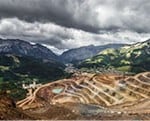
Most of us would agree that there is a new global economy being forged right now in the manufacturing sector.
Inevitably, this translates to a renewed focus on transferring more business value to the customer. Central to this will be linking RCM (Reliability Centered Maintenance) facilitation with effective maintenance program implementations.
In short, the difference between what we, as RCM Facilitators, have been doing in the past and what we will be doing from now on is: a strong emphasis on what tactics are required in order to achieve the failure management strategies an RCM Team defines.
That is, we will conduct the decisions phase of the analysis somewhat differently. (i.e. The 3rd pass through when walking-the-dog in an RCM analysis)
On a consensus basis, the Facilitator leads the RCM Team to create well-articulated PM tasks in a simple two-step process.
Note that the process always considers each of the three possible types of proactive maintenance tasks (Condition-Based Maintenance – CBM, Scheduled Restoration/Discard – SR/SD, or Detective/Failure-Finding Interval – FFI) :
Step 1: A physical asset health Indicator is described with an NWAC state:
– Normal state (a description of asset status where there is little or no degradation in performance),
– Warning state (a description of asset status where there is some degradation in performance but perhaps insufficient to warrant an intervention),
– Alarm state (a description of asset status where there is sufficient degradation in performance to warrant an intervention either immediately OR at the next available downturn) and,
– Critical state (a description of asset status where there is a significant degradation in performance to warrant an immediate intervention).
Step 2: Identify which NWAC state triggers an actionable alarm:
The other is a brief description (i.e. 20 to 30 words) articulating which NWAC state in Step 1 triggers an actionable alarm that constitutes what remedial action if any, and what is necessary to return the asset to like-new condition.
Here’s an example of this for a CBM type task:
Visually inspect the condition of the hydraulic hose for signs of blistering, cracks, leakage or other physical damage.
When visible cracks are found, Maintenance Mechanic replaces hose H1004.b as per SOP #MT501-1(a) at next available downturn. Repair time = 30 mins. Spare hose (SAE 100R2 Type AT) needed.
N – Normal (Not brittle, not blistered, not cracked, not leaking – no action)
W – Warning (Brittle, blistered – Continue to monitor hose condition)
A – Alarm (Cracks found – schedule hose replacement at next available downturn)
C – Critical (Leaks found – contact Maintenance for immediate hose replacement)
If done correctly, the effort/time required describing each NWAC in Step 1 and the corrective task in Step 2 should be only slightly more than previously.
How can this be?
This is because we are already capturing the NWAC information when we describe the P to F (or life) ‘evidence’ that leads to functional failure in the failure effect during the second pass through ‘walking-the-dog’.
Provided the Subject Matter Experts (SMEs) are reasonably familiar with the assets being analyzed, they will be able to quickly & easily assign each NWAC from their asset management experience and knowledge.
Furthermore, the corrective task should be easy to write up because seasoned maintainers (i.e. The subject matter experts or someone they know) have often ‘lived’ the pain of repairing the equipment failure. As such, the SMEs are more than willing to share their experiences with the group.
As Reliability Centered Maintenance Facilitators, we should conduct our analyses with maintenance program implementation clearly being our end objective.
After all, the complete business value proposition (i.e. the promise of RCM) can only be realized if, after all, we do, the agreed-to Proactive tasks are dove-tailed into the customer’s day-to-day work management process.
Even if it means compromising our number of failure modes per hour metric, the end justifies the means.
Leave a Reply