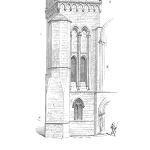
PREVENTIVE MAINTENANCE STRATEGY IN A PLANT WELLNESS WAY EAM SYSTEM-OF-RELIABILITY
IN A PWW EAM SYSTEM-OF-RELIABILITY, PREVENTIVE MAINTENANCE STRATEGY IS TO REPLACE PARTS WHEN EXCESSIVE STRESS BUILD-UPS IN THEIR MICRO-STRUCTURE
—
Once you adopt the new Preventive Maintenance strategy, practices and timing, your operating equipment risk drops so low that you don’t need expensive condition monitoring solutions
Old Preventive Maintenance was reserved only for wearing parts renewal. The new view of Preventive Maintenance strategy is to use PvM to ensure zero parts failure from stress accumulation within component micro-structures. Without parts failure from over-stress you can get zero equipment failure. It’s a foundational concept used in Plant Wellness Way life-cycle asset management strategy.
In this article, Preventive Maintenance has the acronym ‘PvM’. It’s a simple way to differentiate the new view of thinking about Preventive Maintenance from the old paradigm of replacing worn-out parts. We relegate the old PM acronym to use for Planned Maintenance (PM).
Preventive Maintenance is no longer only for parts that wear-out. In new Preventive Maintenance thinking you replace over-stressed parts causing too much risk. As well as the parts that are worn-out, you intentionally replace parts that are tired, aged, and degraded just before they fail. The image below encapsulates the new view of Preventive Maintenance strategy—create a life cycle asset management system that eliminates the chance of component failure, and renew a part as PvM when internal stress accumulation becomes too risky.
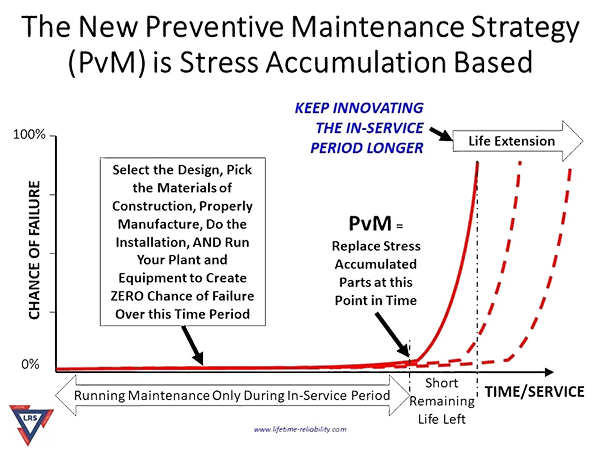
The choice when to do PvM is wholly micro-structure stress dependent. Preventive Maintenance is used everywhere there is excessive stress accumulation! You proactively manage and reduce stress accumulation within a component to control when the part needs to be replaced. Once you know when the service duty stresses have built up too much, you know when to renew the part. Start counting and measuring stress accumulation and PvM strategy becomes a low cost and simple way to get and maintain utmost plant and equipment reliability.
TO GET ALL THE BENEFITS AND SAVINGS POSSIBLE FROM PREVENTIVE MAINTENANCE, YOU NEED TO UNDERSTAND WHAT PVM IS REALLY ALL ABOUT
Your aim is to intentionally create the ‘knee’ in the asset wellness curve shown in the image. You use your life cycle asset management system to give you zero chance of failure during operating life. You also use your life cycle asset management system to control where the knee is located and replicate that point over and over again. By using a faithful system that repeats the position of the bend, you no longer need to do condition monitoring. Your life cycle asset management processes ensure zero chance of parts failure until the part has built-up so much stress that the chance of failure rapidly rises.
I love using PvM everywhere it can possibly be applied. It keeps maintenance simple to plan and to do. It minimizes your spare parts inventory, since you buy parts just-in-time. You don’t need a warehouse full of spares because you replace parts before they break. Provided you have world class Precision Maintenance (PrM) capability, you’d use PvM a lot to get zero breakdowns.
You must always use parts that are in “as-new condition” for Preventive Maintenance replacement or rebuild. Old parts that have been in service contain accumulated stresses and micro-structure damage. If you use old parts, or reclaim parts and refurbish them for reuse, you have no idea how much stresses they contain and how much life remains before they fail. Only with new parts can you be certain of what internal stresses are present and how stressed the micro-structure actually is. If you decide to use old parts in your plant and machines, you’ll also need to introduce condition monitoring of them, because you have no idea when the part will fail. At least with condition monitoring, you have a good chance of spotting a coming failure early enough to prevent breakdown.
PARTS OVER-STRESS PREVENTIVE MAINTENANCE STRATEGY IS FUNDAMENTAL IN PLANT WELLNESS WAY EAM
Creating zero chance of parts failure and controlling the bend in the wellness curve are achieved with Plant Wellness Way Enterprise Asset Management methodology. Plant Wellness Way EAM puts world-class reliability, maintenance, and operating strategy and practices into your organization’s processes. Stress reduction and stress prevention are key tactics that you embed into your company when Plant Wellness Way EAM is used to get maximum plant and equipment reliability. You purposely design and build your life cycle asset management processes, supply chain processes, maintenance processes, and operating processes to get zero chance of failure during a part’s service lifetime.
