen used expansion slots or features when attaching wooden table tops to their frames.
The motion due to temperature change will occur and has the potential to create immense strain within your product.
Types of damage caused by thermal cycling
There are a couple of ways a change in temperature can damage your product or system.
Understanding how you material and design risk incurring damage leading to product failure permits you to design and interpret the life testing results appropriately.
Material phase transition
If the change is severe enough that it crosses a material transition point, it may melt, for example.
To avoid this type of damage select materials that will retain the essential material properties for the functioning of the design.
Thermal shock
If the rate of change is too fast (thermal shock) some materials cannot accommodate the change in dimension that occurs on the cold side as the warmer side attempts to catch up, thus may fracture.
As an example, consider what happens when you splash a bucket of hot water on a frozen windshield, it shatters.
If the entire windshield is slowly warmed to the same temperature as the hot water, it will not shatter.
An easy way to crack ceramic capacitors is to touch one edge with a 400°C soldering iron tip.
Heating the circuit board pad and component by touching only the pad allows the capacitor to heat slow enough to avoid the huge thermal stress relieved by cracking the ceramic.
Accumulated cyclic damage
Let’s assume the temperature range for the thermal cycling does experience thermal shock and does not cross material transition points (freezing or melting, for example), thus the bulk material’s motion is relatively elastic, meaning the material retains its properties such as tensile strength, hardness, etc.
If you bend a wire coat hanger wire nothing much appears to happen other than the change in shape.
Yet even a small amount of deflection comes at a price.
The material structure, the bonds that create and hold the shape and properties, changes or accommodates the change in shape.
The material may break chemical bonds, scission polymer changes, alter the local accumulation of elements, create microvoids or cracks, or even accelerate material diffusion across boundaries.
Even well-designed springs incur a small amount of damage with each deformation.
Eventually, the accumulation of small changes leads to a failure.
Embrittlement and hardening are just two of types of changes that may occur within the material as it experiences even small thermal changes.
Coefficient of thermal expansion mismatch
It is rare that we create a product from a single material.
Gold bars are an example of single material product. The functionality is limited compared to an iPhone, for example, yet a solid gold bar will not experience damage due to a mismatch of different coefficient of thermal expansion (CTE) materials.
CTE is a measure of the relative motion due to a change in temperature.
It allows us to estimate the dimension change of a bulk material given a specific change in temperature.
The mismatch parts come into play when two materials are connected in some fashion and have different responses to a temperature change. If they have different CTE values, they will move relative to each other across the attachment points.
This relative motion may cause significant strain, thus often causes damage as the involved materials and attachment accommodate the induced strain.
Consider a table top
Consider the table top attached to a frame and legs.
The wood will expand with temperature (even more so with moisture) and if the table in simply pegged or nailed to the supporting frame, the dimension change across the large table top (wood expands more across the grain than with the grain, by the way, thus for some materials the CTE is different for different orientations) and the relatively smaller frame will more much less.
This relative motion will place a significant strain on the peg or nail making the attachment.
With a very poor design or over time, the relative motion will cause the attaching method to fail.
A well-designed attachment will accommodate the relative motion.
One technique is to make the attachment using a slot, allowing a sliding motion to occur thus avoiding the accumulation of damaging strain.
Railroad tracks and concrete sidewalks include expansion gaps to permit the iron rail or concrete slabs to expand into the gaps without causing buckling, for example.
In both cases, the relative expansion of the metal and concrete is much creating than the surrounding earth.
The design accommodates the difference.
Consider a circuit board
Consider a circuit board with a large integrated circuit (IC).
The silicon-based IC has a CTE of approximately 2 ppm/°C, whereas the CTE of the printed circuit board (PCB) is possibly 21 ppm/°C.
This order of magnitude difference in CTE is the mismatch. As the assembly heats up the PCB will move much more than the relatively unresponsive IC thus creating a strain across the solder joints attaching the IC to the PCB.
Solder responds by deforming when under strain thus retaining the connection.
Solder materials then respond to the strain by relaxing, and to oversimplify a bit, the relaxation process causes damage to the solder.
As the system cycles thermally and continues to relax it accumulates damage and eventually will form a crack which eventually creates an open in the circuit.
Understand the failure mechanism caused by thermal cycling
This very brief introduction to thermal cycling and the ways it can damage your product implies that you must understand the specific failure mechanisms before designing your thermal cycling based life test.
