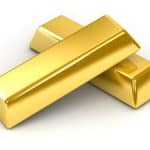
Unlock the Potential of Your CMMS by Accessing the Data Within
If you have properly selected and implemented your CMMS, you have the ability to truly make significant improvements in your operation. This is made a reality by using the data within the CMMS to make data driven decisions instead of intuition or feelings. This ensures the business resources are spent on the most important and strategic issues for the business.
In order to leverage the data within your CMMS, you have to ensure the data can be captured and reported easily. This is usually done during the implementation phase.
Why Setting up the Data Structure is So Important
Data standards to ensure that the equipment and materials are categorized, making the reporting easier, but it is not the only piece of organizing the data. Data must be structured in a way that facilitates easy entry, reporting, and analysis.
Without the structure, the information is just unorganized data in the CMMS that has no meaning. The old saying goes “Garbage in, garbage out”, and it holds true without the standards and the structure. So how does one structure the data in a CMMS for maximum benefit to the business?
Failure Reporting and Corrective Action System
All failures need to be recorded in a structured way to facilitate the collection all the required data for analysis and improvement. The framework that is commonly used is the FRACAS or Failure Reporting & Corrective Action System.
In this framework all failures need specific data, which could follow the recommendations from ISO 14224, or follow what Mr. Paul Barringer states as required;
- Equipment ID
- Ages to Failure (time the equipment or component was in operation)
- Censored Failures (Removal of equipment before failure due to PMs, overhauls, or restoration)
- Reasons for the removal (this must be detailed in terms of the cause, not broke and fixed)
- Date, time, operating condition
This information is the minimum information required and you can require more data points for various purposes. Just remember, if you are collecting it, be sure to use it.
Ideally, the failure data is codified in the CMMS, making entry easy. If you are able to codify the failure data, make it simple and make it relevant to the equipment. For example, only failure modes and causes related to a pump should be available for a pump. Lastly, if possible, try to align the failure coding with the data from your RCM work. This will connect the RCM to the failure recording and make the whole program come to life.
Extracting the Gold from the CMMS
With all the right data going into the CMMS, we can finally start to extract information and make sustainable improvements in the operation.
Start by using a Pareto to identify the top candidates for analysis. The Pareto will identify the 20% of equipment causing 80% of the downtime in the operation.
With the top equipment identified, you need to determine which equipment is costing the most, and not just in terms of downtime hours, but also lost production, overtime, and expediting of parts. The total cost of the downtime needs to be considered.
With the final piece of equipment selected, start to use Reliability Engineering tools such as Root Cause Analysis, Fault Tree Analysis, or Weibull Analysis to use the data we have been collecting to drive down to the root cause of the issue. With the failure data collected, the cause can be identified, along with the conditions around the failure.
The conditions may be that the majority of the failures occur during start-up which tells us that start-up procedures and interlocks will address the majority of the failures. The rest of the failures can be analyzed using the Weibull analysis and determined that the failure is in fact related to age. This will guide changes to the maintenance program. These are the corrective actions that will make a difference for the business.
It is ideal to then repeat the process, constantly identifying and eliminating the issues that plague the business. However, it is critical that the return on investment of the corrective actions is tracked and reported to prove the improvements. A Crow-AMSAA analysis will assist with this.
With the right data in the CMMS, you can easily start to extract the data and utilize the powerful tools available to you. So what is stopping you from using the data you have or to start collecting the data you need?
Remember, to find success, you must first solve the problem, then achieve the implementation of the solution, and finally sustain winning results.
I’m James Kovacevic
HIGH PERFORMANCE RELIABILITY
Solve, Achieve, Sustain
Follow @HPReliability
References
ISO 14224:2006, Petroleum, petrochemical and natural gas industries – Collection and exchange of reliability and maintenance data for equipment
FRACAS – Paul Barringer
Leave a Reply