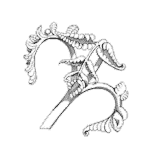
Moving slurries about. Slurry is solid particles in a liquid. Concentration can vary from mostly liquid to mostly solid. Slurries are usually transported through pipe work using pumps, pressurised gas or steam. Different concentrations and different particulate produce different flow characteristics. Successful slurry transport requires knowledge of the particulate, its transport behaviour in the liquid at different concentrations and speeds, the nature and friction effects of the pipe work system and selection of the right motive method for the application. This article provides information for transporting slurries of up to 60% solids concentration.
Keywords: Dense phase transport, rheology, viscosity.
Pumps or pressurised blow tanks are usually used to move slurry. If a pump is used it is best put below the outlet nozzle of the supply tank. With a blow tank either a dip pipe goes into a sump at the bottom of the tank or the outlet nozzle is at the lowest point of the tank. The surface of the slurry in the blow tank is pressurised to force it out the vessel and through the pipe work.
Because slurry is solid particles in liquid the particles will want to settle out. The particles are pulled down by gravity and will follow the direction of gravity. The only mechanism available to keep the particles suspended while moving through the pipe is turbulence within the pipe.
In slurries where the concentration of particles are so high that there is not enough liquid movement available to suspend them, or the particles are to big, it becomes necessary to use equipment that mechanically forces the product through the piping.
Requirements when moving slurry
The entrance flow into the motive device is important. In the case of a pump the suction must always run full to be sure the slurry will be drawn through to the pump. Bubbles, froth, slugs of gas or cavitation will allow the slurry to settle out and block the pipe. If gas or froth enters the pump the impeller spins in empty space. If too much gas or froth is present suction is lost. Insure that only slurry is in the suction port at the pump. A vent pipe can be fitted at the pump suction and vented back to the top of the supply tank.
Flow velocities are critical to particulate movement. The liquid must move fast enough to pick up the particles and move them forward. The heavier the particles the faster the flow of flushing liquid. It maybe necessary to conduct lab trials to determine the slowest flow velocity that prevents particle dropout. Never go below that velocity else you will get blocked pipes! Size pipes to insure flow velocities stay above the dropout velocity.
Flow pathways need to be smooth and unobstructed to minimise friction losses. Select valves that are straight- through designs and that have internal contours causing little effect on flow and pressure loss. Use bends in preference to elbows when changing pipe direction. Select instrumentation that does not protrude into the flow path.
Pressure losses in slurry flows are significantly higher than if the liquid were flowing alone. It is necessary to calculate the losses accurately so that the proper sized motive equipment and piping is installed. In the process of designing and determining the equipment to use it is wise to assume that there will be dropout incidences (power loss is a typical situation). Determine how the particulate will be re- entrained and design the method into the process/plant.
Issues to consider when moving a slurry
Settlement: It is critical to prevent settlement in the pipe. If it does occur there are few options to try. If the pipe is not totally blocked it may be possible to force high-speed liquid across the top of the settled particles and try entraining the top layer of sediment. An alternative is to introduce compressed gas (such as air if it is safe to do so) into the liquid flow to create maximum turbulence across the top of the sediment. With liquid flowing quickly across the top of the sediment it is sometimes possible to mechanically hammer the outside of the pipe and bounce the particulate up into the flow stream. In the case of crystal slurry is it possible to dissolve the crystal into the liquor by using hot liquid or liquid with a low concentration of product?
Mechanical cleaning is another possibility. Devices such as a plumber’s screwing ‘pipe snake’ can cut the particulate up and drag it out. The last resort is to open up the pipe section- by-section and clean each out.
Wear: The high flow velocities attained through pipes and equipment and/or the hardness and shape of the particulate can cause extremely high wear rates. High wear occurs where the flow changes direction and/or where localised velocities are extreme.
Typically inside pumps the impeller walls and vanes see high local velocities and speed changes. Often an open impeller is used with slurries. In an open impeller there is no wall on the inlet side to the impeller. Also the impeller may have fewer but thicker and deeper vanes. This provides more sacrificial material to wear away and larger spaces between the vanes to more easily handle lumps. With an open impeller the pump volute on the open side experiences high flows across it will wear as the impeller spins. Usually changeable volute liners are installed in the pump or it is made of hard, wear resistant material.
Pipe walls can wear away. If the particulate mostly slides along the bottom of the pipe it will cut a groove into the pipe wall. Where the flow changes direction the impact will gouge away the pipe. Some options to address wear are to:
- Provide plenty of sacrificial wall material or a sacrificial liner,
- On bends use bulbous elbows with a cavity that let product build-up to form a solid surface over which the flow rubs as it turns. Deflector plates surfaced with hard- face weld can be fabricated and mounted into the flow path.
- Change the material to one harder than the particulate (possibly use hard stainless steels, cast Nihard steels or Bisalloy steels instead of carbon steels),
- Change the material to one that absorbs the impact and bounces back (rubber lining and soft urethane are examples),
- Line the pipe with an extremely hard surface such as ceramic or trowel on coating designed for impact and wear.
- Use slippery surfaces to minimise friction (some plastics, such as polyethylene, have this property).
- It maybe necessary to ‘mix-and-match’ materials to get the best properties of each. For example it might be better in a slurry pump to have a rubber or urethane impeller for its impact properties but a hard metal volute liner for its surface wear properties.
Mike Sondalini – Equipment Longevity Engineer
If you found this interesting, you may like the ebook Process Control Essentials.
Leave a Reply