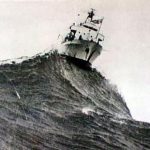
Stress Margin is an interesting topic because our gut reaction is “more is better.” But more isn’t better. The key is figuring out “How much and where?” this is where the attention should be paid.
Too much stress margin can end the project the same way making material too thick will turn a plane into nothing more than a crappy diner with too much security. It’s the correct margin that is needed. How do we select the correct margin?
It is a matter of identifying how much risk to the expected variability is acceptable. If there was no variability in use, environment, or manufacturing we wouldn’t need any. The first step to accomplishing this is accessing how much variability can be expected in all three of these categories. The variability will need to be compensated for by the design margin to ensure that the overlap of stress and strength is an acceptable percentage.
The overlap of these two distributions is where product failure occurs. To minimize the overlap two things can be done. The first is tighten the distributions, reduction of standard deviation, the second is move the distributions farther from each other, distance between the means.
To reduce the standard deviation from the mean improved manufacturing processes and quality control will be put in process. This ensures more of the product in the field is equivalent or better than the design (nominal) value. Ensuring the reliability program had the right hooks to support an improved manufacturing and quality inspection process is key.
This can be done by ensuring HALT testing considers the opportunities to use HASS in production. Accelerated Life Test (ALT) identifies multiple wear-out failure modes, not just the first under nominal conditions. That second or third may quickly become the primary wear-out failure mode under certain use or environment variabilities.
The second way to increase margin is to identify measure and adjust the distance between the nominal stress and design parameters. The “miss” here is usually “identify”. The risk assessment process needs to directly evaluate the areas of greatest risk to variability. There are multiple versions of this chart for a single product. The stress may be an axial load on a bearing or the thermal stress on a PCB. They all exist and there are too many to evaluate. Selecting the correct ones to measure and dial in is the key to using program resource correctly and ensuring the team doesn’t get a surprise when the highly variable world tests the product.
Margin on stress is the definition of the”robustness”. But robustness on the right parameters is what makes the difference between an over designed product and a truly robust product
-Adam
Leave a Reply