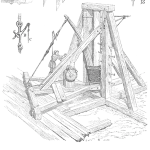
Originally published in the ASQ Reliability Review, Vol. 12, No 3, June 1992
Insert these pages into your copy of MIL-HDBK-217. The boldface text is changed to MIL-HDBK-217E [1], section 5.2, on parts count reliability prediction. The changes explain how to use “Paretos,” proportions of parts failing in the field, to compute a reality factor that makes predicted Paretos match field Paretos. You can use field Paretos to calibrate predictions for new equipment. You probably have field Paretos on related parts used in your other equipment, which is now in the field. Remember, the field determines reliability.
HORROR STORY
A famous computer company congratulated itself that field failure rates agreed with predictions. Unfortunately, their failure rate predictions were the lower 5% confidence limits. (The field failure rate approximates the inverse of the true MTBF under some conditions.)
FREE OFFER!
If the formula for the reality factor seems daunting, send for a spreadsheet that does the calculation. Send your field Paretos, parts count and reliability predictions for the parts on the equipment. I’ll compute the reality factors and send them back. Plug them into your MIL-HDBK-217 predictions for new equipment.
I gave away spreadsheets to do MIL-HDBK-217 computations [2]. Look them up or ask me for them, and you could add the reality factors to those spreadsheets.
Send DOS or Macintosh, spreadsheet, dBASE or text format. Send by modem, fax, Internet if you’re in a hurry.
CONCLUSIONS
Don’t cringe when people ask why equipment’s field failure rate is so much higher than your prediction. Don’t blame vendors for component Paretos that have no relation to predicted Paretos. Use the MIL-HDBK-217G (George) parts count reliability prediction method to improve your predictions and calibrate failure rates to agree with reality.
MIL-HDBK-217G (George)
5.2 Parts Count Reliability Prediction with Reality Factors. This prediction method is applicable during bid proposal and early design phases. The information needed to apply the method is (1) generic part types (including complexity for microelectronics) and quantities, (2) part quality levels, (3) equipment environment, and (4) field failure proportions (aka Paretos), if any. The general expression for equipment failure rate with this method is
$$ \displaystyle \lambda_{EQUIP}=\sum_{i=1}^{n}N_{i}\left(\lambda_{G}\pi_{Q}\pi_{R}\right)_{i} $$ (1)for a given equipment where:
λEQUIP= total equipment failure rate (failures/106 hr.)
λG = generic failure rate for the i-th generic part (failures/106 hr.)
πQ = quality factor for the i-th generic part
πR = reality factor for the i-th generic part’s field failure experience
Ni = quantity of the i-th generic part
n = number of generic part categories.
The above expression applies if the entire equipment is being used in one environment, like the environment previously experienced. If the equipment comprises several units operating in different environments (such as avionics with units in airborne inhabited (AI) an uninhabited (AU) environments), then equation (1) should be applied to the portions of the equipment in each environment. These “environment-equipment” failure rates should be added to determine total equipment failure rate. Environmental symbols are defined in Table 5.1.1-3, page 5.2.2-3 through 5.1.1-6.
The quality factors to be used with each part are shown with the applicable lG tables and are not necessarily the same values that are used in Section 5.1, Part Stress Analysis. Multi-quality levels are presented for microelectronics, discrete semiconductors, and for established reliability (ER) resistors and capacitors. The λG values for the remaining parts apply providing that the parts are procured in accordance with the applicable parts specifications and, for these parts, λG = 1. Microelectronic devices have an additional multiplying factor, πL (learning factor) as defined in Table 5.2-24.
The parts’ reality factors come from field failure experience quantified as “Paretos.” Paretos are the fractions of equipment failures caused by each part. Compute them from field failure experience, if any.
5.2-1
Compute the ratio of each part’s failure fraction and its predicted failure fraction, for the equipment observed in the field,
$$ \displaystyle N_{i}\left(\lambda_{G}\pi_{Q}\right)_{i}/\lambda_{EQUIP} $$ (2)If the ratio exceeds the observed fraction of equipment failures, P(i) , then πR = 1. If the ratio is less than P(i) , then reorder the parts so the parts with Pareto greater than predicted failure fraction, on the equipment observed in the field, is greater than 1. Let k denote the number of parts for which this is true, and let n denote the total number of parts on the equipment observed in the field, k < n.
The reality factor for the i-th part type is
$$ \displaystyle \pi_{R}=\left[A^{-1}b\right]_{i}/\left(\lambda_{G}\pi_{Q}\right)_{i} $$where [A-1 b]i is the i-th element of the vector [A-1 b], A is the matrix
1-P(1) | -P(1) | Etc. | -P(1) |
-P(2) | 1-P(2) | Etc. | -P(2) |
-P(3) | -P(3) | Etc. | -P(3) |
Etc. | Etc. | Etc. | Etc. |
-P(k) | -P(k) | -P(k) | 1-P(k) |
and b is the vector
P(1) |
P(2) |
P(3) |
Etc. |
P(k) |
times ∑(λG πQ)i where the sum is from i=k+1 to n, the number of parts’ Paretos. Note that the ratio Ni (λG πQ)i/λEQUIP is the ratio computed for the equipment on which the field experience is observed, not on the equipment whose reliability is to be predicted! The reality factor adjusts the equipment reliability prediction by adjusting some parts’ failure fractions upward, in the direction of field failure experience. Naturally this increases the equipment reliability prediction.
REFERENCES
1. MIL-HDBK-217E, “Reliability Prediction of Electronic Equipment,” U. S. Department of Defense, Washington, DC, 27 Oct. 1986.
2. George, L. L. “Reliability Analysis Templates,” Reliability Review, June 1989.
About the Author
Larry has a Ph. D. in industrial engineering and operations research. He’s past Division Director of the IIE QC&RE Division, editor of the Software Entrepreneurs’ Forum newsletter and Reliability Review reviewer. He taught industrial engineering, management science and statistics for ten years, worked for Lawrence Livermore National Laboratory for eleven years, Apple Computer for two years, EPRI for one year, Abbott Labs for two years, and Triad Systems for three years. Contact Larry at 1573 Roselli Drive, Livermore, CA 94551-2446, 925 447 4969, pstlarry@home.com.
I apologize for violating the ASQ copyright, although ASQ no longer publishes Reliability Review. I didn’t intend to do so.
The next Accendo Weekly Update #465 contains a more elaborate explanation of MIL-HDBK-217G with an example.
My address and email have changed to pstlarry@yahoo.com