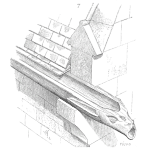
The materials used in new equipment can pose a design risk. But what makes a material a design risk? And how is de-risking achieved for metallic and nonmetallic materials?
To satisfy design requirements for loading, corrosion resistance, and manufacturability, materials properties must be controlled. Design risk is high when material properties are not controlled and materials are not selected using best practices. And as stated in Equipment Risk, material stability is also necessary for long service life, meaning that mechanical and physical property response to elevated temperature and corrosive media is predictable or reasonably estimated. Thus, controls for material properties and selection are the basis of de-risking.
Metallic materials
- Well-written OEM materials specifications control chemistries, mechanical and physical properties, and tests, as well as Quality Assurance (QA) and mill requirements.
- Materials characterization studies may be required for critical applications such as long service life or high-pressure high temperature (HPHT).

Non-metallic materials
- Well-written OEM material specifications control compound chemistry, mechanical and physical properties, processing parameters, ASTM property evaluation, and more.
- Arrhenius- based properties degradation studies may be required for critical applications such as long service life or HPHT.
Materials Selection
- ANSI/NACE MR0175/ISO 15156-2015 is one industry standard for metallic materials selection.
- Some API product standards, such as API 6A, contain sections on materials selection.
- Well-written OEM guidelines for materials selection are based on industry standards and best practices.
TRUTH: Control of material properties and selection criteria minimize design risk.
This is the 3rd in a series of 10 articles on critical equipment design for offshore completions.
very informative article.
Thanks for your feedback!