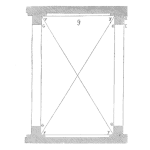
At SDMyers, we can’t stress enough the importance of safety when testing high-voltage electric-power equipment. Our partners at IRISS share our passion for the safety of maintenance workers in the field, including our own mobile diagnostic technicians. We hope that this guest blog from them is educational. If you find value in it, please leave us a comment. And, if you enjoyed this article, then here’s information on the safest way to obtain oil samples from cabinet transformers without de-energizing them.
Be safe—never make contact on energized equipment with an ultrasound device.
By Guest Blogger Drew Walts, training manager, IRISS Inc.
(This blog post was contributed by IRISS Inc., a global provider of electrical and mechanical asset management solutions that increase safety and reliability, decrease costs, eliminate human error, and prevent injuries and fatalities in the inspection and maintenance process.)
This was usually dad’s go-to statement when talking to one of his guys on the jobsite when he did something unsafe or risky. Today, this adage seems even more relevant when it comes to electrical inspections with ultrasound devices. Just because you have a contact module in your kit doesn’t mean you should use it to contact energized gear when you hear something with your airborne module from the seam, vented opening, or ultrasound port.
Hierarchy of Controls
If we look to the Hierarchy of Controls from NFPA 70E, the first step is the Elimination of the hazard by de-energization of the equipment. However, condition-based maintenance (CBM) inspections like ultrasound require the equipment to be energized; so, elimination isn’t possible.
The second stage is Substitution, or what we at IRISS refer to as “Safety by Design.” Can we redesign the work task and/or the equipment in such a way as to eliminate the hazard without introducing any other new hazards? The use of infrared windows and ultrasound ports is the best method for Substitution of the hazard since infrared and ultrasound have become a go-to test method for the detection of electrical fault conditions of closed panel-energized assets.
Without the substitution—Safety by Design—devices in place, it can be next to impossible to test using infrared cameras or ultrasound devices. With the enclosure panels in place the inspector may still be able to use an airborne module and trace the seams or air vents to listen for ultrasound anomalies. Remember that most electrical equipment should have no discernible noise emanating in the ultrasound spectrum. In addition, the challenge with this “scanning the seam” method is that diffraction of the signal can cause issues with the signal’s amplitude being increased as it bounces out of the seam and increases the decibels. Decibels should never be used as a trendable value for determining required intervention action on electrical assets. The CBM Analyst should capture a sound wave of the anomaly so it can be analyzed in a Spectrum Analysis Software Platform. Sound wave analysis of the anomaly is the only way to truly determine what fault condition is present in the equipment.
When an ultrasound anomaly is detected around the seams or vent of the asset, it should be tested further. However, without having IR windows or ultrasound ports there is no way to safely perform these tests while energized. So, the gear will need to be de-energized and then opened to look for visual indications of corona, treeing or tracking, or arcing. Once these visual indications are found, corrective action can be determined, which may include cleaning, component replacement, tightening or re-cabling.
The “last resort” requires more training, more planning, more knowledge.
The inspector should almost never perform an open panel-energized inspection using ultrasound devices or infrared cameras, as this would be deemed a last resort per the Hierarchy of Controls. If this is deemed the ONLY way to perform the work, then there are several requirements that must be in place first:
- Personnel must have the appropriate training.
- A job safety plan must have been created (including planning for human error).
- Proper PPE should be worn.
- Proper boundaries should be put up to isolate the test area of non-essential personnel.
If the equipment’s arc flash rating has been gauged to be one that PPE can be worn to perform energized open inspections, there still are a few things that will need to be heeded:
- The CBM analyst should never wear the headphones for their ultrasound device under the hood of the arc flash suit. The analyst must hold the headphones off to the side by their ear on the exterior of the suit.
- Even when wearing PPE, they also should never break the plane of the opening of the gear. Restricted approach boundaries, as defined in the NFPA 70E tables [130.4(D)], should always be maintained.
- They should neveruse the contact module or even rubber or plastic focusing probes or long-range horns to touch energized equipment to locate or listen to the anomaly. It only takes one time for it to be your last time ever.
So, a CBM analyst should only very rarely open gear while it is still energized to perform an airborne ultrasound inspection. It has been brought to our attention that there are instances where a CBM technician has swapped out their airborne module and used their contact module to make physical contact with open energized gear. To reiterate: This is unsafe and should never happen under any circumstances.
We cannot stress the importance of safety for electrical personnel enough. We created IR windows and ultrasound ports to help protect those doing electrical inspection by minimizing the risk of this CBM data collection task. Being able to see the equipment with your eyes and with an IR camera affords you a safer view of what’s occurring inside. Ultrasound ports give you the best sound quality of any possible electrical anomaly without the effects of antagonistic ultrasound, diffraction of signal, or inability to achieve the critical angle of the anomaly.
About IRISS Inc.
IRISS Inc. is the global provider of electrical and mechanical asset management solutions that increase safety and reliability, while decreasing costs, human error, and injuries/fatalities in the inspection and maintenance process. Through unmatched research and development, we harness advanced technology to design and manufacture reliable infrared, ultrasound, intelligent asset management, and wireless temperature monitoring solutions.
Leave a Reply