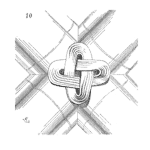
This failure occurred on a turbine driven boiler feedwater pump (TDBFP) at a fossil fuel power plant. The pump in question is an outboard boiler feed pump. Plant is operating normally when unexpectedly pump shuts down and causes a forced outage.
Here is a basic process flow diagram for this process.

When investigators were able to safely access the failed components, the following was found:
1. All inboard components are detached (see below)
2. Pump had lift and could be rotated by hand
3. Strainer was not in place
4. Turbine driven boiler feedwater pump (TDBFP) opened and no damage was evident (including no damage to impeller and/or housing)

Here is a full picture of the coupling (pics in the heading seem to get cut off by LI limitations).

Given the limited preliminary physical data provided, what anomalies do we see, that need to be explained?
UPDATED POST 5.31.17 (ID# TDBFP.5.24.17)
Why were there different grade bolts as well as balancing weights on the coupling?
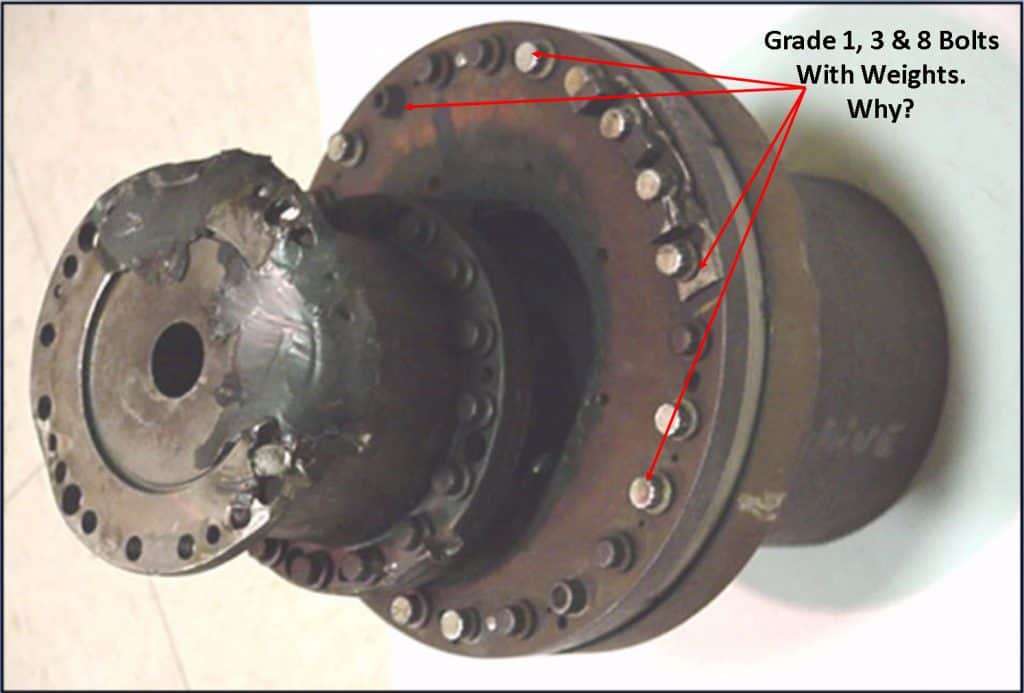
Here is the summary path(s) to failure for the boiler feed water pump case study above.
1. ‘Procedure/specs for coupling fasteners were inadequate’ & ‘No QC inspection required during installation/repair’ [Latent Root Causes/Organizational System Related]>
2. Results in ‘Field Selection Error’ when retrieving replacement coupling bolts [Human Root Cause/Decision Error Related] >
3. Results in wrong bolts installed in the coupling [Physical Root Cause] >
4. Results in inappropriate bolt coming loose and locking up turning gear>
5. Results in pump being overloaded>
6. Results in coupling failing>
7. Results in pump failing to act as a primary mover>
8. Results in turbine driven boiler feed pump to shut down in operation>
9. Results in plant tripping due to loss of boiler feed water
This is a summary of one of the paths to failure; to view the full RCA, please review the Boiler Feed Water RCA video case study on YouTube.
As always, all comments, suggestions, questions and debate are welcome!
Leave a Reply