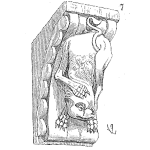
I’ve spoken with a few of my customers over the past couple of weeks, one who happens to be in the food business was cranking and working overtime to meet the increased demand that resulted from folks stocking their homes, the other two were labeled non-essential and were preparing to shut down for the foreseeable future.
I asked the two that were preparing to shutdown what they planned to work on during the shutdown and was met with silence. One in fact replied “we have been so tied up trying to figure out how we’re going to deal with this that we haven’t thought about what we could work on. People are in shock. They want to know how long we think this will last. They want to know if they will be paid or if they’re going to be laid off. As it stands right now, no one is real clear on what the future holds.”
I then asked him a question I hoped would bring him back to reality. Do you think the company will close its door forever?
He replied, “No, of course not! We’ll get through this at some point and be right back at it. I just hope we don’t loose any of our good people to other companies who are up and running. This would be a heck of a time to hire some of those top tradespeople who are sitting home.”
I asked him what could you and others, start working on at home using over tools like Skype or Go To Meeting that would be productive for your company?
Our 10-minute discussion created a list I thought several other companies could use. Understand, this is the list I jotted down as we brainstormed, its not in order of importance.
- Make your CMMS equipment hierarchy ISO 14224 compliant and detailed to the component level
- Perform a criticality analysis on our equipment to asset or machine level using a ranking system with a number range that is the square root of the number of assets at our site
- Do some data mining to find out where we are spending the most time and money
- Perform a Root Cause Analysis, RCM or FMEA on our bad actors
- Review our PM’s – Eliminate those that are not applicable and effective, rewrite those that are vague or subjective
- Perform a virtual RCM analysis on a critical asset that not performing as expected
- Review your spare parts inventory. Look closely at parts that haven’t turned, parts with a high turn rate, parts tied to equipment/assets that no longer exist, and obsolete parts.
- Develop a check list for start-up. In what order should we restart? Who should be working when we start up? What are some of the things we should be monitoring and doing as we start up?
- Make a list of any potential hazards we might expect to see from having our equipment down for an extended period. Make a list of expected hazards we might see in restarting.
As always, I’m interested in your thoughts. This list was created from a short conversation so I’m sure may of you will have some fantastic suggestions!
Douglas Plucknette is the President of Reliability Solutions Inc. and creator of RCM Blitz™. The author of Reliability Centered Maintenance using RCM Blitz™ and Clean, Green and Reliable a best-selling book on how to reduce energy consumption in manufacturing plants through equipment reliability. Doug has published over 100 articles on Maintenance & Reliability and has been a featured Speaker as well as Keynote Speaker at a countless number of conferences around the world.
Leave a Reply