The thermal cycling profile will replicate the same path to failure as seen in normal use.
If you accelerate the life testing by cycling more often than will occur in use, you may inadvertently accelerate different mechanisms than desired.
For example, a nichrome wire based toaster, if cycled quickly by making toast one cycle immediately after the last, will not allow the wire to cool, thus minimizing the stress across the wire attachment.
The result will not correspond to the life behavior during normal home use.
Testing a subsystem when the attachment to the enclosure causes the most CTE mismatch accumulation of strain should include the enclosure.
Testing an IC attachment method, well, should include the solder joint and PCB. When flexing a tube, rod, cable, take care to understand how the damage for that specific material occurs.
Flexing too far or too fast will likely destroy your ability to equate a test cycle to a use cycle in a meaningful manner.
Conclusion
The first, and I would suggest, most important step in crafting a thermal cycling life test is to understand how the damage occurs.
Understanding the failure mechanism permits you to design a test which you can confidently interpret and estimate the expected life during use.
If you currently just toss a few units into a thermal cycling profile, how are you interpreting the results?
Do you have a firm understanding of how the damage occurs in testing and in use, plus understand the relationship between the two?
If not, it’s time to find out and get the most value from your testing.
Do you have an interesting failure mechanism related to thermal cycling? Leave a short description in the comments and help your community learn about the many facets of thermal cycling and its impact on system life.
Related:
Mechanical Systems Reliability Testing (article)
Basic Approaches to Life Testing (article)
Failure Modes and Mechanisms (article)
CTE resulted in my F350 diesel truck running like a bag of hammers. The injector driver module known as a FCIM was bolted to the engine. So a cold Canadian winter to a hot running engine saw a huge temperature swing with the addition of vibration left the end user with broken solder joints. Taking the module apart and re soldering every joint annually was the fix. Buying a new FCIM still left the end user with the same failure mechanism.
Good one Dale, what a pain, manually soldering every joint annually… that is a poor design. Cheers,
Fred
We had a problem with a projector product that was manufactured by a subcontractor. The units would exhibit intermittent failure of cooling fan operation that would then shut down the projector during use.
One of the causes turned out to be a Hall effect sensor used to control the fan operation. The sensor was packaged in a small, plastic (and fragile) SOT type package whose solder joints were being manually reworked (on a portion of the modules) with a soldering iron by the subcontractor. This resulted in one of the sensor package pins moving in the softened plastic during rework, resulting in damage to the wedge wirebond to the pin. During subsequent thermal cycling near the high-intensity (read hot) projector bulb, this damaged wedge bond would become intermittent. Add to this a vibration sensitivity, such that a (intermittent) working fan flown across the country in an engineer’s carry on luggage would be not working when tested after the trip, and a non-working intermittent fan could test out as good after the flight. A very confusing root cause analysis to begin with.
Thermal cycling of the fan modules / Hall effect sensor in a thermal chamber showed intermittently good, intermediate, and open circuit behavior of the sensor over the temperature range, often self-healing itself at room temperature. Banning manual soldering iron rework of the component solved the problem.
Dave
Excellent story David, thanks for sharing.
I’m curious how did you discover the damaged wedge wirebondss?
Cheers,
Fred
Hello Fred,
It seems like we can capture more failure mechanisms by high temperature (arrhenius method). If we have limited time, is it more effective to develop the plan of high temperature test instead of thermal cycling?
Thanks!
Hi Gulin, high temperature stress does cause more failure mechanisms to accelerate than other stresses, for electronics especially. Yet, it really depends on the use environment and the stresses most likely to cause failures in the field. Use FMEA and similar risk assessment tools to determine what is likely to fail, the develop your testing to determine the probability of failure over a time period of interest.
Cheers,
Fred
Thanks Fred!
Cheers,
Gulin
Please guide me; can we apply certain number of thermal cycles (e.g. 6 cycles) on some electronic unit in time breaks, for example, 3 in one day and other 3 on the next day. or we have to apply in consecutive form. I would appreciate if you refer some a standard if its is to be applied in consecutive state.
Hi Dr Tasleem,
I’m not sure I understand the question – generally, we count the number of cycles to failure for each failure, of course this may be related to time since the start of the test.
Please explain a bit more about your situation and your question.
Cheers,
Fred