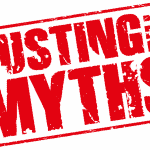
Manufacturers always publish recommended maintenance for users of their products. There are a few myths about this maintenance – one is that it will result in reliable operation of the equipment. In some cases it does, but in most, it does not. Why?
The myth is that the manufacturers always know best how to maintain their designs. Think about that for a minute. How many manufacturers actually use and maintain what they sell? Some do, but not many. If they don’t, then how do they know how their product fails? Moreover, how will they know what to do to avoid it happening? Dig a bit deeper now – even if they operate what they sell, do they operate it in the same way and environment that you use? Let’s assume that like most companies, you buy your parts from the original equipment manufacturer (OEM). Who makes money from those sales? Who makes money if the maintenance program requires use of those parts? Who spends it? Who benefits from after-market sales if the equipment fails? Is it really in the best interest or the capability of the manufacturer to recommend a truly effective maintenance program for your application?
This isn’t so much a myth buster as it is an explanation.
In some cases, particularly large fleets of vehicles, the manufacturer recommendations are based on a lot of accumulated knowledge – their own and their customers’. As a rule, you can believe them and follow them, unless you have some unusual application. But even in those cases, it is not uncommon to find companies stretching the maintenance intervals quite successfully. The manufacturers in those cases know that if you follow their recommendations and it doesn’t work, their reputation could suffer and they could lose future sales. Their recommendations will be conservative (i.e.: applicable to the worst cases) but overall quite valid.
In these cases, where the recommendations are generally pretty good, but you can still improve on them.
In most other situations and asset classes however, that is not the case. The recommendations of the manufacturer should be examined carefully. Do they really apply in your operational environment? Do they really deal with failures that you can realistically expect to see occurring? Do the task frequencies make good sense to you, given your experience with other similar assets?
I am always cautious about manufacturer recommendations that rely heavily on component replacements or overhauls. Firstly, they will consume the most parts; and who benefits from that? But more importantly, do those replacements and overhauls really deal with age or usage related failure modes? Tasks that require you to “inspect and replace if necessary” are a license to print money for the supplier.
To inspect you must disturb or dismantle. In doing that you will need to replace a few parts (e.g.: gaskets, seals, o-rings, bearings). You will expose the internals to dust, dirt, moisture, etc. That sets the stage for failures that could be avoided had you left the item closed up. If you are hurried to do the work (and who isn’t?), there is a good chance a mistake will be made that causes a failure on start up or soon afterwards. If the asset is something that usually runs and is not shut down or started except for failures or maintenance, then there is a substantial risk that operators will make a mistake in either shutting it down or starting it up – more failures, more downtime, more costs for labor and parts …
The other problem with “inspect and replace if necessary” comes from human nature. Mechanics who see a small amount of wear or degradation on something they are inspecting will often want to replace it with a new component. Even though the old one was showing no signs of distress in operation and it is designed to wear, it is often replaced. That drives up costs associated with that work order and unless the replacement component is exactly identical to the one removed (even within manufacturing tolerances), creates other opportunities for other failures to develop.
I use Reliability Centered Maintenance extensively to develop maintenance programs. In almost every case (and there are many that I’ve experienced personally) I’ve seen results quite different from the manufacturers’ recommended maintenance. When the planning and parts identification is done, using RCM results as a basis, there are fewer parts than the manufacturer recommends and they are often different parts as well. Future inventory savings result from that.
In one case of an electrical distribution system switching device we replaced an overhaul at intervals of 2 to 3 years with a program of regularly switching the devices from one position to the other (open / closed and back). That cycling eliminated most failures and by eliminating the overhauls, we eliminated all the infant mortality failures that utility had been experiencing. The cycling task was executed by operational staff, freeing up maintainer time. The overhaul shop was converted to other uses. This resulted in dramatic cost savings.
In another case of a high horsepower diesel propulsion engine (used in mines, railroads and ships) we extended the maintenance intervals by almost double. We also shifted from inspect and replace to condition-based maintenance almost across the board. In the case we worked on (ships) we were able to extend sea time between work periods and get more service out of the vessels.
In a mine we found that an incorrect operating procedure was causing extensive damage to the asset, poor performance and high maintenance costs. Compounding that was the need for a substantial capital investment (nearly $100 M) to make up for the shortfalls in the asset that was being operated incorrectly. In that case, the manufacturer had specified correct procedures – the company had failed to follow them, but didn’t realize it until we did the analysis work. The new operating practices dramatically increased performance, reduced demand for maintenance and both operating and maintenance costs. Unfortunately in that case, the capital cost was already spent, but operation of the new asset was no longer needed. There were operational cost savings (energy, operating labor and maintenance of the new asset).
In a rail transit system we identified different maintenance routines for the different instances of the same assets depending on their location within the system and the amount of traffic and use they experienced. Only one task was the same as the manufacturer had recommended. Frequencies and other tasks were dramatically different. The result was a big maintenance cost savings, reduced risk of failure and freeing up of maintainers for other tasks.
Finally, what about warranty? If you don’t follow what the manufacturer says, you invalidate any warranty BEYOND basic quality and workmanship. That is always standard on new, and often times, refurbished items. Warranty is like insurance. You only win if you lose, and you pay for the privilege. Extended warranty costs 2 to 3% of capital cost. So does RCM. For capital cost purposes, it is wash. But what about extended benefits? RCM is “live” (if you do it right) and will ensure long term sustainable high performance. The warranty doesn’t do that, and the PM program from the manufacturer (as described above) is often mis-leading.
The manufacturer gives you a warranty that you pay for, insists you follow a program that ensure future sales at your expense, and threatens not to make good on it if you fail to follow it. In many cases, companies can’t stick to their PM programs very well and they will highly likely run afoul of this contractual condition anyway. In my opinion, warranties that go beyond quality and workmanship are a bad investment. Put your money into RCM and get far more payback with only two conditions – 1. you must do the RCM properly, and 2. you must follow the PM program it produces. Payback will be huge!
In conclusion – take manufacturer’s recommendations only as initial guidance. You are better served to use RCM to determine your maintenance requirements in almost every case.
For new installations I think OEM maintenance plan should be followed but as operations take over, log history, operational parameters, machine load factor plays important role on planned maintenance.
More condition monitoring methods should be adapted before taking major overhaul
Neeraj – As mentioned above, there are cases like you describe, but as a more general rule, that won’t work as well as thinking through your program with RCM.