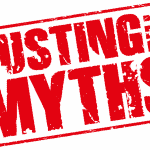
The last article speaks to who should run your storeroom – NOT maintenance. It also leaves us hanging a bit – what should go into the store room to ensure good supply of needed materials, when needed?
Many maintainers will default to the manufacturers’ recommendations for maintenance actions and for spare parts lists. After all, we are paying for those when we buy our equipment and build our plants, so why not follow them? The manufacturers are often seen as highly knowledgeable about whatever it is that they sell to you. In some cases that is true too, particularly where sales of the asset are very high volume (like vehicles). But in most cases, the manufacturers of industrial equipment do not actually use what they sell. They design it, build it and then sell it. They make their money on the initial purchase of the asset and then later on the sales of parts needed to support it. The technical manuals often reflect the thinking of whomever wrote it (probably a junior engineer or designer many years ago) rather than those who use it today.
Vehicles are an exception. There are so many and so much similarity that the sheer volume of experience leading to shared / common knowledge is high. As a rule they all fail in similar ways and need similar maintenance, hence similar parts. Whole industries are based on that – muffler shops, oil change / lube shops, tire shops, engine rebuild shops, body shops, etc. The manufacturers do have a good idea of what happens to their products and what is needed to support them. In those cases, manufacturer recommendations can usually be trusted. In most other cases however, that is simply not the case. The rest of this is about those other cases.
Technical manuals rarely include optional maintenance programs for different operating scenarios. A manual that recommends overhauls does so regardless of usage – heavy use or almost no use in a standby mode – it makes no difference. This is why Reliability Centered Maintenance (RCM) begins with a definition of operating context. It is absolutely critical and it is something about which a manufacturer will invariably have little to know awareness. Manufacturers often have no idea what RCM even is, let alone apply it to their products. So why trust their parts recommendations?
Most of us realize that acquiring all the parts of any asset and building it in your own shop will produce an asset that is far more expensive than the manufacturer would have sold it for. The costs of parts alone will overshadow the assets purchase price, and then consider all your labor. We simply don’t do that though because it makes no economic sense. Take that a bit further. Why do parts cost so much then? Answer – it is how many manufacturers make up for the discounts they are often cornered into offering for the original equipment in order to win the bid. Margins on parts can be much higher than on the original equipment. After all, at that point you (the buyer) are often locked in to using their parts. Warranty conditions will require you to use only Original Equipment Manufacturer (OEM) parts, and your own maintainers will want to ensure that the parts they get are the right parts and of the correct quality. Cheap copies cause problems.
That warranty will also require that you do the manufacturer recommended maintenance. Recommendations that often don’t match your true needs. Anyone who has had success with RCM will tell you that manufacturer recommendations are often flawed.
Even if you follow manufacturers’ recommendations on parts, it’s not uncommon to find yourself wanting parts that are not in your storeroom. Why? The answer lies in the manufacturers’ lack of knowledge of how their assets are actually used and how they actually fail. Don’t take my word for it. If you think they know this information, then ask them to provide you with actual field data on failure rates of their equipment and of the components that comprise their equipment. Good luck with that.
So, having carried out your research, you know what not to do, and you are left with the perplexing question of what to stock in your storeroom.
If you have a storeroom that is well managed by qualified stores persons, and no “squirrel” or “magpie” stores that maintainers love to hide away, then you can reliably stock those fast moving items. If you do have those unofficial satellite stores, chances are they contain some fast moving items that you can easily identify from memory. They may also contain many “just in case” items that should be turned into stores and observed to get a handle on actual usage.
When moving these items that you are unsure about, check to see if they are for equipment you actually have or for something that may no longer be used. It’s not uncommon for parts used on decommissioned equipment to still be hanging around.
If you are doing a lot of planned maintenance work (and I do mean planned, not just scheduled), then review those plans for needed parts. Anything not already in stock is a candidate for stocking but only if you think its usage will justify it. Estimate annual usage (keep in mind that the same item may be used on more than one asset), how many are needed when used, and then let your stores people determine whether it should be stocked using their inventory management equations / formulae. If they cannot do this, or they ask you (the maintainer) for a min / max recommendation, then get outside help – they have some learning to do.
Stores / inventory management needs ongoing information about coming demand for parts. Ideally, if you have done RCM or other failure management analyses, you can forecast what will be allowed to fail (you need parts for those), what will be prevented (you also need parts for those) and what will be predicted using condition monitoring (you need parts for the “finds” that discover during monitoring. You should have frequencies for those tasks and forecasts of how often you will make finds of failures with your condition monitoring. If you can’t forecast that, then you also need some help.
The above forecasts will only work if you can comply with whatever schedule the analysis produces. If your work schedule compliance levels are low, you’ll also have work to do on basic work management / supervisory, planning and scheduling skills.
Solving store room challenges is not just a job for the stores persons. It requires a lot of work from your maintainers too and patience from finance while you make those changes. If stores are a big problem for you now, then you also have problems elsewhere, primarily in maintenance. It is probably better in the short term, to have too much in your stores and avoid production delays, than to have too little and suffer the revenue losses. You’ll need effort in several areas to truly achieve high levels of stores service at low cost.
Very good
It’s such a sad story that I don’t know how to reply, because I have worked for the product manufacturers, spares parts suppliers, and parts’ bins, and my ex-father-in-law stocked parts for Pep Boys. If your aftermarket auto parts didn’t have what you needed, it could have been my fault.
1. Manufacturers, if they’re doing their job should know the age-specific field reliability and failure rate function of every product and part
2. Consumers should know their installed base, BoMs, and spares consumption.
3. Actuarial forecast gives mean demand during lead time
4. Distribution of demand helps set stock levels to satisfy service level
5. Kits based on joint demand distributions
I am so distraught I can’t continue
Choose: lament or do something. Been there done that