Moving the knee further and further along the service life axis is done through innovation. The innovations can come from anywhere and from anyone. Every improvement in operating life that extends the duration between preventive maintenance renewals is a good improvement to do. The most likely people who have useful innovations will be the operators, maintainers, maintenance engineers, and the original equipment manufacturer.
THOUGHTS AND COMMENTS ON MEANINGFUL DEFINITIONS FOR PREVENTIVE MAINTENANCE
The text book definition of Preventive Maintenance depends on which text book you read. Today, Saturday 9 December 2017, there are four different definitions for Preventive Maintenance on Wikipedia. None of the explanations are completely correct, and none of the four agree with each other. In your own company you must have only one definition of Preventive Maintenance, with a meaning that is agreed by everyone across the organization, world-wide.
If you replace a part with a new part using a criterion from its service life, you are doing preventive maintenance. Look for 1) preset time period, or service duty, and 2) the part is replaced regardless of condition. Then you have found a Preventive Maintenance job. Criteria used to schedule old-style Preventive Maintenance include time-in-service; production throughput; number of cycles; age from new for degrading materials, like rubber; etc.
When a scheduled maintenance work order that people call a “PM work order” asks you to check, or inspect, or to observe, or to do a test, or take a measurement, and, depending on what you find, you replace the part or return it back to standard, you are doing condition based maintenance (CBM). CBM is also known as Predictive Maintenance (PdM). It’s easy to differentiate PvM from PdM. In PdM, the part’s observed condition determines if it is maintained. For PdM you look for 1) condition check(s), and 2) on-condition rectification.
Yes, both PdM and PvM are Planned Maintenance (PM) when they appear as scheduled maintenance work, but each is a totally different job type with completely different purposes to the other. Be sure your Computerized Maintenance Management System (CMMS) always differentiates the type of a planned maintenance work order—clearly identify and distinguish PdM from PvM. Otherwise you confuse everyone in your company and supply chain for evermore.
The debate that often starts now is, if the condition indicates that rectification is required, is the restitution work categorized as Corrective Maintenance (CM)?
In the Maintenance Manager role, I’d ask my people to do the following. If the rectification can be done simply, safely and correctly immediately after the on-condition check indicates a problem, then do the restitution on the same PdM work order, and provide a complete and thorough job history of what was done. For example, when a drive belt needs alignment, do it immediately and record the details in the PdM work order history. If instead, the restitution requires more than what can be done at that opportunity, or the opportunity cannot be taken for production, safety, or supply chain reasons (etc.), then close the PdM work with a complete and thorough job history, and open a Corrective Maintenance work order to do the repair. Be sure to link the ‘child’ CM work order to the parent ‘PdM’ work order so the maintenance history records tell the repair followed the discovery of an on-condition problem.
All the very best to you,
Mike Sondalini | Plant Wellness Way EAM System-of-Reliability
A question from a Reader: “Could I have more insight of the terms and their benefits, and also, how to do the PdM and PvM as Planned Maintenance (PM)?”
I have seen PM defined as Preventive Maintenance and also as Planned Maintenance—that’s a sure way to cause confusion. To help people clarify the meaning of the acronym ‘PM’ it must be exactly defined. In an organization there must not be two different meanings for ‘PM’.
In the article, PM is set as Planned Maintenance, which is maintenance work that is reviewed and prepared for executing, i.e. a work pack for the job is completed. Once PM is first defined as Planned Maintenance it cannot again be used to specify Preventive Maintenance. In the article ‘PvM’ is made the acronym for Preventive Maintenance. Preventive Maintenance is the recurring replacement of degrading equipment items before they get to a condition that greatly increases the risk of equipment failure.
Predictive Maintenance has the acronym PdM, which fortunately is the standard used around the English-speaking world. Predictive Maintenance is the inspection of equipment items to review their in-service condition and determine their remaining service-life.
Using the words ‘Planned Maintenance’ implies the maintenance work is organized, with all the requirements to complete the job from start to finish known and specified. Preventive Maintenance jobs become Planned Maintenance when they are reviewed and prepared for execution. Similarly, Predictive Maintenance jobs become Planned Maintenance when they are reviewed and prepared for execution.
Preventive Maintenance that recurs, e.g. 3-monthly, annually, .etc., should have a work pack that was developed when the PvM job was first established. The existence of the work pack makes recurring PvM jobs Planned Maintenance. The same applies for recurring PdM jobs—when they were first established a work pack covering the condition monitoring inspection requirements was developed. If you run a forecast of future maintenance work the list will contain PvM and PdM jobs. PvM work orders will have replacement tasks and PdM work orders will have inspection tasks. Each category is a different type of maintenance work, but the work orders are still both Planned Maintenance.
Leave a Reply