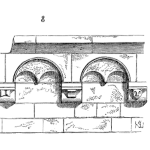
A machine run-off, refers to the process of testing and adjusting a new or modified machine or piece of equipment before it is put into regular use. When a run-off is performed prior to shipping to the customer, it is called a Factory Acceptance Test (FAT), and when it is performed after installation at the customer’s facility it is called a Site Acceptance Test (SAT).
Both types of machine run-offs are common with large, complex, and/or expensive equipment. And both have the same goal of ensuring the equipment is safe and reliable, and meets the customer’s requirements and functional criteria before it is launched into production where repairs and corrections become much more expensive. The SAT is largely a repeat of the FAT expect it additionally verifies that no damage was incurred during shipment and that the unit is correctly installed.
Run offs typically involve cycling the machine through a series of tests to ensure that it is functioning properly and that any issues or problems have been identified and addressed.
The SAT and FAT, despite their singular nouns, are comprised multiple tests to verify different performance aspects of the machine. A common first step in an acceptance test is a visual inspection of the components of the machine as compared to the purchase order and engineering specifications. This includes:
- All components and accessories.
- Correct input power connection (e.g. electrical, pneumatic, hydraulic, etc.)
- Safety curtains, static guarding, interlocks, etc.
- Custom or perishable tooling
- Documentation such as operating manuals, prints, electrical schematics, and spare parts list
Next is a start up of the equipment. Depending on the complexity of the equipment, this and subsequent steps may be interleaved with training for the customer’s representative. Helpful observations during start-up may include correct air or hydraulic pressure, unusual noise or vibrations, and the correct functioning of control screens.
Then after the initial start-up but before any parts are manufactured, FAT’s include a safety validation test. This is where all light curtains are intentionally breached, e-stop buttons are pressed, 2-hand controls and similar safety devices are intentionally activated to determine if they are correctly functioning. A failure at this step results in a failure of the entire acceptance test.
Once the equipment is verified to operate safely, factory technicians will begin a production run of the customers parts. In the case of a CNC lathe for instance, technicians will set up the machine with the customer’s raw inputs and cut their shapes to their specification. This will give both factory and customer representative the opportunity to observe the machine in motion. These sessions may be video recorded for future reference.
At this point, a second test may take place: functional performance. Commonly machines are specified with a minimum production rate. This may include a cycle time such as “less than 3 seconds per part” or a longer-term rate such as “minimum 3,500 parts in a 4-hour run”. This latter test is designed to account for perishable tooling changes, minor process adjustments, the resolution of machine faults, and similar. By conducting a longer functional test, customers may observe certain types of shifts or failures that are less likely to occur in shorter events.
A third area of evaluation is quality performance. Once the machine is functioning at its production rate, a quality representative may select samples for process capability analysis. In short, a process capability study is an analytical comparison of the customer’s specification range for a given part characteristic (typically a critical-to-quality characteristic) and a statistical-derived estimation of the process range for that characteristic based on a sample of parts produced by the machine.
Common process capability studies for machine run-offs include:
- Cpk – An analysis of the potential quality performance of the machine performed by comparing the average variation of small subgroups over time to the customer’s specifications.
- Ppk – An analysis of the actual quality performance of the machine performed by comparing the total variation of parts it produces over time to the customer’s specifications.
- Cmk – An analysis of a narrow range of sequentially produced parts to find the machine’s minimum inherent quality performance as compared to the customer’s specifications.
And for machines with integrated measurement systems, another type of statistical analysis called a Measurement Systems Analysis may be performed as well.
A well-conducted machine run-off will also include the documentation of all significant findings, both positive and negative, including a checklist of action items that need completed prior to full acceptance by the customer.
And while not a formal part of FAT’s and SAT’s, they are often a good opportunity for the formal training of machine operators, set-up technicians, engineers, and maintenance personnel.
FAT’s and SAT’s are beneficial not just for the equipment buyer, but for the manufacturer as well. A well-planned and executed acceptance test can help both parties understand that the contractual requirements have been met, and that the equipment can operate safely and reliably in the customer’s facility. Identifying and correcting even small issues discovered during acceptance testing can save untold time, onsite repair costs, and the frustration of not meeting the expectations of the project.
Leave a Reply